Sulphurization Process of Rubber Hose Joints
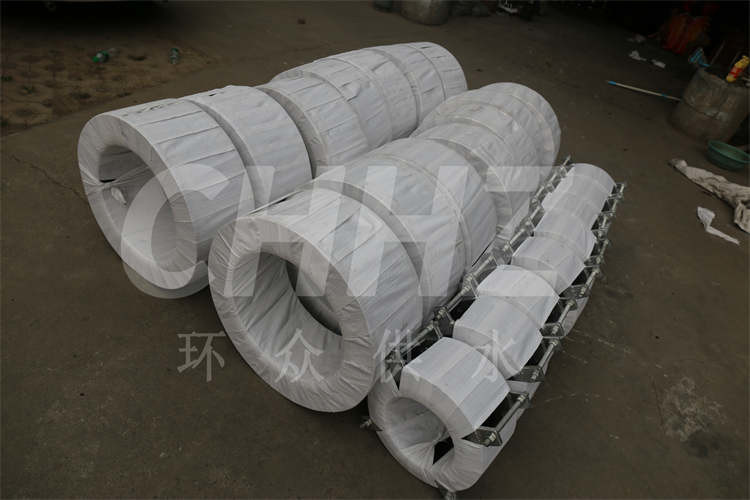
Introduction:The sulphurization process plays a critical role in the production of rubber hose joints, enhancing the physical and chemical properties of the materials to achieve the desired performance characteristics. This article outlines the key aspects of the sulphurization process for rubber hose joints, covering the methods and benefits associated with this essential manufacturing step.
Sulphurization Process Methods:
1. Compression Molding: In this method, uncured rubber compounds are placed into a mold cavity and exposed to heat and pressure. The addition of a sulphur-based curing agent initiates the chemical reaction, resulting in the cross-linking of polymer chains and the formation of a cured rubber hose joint.
2. Continuous Vulcanization: In this method, the uncured rubber compound is extruded through a heated die, where the combination of heat, pressure, and sulphur-based curing agents facilitates the continuous vulcanization of the rubber material to form the hose joint.
3. Steam Vulcanization: Steam vulcanization involves exposing the rubber hose joint to high-pressure steam in a controlled environment. The heat and moisture provided by the steam activate the sulphur curing agents, leading to cross-linking within the rubber compound and the formation of a cured hose joint.
Benefits of Sulphurization Process:
1. Improved Mechanical Properties: Sulphurization enables the formation of cross-links between polymer chains, enhancing the strength, elasticity, and durability of the rubber hose joints. This results in improved tensile strength, tear resistance, and abrasion resistance, making the joints suitable for a wide range of industrial applications.
2. Enhanced Chemical Resistance: The sulphurization process imparts chemical resistance to the rubber hose joints, allowing them to withstand exposure to various fluids, oils, solvents, and environmental conditions without undergoing degradation. This ensures the longevity and reliability of the joints in demanding operational environments.
3. Thermal Stability: Sulphurization contributes to the thermal stability of the rubber hose joints, enabling them to withstand elevated temperatures without softening or losing their structural integrity. This is essential for applications that involve exposure to high-temperature fluids or environmental conditions.
4. Dimensional Stability: Through the sulphurization process, the rubber hose joints attain improved dimensional stability, maintaining their shape, size, and structural integrity during operation. This ensures proper sealing and fitting, reducing the risk of leakage and enhancing the overall performance of the joints.
Conclusion:The sulphurization process is a vital step in the manufacturing of rubber hose joints, imparting essential properties that are fundamental to their performance and durability. By employing suitable sulphurization methods, manufacturers can achieve the desired mechanical, chemical, and thermal characteristics in rubber hose joints, making them suitable for a wide range of industrial applications. Understanding the significance of sulphurization in the production of rubber hose joints is crucial for ensuring the quality and reliability of these essential components in industrial fluid handling systems.
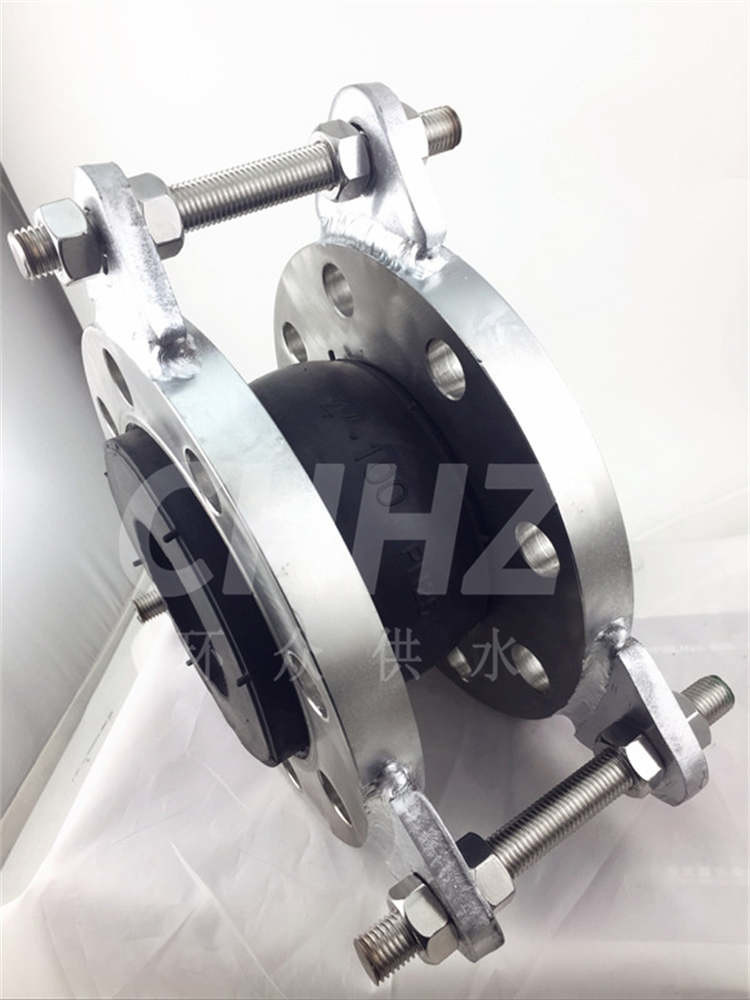