Rubber Flexible Joints in Piping Systems
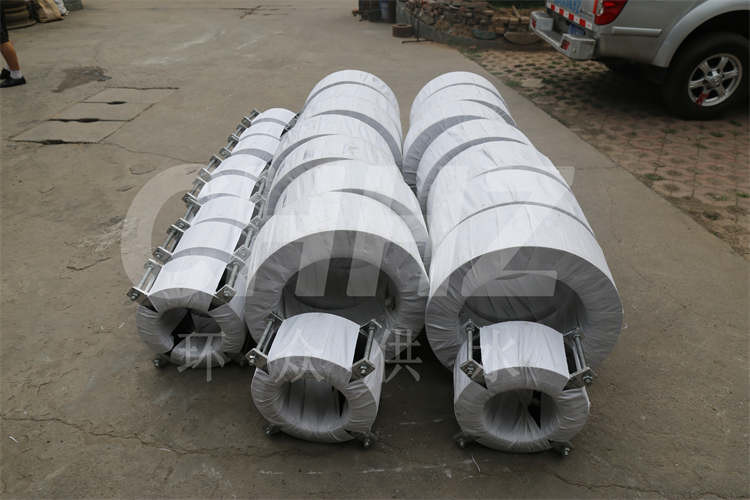
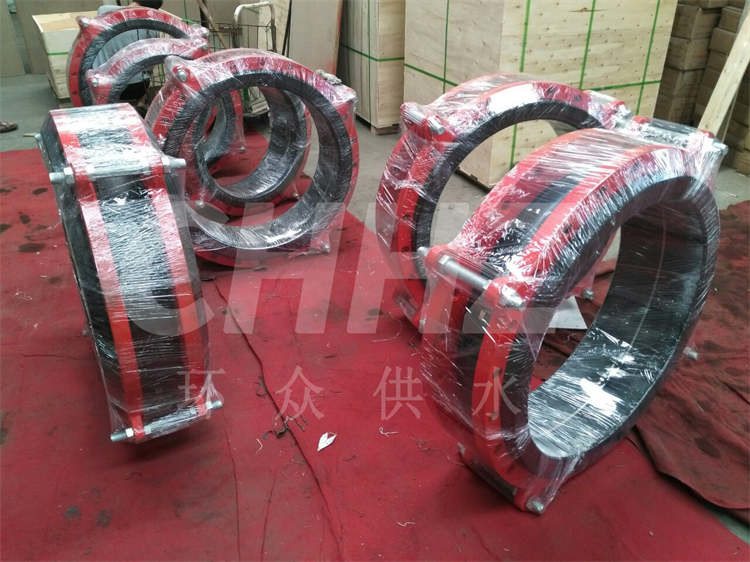
Rubber flexible joints, also known as rubber expansion joints, play a crucial role in piping systems by providing flexibility, vibration isolation, and accommodating movements due to thermal expansion, and settling. These components are widely used in various industries to mitigate stress and maintain the integrity of pipelines. In this article, we will explore the key aspects of rubber flexible joints and discuss their benefits in piping applications.
Material Composition: Rubber flexible joints are typically constructed using high-grade elastomeric materials such as natural rubber, neoprene, EPDM, or nitrile rubber. These materials are chosen for their exceptional resilience, flexibility, and resistance to chemicals and weathering. Reinforcement materials such as nylon, polyester, or metal rings may be added to enhance the structural strength and load-bearing capacity of the joints.
Flexibility and Movement Absorption: One of the primary functions of rubber flexible joints is to accommodate movements and misalignments within the piping system. They can absorb axial, lateral, and angular movements, as well as provide vibration and noise attenuation. This capability helps to reduce stress on the pipeline components, extend their service life, and minimize the risk of leaks or ruptures.
Sealing and Leak Prevention: Rubber flexible joints act as effective seals within piping systems, helping to prevent leakage of fluids and gases. Their design and construction ensure a secure and reliable sealing connection, even under fluctuating pressures and temperatures. This feature is essential for maintaining the efficiency and safety of the overall pipeline network.
Corrosion Resistance and Maintenance Reduction: In corrosive or abrasive environments, rubber flexible joints provide a non-corrosive solution that mitigates the need for frequent maintenance or replacement of rigid pipe connections. By isolating the piping system from vibrations, thermal stresses, and mechanical movements, these joints contribute to the overall longevity and reliability of the infrastructure.
Variety of Applications: Rubber flexible joints find application in a wide range of industries, including chemical processing, water treatment, power generation, HVAC systems, and marine engineering. They are utilized in various piping systems, including those conveying water, wastewater, chemicals, gases, and slurries. The versatility of rubber flexible joints makes them suitable for both industrial and commercial uses.
Installation and Maintenance: Proper installation and periodic inspection and maintenance are essential for ensuring the optimal performance of rubber flexible joints. Installation guidelines provided by manufacturers should be followed, and regular inspections should be carried out to check for signs of wear, damage, or fatigue in the joints.
In conclusion, rubber flexible joints are vital components in piping systems, offering flexibility, movement absorption, sealing, and corrosion resistance. Their ability to reduce stress on piping components and provide efficient vibration isolation makes them indispensable in ensuring the integrity and longevity of pipelines across diverse industries and applications. Well-designed and properly maintained rubber flexible joints contribute to the overall efficiency, safety, and reliability of piping systems.
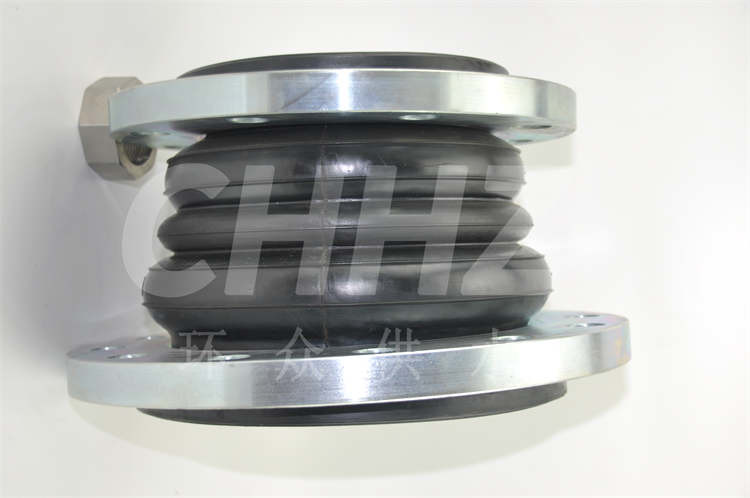