The Manufacture of Rubber Oil Hose Connectors for Automobiles
Rubber oil hose connectors play a crucial role in the safe and efficient operation of automobiles. These connectors are responsible for ensuring the proper flow of oil and fuel to various parts of the vehicle, such as the engine and transmission. In this article, we will explore the process of manufacturing rubber oil hose connectors, highlighting the key steps involved in their production.
One of the primary materials used in the manufacture of rubber oil hose connectors is synthetic rubber, which is known for its durability, flexibility, and resistance to oil and fuel. The process begins with the selection of high-quality synthetic rubber, which is then subjected to a series of treatments to enhance its properties. This may include the addition of reinforcing materials such as fibers or fabric to improve the strength of the rubber.
Once the rubber material has been prepared, it is ready to be molded into the desired shape of the hose connector. This is typically achieved through a process known as injection molding, in which the rubber material is heated and forced into a mold cavity under high pressure. The mold is designed to give the connector its specific shape and features, such as the connection points and sealing surfaces.
After the rubber material has been molded, it undergoes a curing process to ensure its stability and strength. Curing typically involves subjecting the rubber to heat and pressure for a specific period, allowing it to set and achieve its final properties. This step is critical in ensuring that the rubber oil hose connector can withstand the harsh conditions it will encounter in an automobile engine compartment.
In addition to the rubber material, the manufacture of oil hose connectors also involves the production of metal fittings that are used to connect the hoses to various vehicle components. These fittings are typically made from materials such as stainless steel or aluminum, which offer high strength and corrosion resistance. The metal fittings are precision-engineered to ensure a secure and leak-free connection between the hose and the vehicle's oil system.
Once the rubber connectors and metal fittings have been manufactured, they undergo rigorous quality control checks to ensure that they meet the required specifications and standards. This may involve testing for factors such as pressure resistance, chemical compatibility, and dimensional accuracy. Only after passing these tests are the connectors deemed fit for use in automotive applications.
In conclusion, the manufacture of rubber oil hose connectors for automobiles involves a series of precise and meticulous steps, from the selection of raw materials to the production of the final product. The careful coordination of rubber molding, metal fitting production, and quality control is essential in ensuring that the connectors meet the stringent requirements of today's automotive industry. Through this process, manufacturers can deliver high-quality and reliable components that contribute to the safe and efficient operation of vehicles around the world.
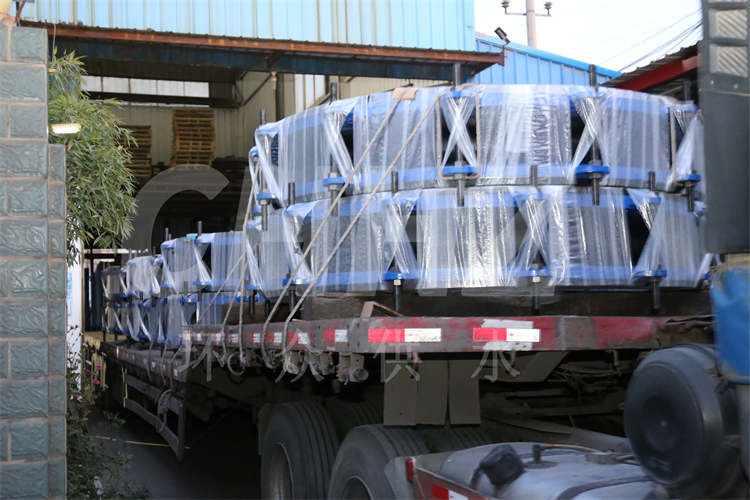