Flexible Joint: The Fusion of Metal and Rubber
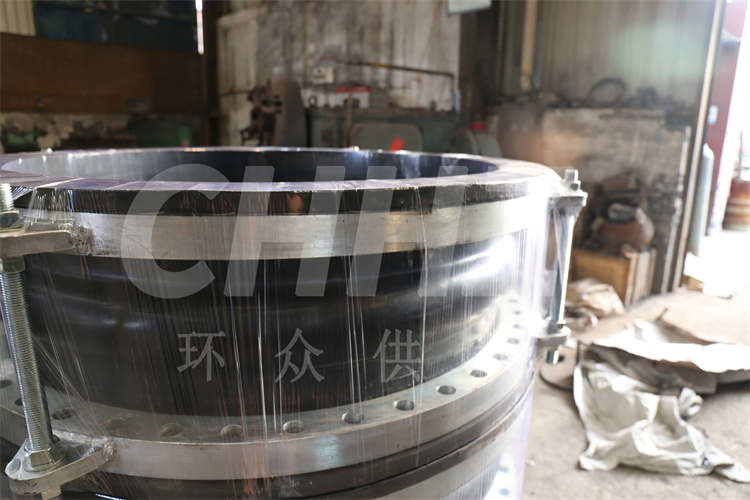
Introduction Flexible joints, adept at absorbing vibrations and accommodating movement, are crucial components in various mechanical and industrial systems. The amalgamation of metal and rubber in the fabrication of flexible joints offers a synergistic blend of strength, resilience, and adaptability. In this article, we explore the characteristics, manufacturing process, and applications of metal-rubber flexible joints, shedding light on their pivotal role in engineering.
Properties of Metal-Rubber Flexible Joints The unique combination of metal and rubber in flexible joints bestows them with a spectrum of advantageous properties. The metal component confers structural stability, tensile strength, and resistance to compressive forces, while the rubber element endows the joint with flexibility, vibration damping, and shock absorption capabilities. This symbiotic relationship allows the flexible joint to effectively mitigate the transmitted forces, minimize wear on adjoining components, and enhance the overall system durability.
Manufacturing Process The manufacturing process of metal-rubber flexible joints encompasses several intricate stages. It commences with the preparation of high-quality rubber compounds, reinforced with additives to optimize mechanical properties. Concurrently, precision-engineered metal components are fabricated, tailored to the specific dimensions and load-bearing requirements of the joint. Subsequently, the rubber and metal elements undergo a meticulous bonding process utilizing advanced adhesion techniques or vulcanization, ensuring a robust and enduring union between the two materials. The finalized assembly undergoes rigorous quality testing to validate its mechanical and material properties.
Applications Metal-rubber flexible joints find widespread utilization in diverse applications across industries. In automotive systems, they are employed in exhaust systems and suspension assemblies to isolate engine vibrations and absorb road-induced shocks, thereby enhancing passenger comfort and prolonging the lifespan of components. Within machinery and equipment, these flexible joints are instrumental in mitigating misalignments, reducing noise, and safeguarding connected components from excessive stress. Furthermore, they are integral in piping systems to accommodate thermal expansion and contraction, thereby averting structural damage and leaks.
Advantages and Considerations The integration of metal and rubber confers a multitude of advantages to flexible joints. Their ability to effectively mitigate vibrations and movements substantially reduces maintenance requirements and downtime, thereby contributing to enhanced operational efficiency. Nonetheless, proper material selection and design considerations are imperative to ensure optimal performance and longevity. Factors such as environmental exposure, temperature variations, and mechanical loads necessitate precise engineering of flexible joints to meet the specific demands of each application.
Conclusion The fusion of metal and rubber in flexible joints exemplifies a harmonious blend of structural integrity and adaptability, serving as a cornerstone in optimizing system performance and longevity. By virtue of their ability to attenuate vibrations, accommodate movements, and safeguard mechanical systems, metal-rubber flexible joints continue to be indispensable in a myriad of industrial and mechanical applications, underscoring their significance in engineering and manufacturing.
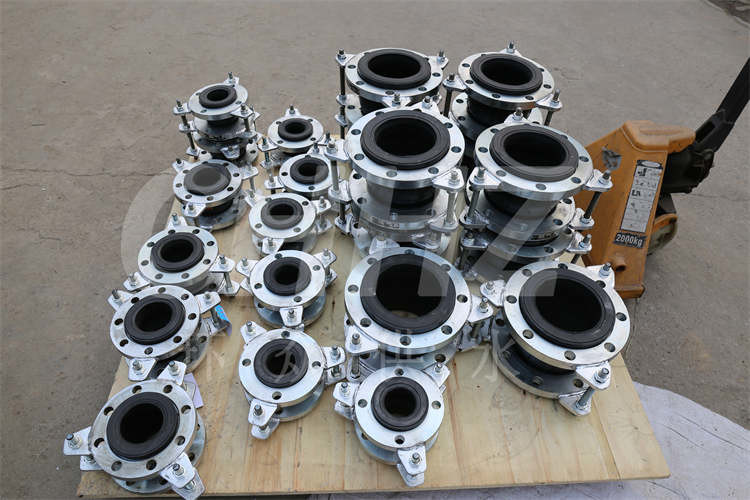