The Processing of Rubber Cable Line Joints
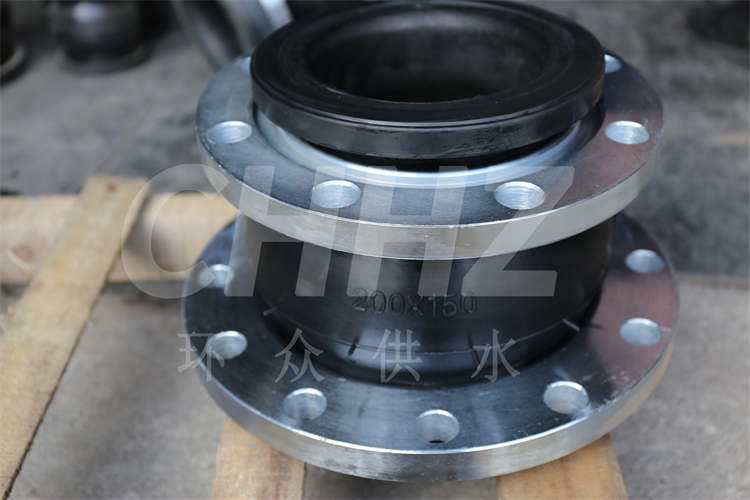
Rubber cable line joints are essential components in electrical systems, providing a secure and reliable connection between cables. In this article, we will examine the processing methods involved in manufacturing rubber cable line joints, emphasizing the crucial steps and considerations in producing high-quality and durable connection solutions.
Material Selection: The process of manufacturing rubber cable line joints begins with the careful selection of suitable elastomeric materials. Natural rubber, synthetic rubber compounds, and specialized polymers are common choices due to their excellent electrical insulation properties, mechanical flexibility, and resistance to various environmental factors such as moisture, oils, and ultraviolet radiation. The material selection is tailored to meet the specific requirements of electrical applications, ensuring optimal performance and longevity of the cable line joints.
Molding and Vulcanization: The production of rubber cable line joints involves precision molding processes to shape the raw rubber material into the desired form. Compression molding or injection molding techniques are employed to create intricate shapes and structures, accommodating the cable diameters and connection configurations. Subsequently, the molded rubber components undergo vulcanization, a critical step that enhances the material's strength, resilience, and resistance to electrical and thermal stress.
Core and Insulation Integration: In the manufacturing process, the rubber cable line joints are designed to incorporate the cable cores and insulation. This integration ensures a seamless transition and electrical continuity between cables, minimizing electrical resistance and heat generation at the joint interface. Advanced insulation materials, such as cross-linked polyethylene (XLPE), are often employed to enhance the dielectric strength and thermal stability of the cable joints.
Shielding and Grounding Arrangement: Given the importance of electromagnetic shielding and grounding in electrical systems, the manufacturing process includes provisions for shielding layers and grounding arrangements within the cable line joints. Metallic shielding materials, such as aluminum or copper foil, are incorporated to mitigate electromagnetic interference and ensure signal integrity. Furthermore, effective grounding features are integrated to maintain electrical safety and protect against potential voltage surges or faults.
Quality Control and Testing: Stringent quality control measures are implemented throughout the manufacturing process to validate the dimensional accuracy, material consistency, and electrical performance of the rubber cable line joints. Comprehensive electrical testing, including insulation resistance testing, high-voltage withstand testing, and resistance measurements, is conducted to verify the insulation and conductivity characteristics of the joints, ensuring compliance with international electrical standards.
Protection and Encapsulation: In many applications, rubber cable line joints undergo protective treatments, such as encapsulation with insulating resins or sheathing with durable outer materials. These protective measures safeguard the joints against mechanical damage, moisture ingress, and environmental degradation, thereby extending their service life and maintaining electrical integrity in challenging operating conditions.
In summary, the manufacturing processes for rubber cable line joints encompass material selection, molding, core and insulation integration, shielding, grounding arrangement, quality control, testing, and protection. By adhering to stringent production standards and leveraging advanced materials and techniques, manufacturers can deliver high-performance cable line joints that ensure the reliability, safety, and efficiency of electrical systems across various industries and applications.
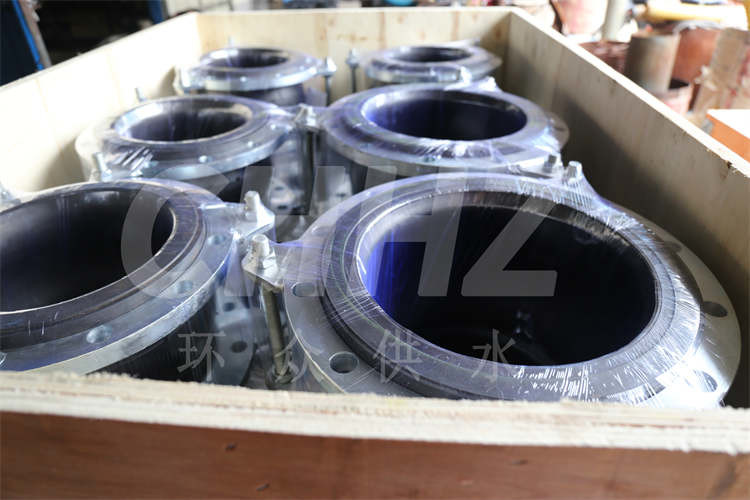