Molding Process of Rubber Cable Joint
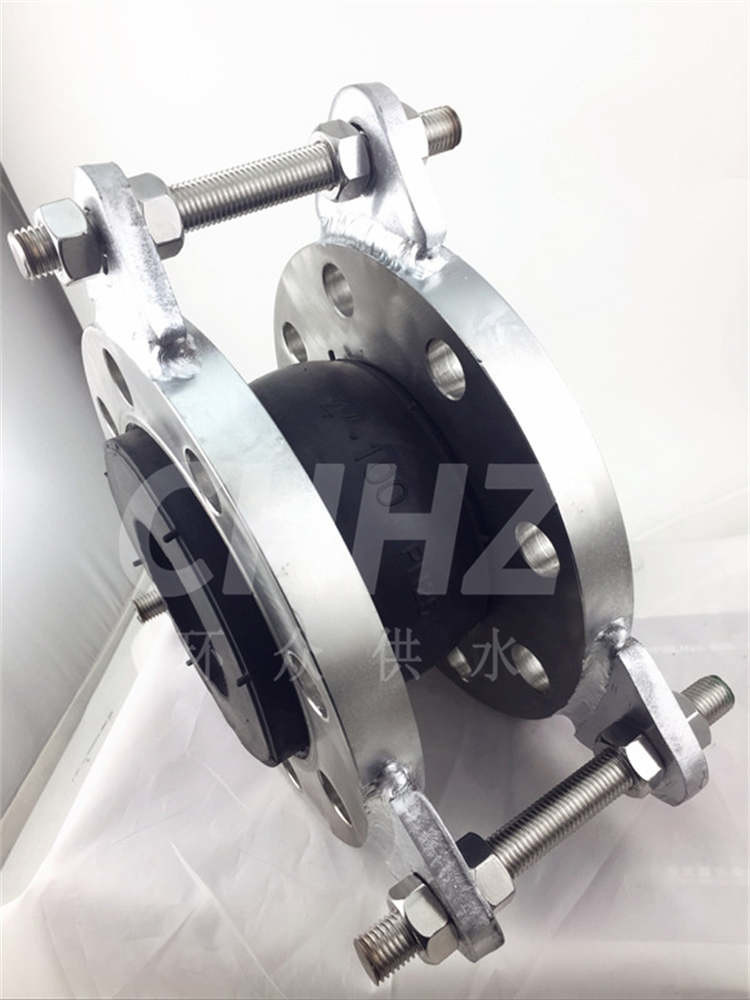
Introduction Rubber cable joints are pivotal for ensuring secure and efficient connections within electrical systems. The molding process for manufacturing rubber cable joints is a critical aspect that dictates the integrity and performance of the final product. In this article, we will delve into the comprehensive molding process of rubber cable joints, highlighting the key stages involved in their production.
Raw Material Preparation The molding process commences with the meticulous preparation of raw materials. High-quality rubber compounds, reinforcing agents, and other additives are precisely weighed and mixed to achieve the desired physical and chemical properties. The carefully controlled formulation of the rubber compound is fundamental in ensuring the subsequent molding stages yield products with exceptional durability, electrical insulation, and chemical resistance.
Mold Design and Fabrication The next stage involves the design and fabrication of molds tailored to the specific dimensions and configurations of the cable joint. Utilizing computer-aided design (CAD) software and precision machining techniques, molds are meticulously crafted to exacting tolerances, ensuring uniformity and consistency in the final product. The molds are engineered to accommodate the complex geometry of cable joints, including intricate sealing features and connection interfaces.
Injection Molding Injection molding serves as the core process for shaping rubber cable joints. The prepared rubber compound is heated to a precise temperature and injected into the cavities of the mold under high pressure. This process allows for the complete filling of the mold, resulting in the formation of the intricate details and geometry of the cable joint. The controlled cooling cycle following injection ensures the accurate dimensional stability and material properties essential for the functionality of the joint.
Curing and Vulcanization After the injection process, the molded cable joints undergo curing and vulcanization in specialized ovens or autoclaves. Controlled heat and pressure facilitate the cross-linking of polymer chains within the rubber compound, imparting the requisite strength, resilience, and thermal stability to the finished product. The precise curing parameters are tailored to the specific formulation of the rubber compound, ensuring optimal performance attributes are attained.
Trimming and Finishing Upon completion of curing, the molded cable joints undergo meticulous trimming and finishing processes. Excess rubber flash and imperfections are carefully removed, and the surfaces are refined to achieve the specified dimensional accuracy and aesthetic appearance. Any necessary post-curing treatments, such as the application of protective coatings or surface treatments, are performed to enhance the durability and weather resistance of the cable joints.
Quality Assurance and Testing Throughout the entire molding process, stringent quality control measures are executed to verify the dimensional accuracy, material properties, and performance characteristics of the rubber cable joints. Sample products undergo comprehensive testing, including electrical insulation, tensile strength, and environmental exposure evaluations to ensure conformity with industry standards and customer specifications.
Conclusion The molding process of rubber cable joints demands precision, expertise, and advanced manufacturing techniques to produce components that deliver exceptional electrical and mechanical performance. By adhering to rigorous quality standards and meticulous attention to detail in each stage of production, manufacturers can consistently deliver reliable and durable rubber cable joints for diverse electrical applications.
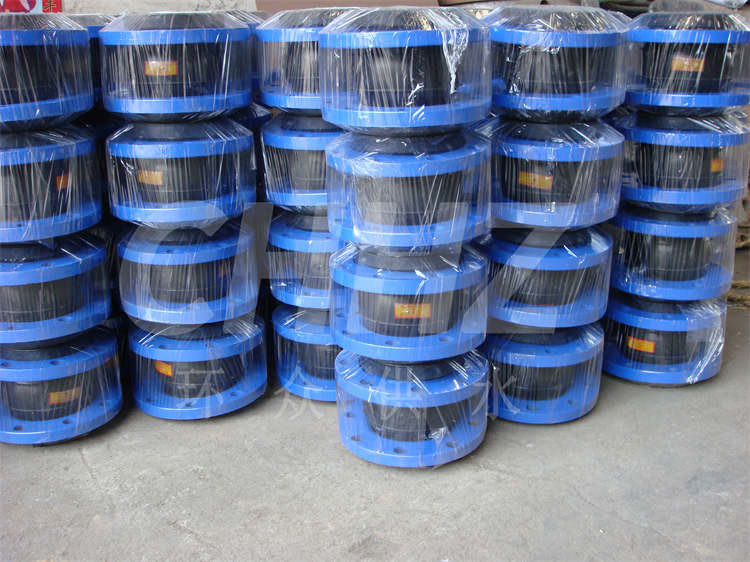