Manufacturing of Rubber Expansion Joints for Varying Diameters
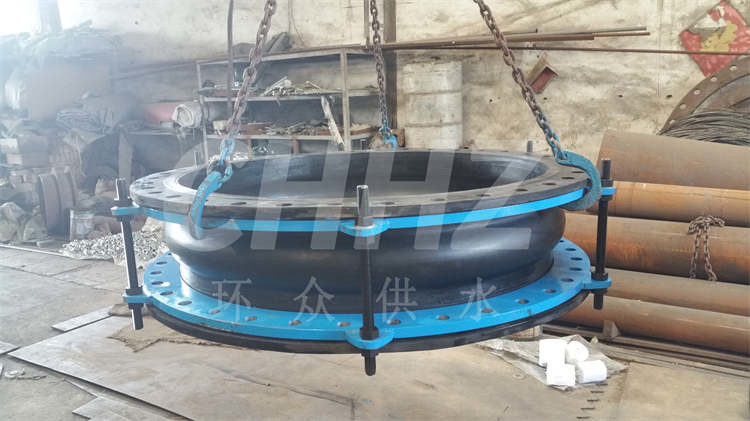
Introduction Rubber expansion joints, also known as rubber flexible connectors, are vital components in pipelines and ducting systems due to their ability to absorb thermal expansion, vibration, and misalignment. In this article, we delve into the manufacturing processes involved in producing rubber expansion joints designed for varying diameters, exploring the materials, fabrication techniques, and quality assessments crucial for their successful production.
Materials Selection The manufacturing process of rubber expansion joints commences with the selection of high-quality rubber compounds. These compounds are chosen based on their resilience to environmental factors, resistance to chemical corrosion, and capacity to endure varying temperatures and pressures. The reinforcement materials, such as nylon, polyester, or aramid fibers, are carefully chosen to impart tensile strength and dimensional stability to the expansion joint. Additionally, metal components, typically made of stainless steel or galvanized steel, are integrated to provide structural support and enhance the joint's resistance to external forces and abrasion.
Fabrication Techniques The fabrication of rubber expansion joints for varying diameters involves precision engineering and assembly procedures. Using specialized molds, the rubber compounds are molded into the desired shape, taking into account the specific size and geometry required for accommodating the varying pipe diameters. Subsequently, the integrated metal reinforcements are strategically positioned within the rubber structure to ensure adequate support and load-bearing capacity. The assembly is then subjected to compression molding or vulcanization processes to create a durable and cohesive bond between the rubber and metal components. This ensures the integrity and longevity of the expansion joint, enabling it to withstand the rigors of industrial applications.
Quality Assessments Stringent quality assessments are integral to the manufacturing process of rubber expansion joints. Each joint undergoes thorough inspections, including dimensional verification, material integrity tests, and pressure resistance evaluations. In addition, non-destructive testing methods such as X-ray inspection and ultrasound are employed to detect any defects or imperfections within the joint structure. This meticulous quality control process guarantees that the rubber expansion joints meet industry standards and performance requirements, ensuring their reliability and longevity in service.
Applications and Advantages Rubber expansion joints designed for varying diameters find diverse applications in industrial and commercial sectors. They are pivotal in piping systems, ducting, and HVAC installations to compensate for thermal expansion, absorb vibrations, and mitigate misalignments. The ability to accommodate varying pipe diameters enhances their versatility, making them suitable for a wide range of applications. The integration of high-quality rubber and metal components equips these expansion joints with attributes such as chemical resistance, flexibility, and durability, bolstering their performance in demanding environments.
Conclusion The manufacturing of rubber expansion joints tailored for varying diameters necessitates a meticulous approach, from materials selection to quality assessments, to ensure the production of reliable and durable components. By adhering to stringent fabrication standards and leveraging advanced techniques, manufacturers can meet the diverse requirements of industrial piping and ducting systems, offering effective solutions for accommodating thermal expansion and maintaining system integrity. The seamless fusion of rubber and metal components in these expansion joints underscores their significance in optimizing the performance and longevity of diverse engineering systems.
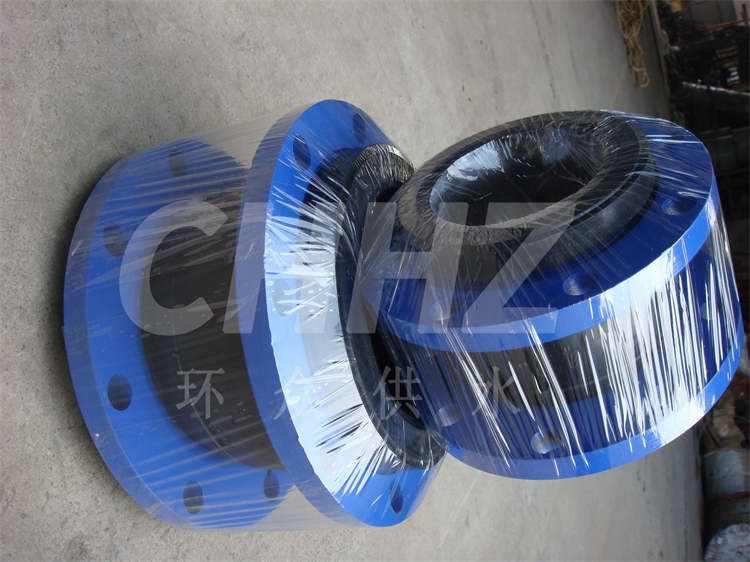