Metal Hoses Vs. Rubber Flexible Joints: A Comparative Analysis
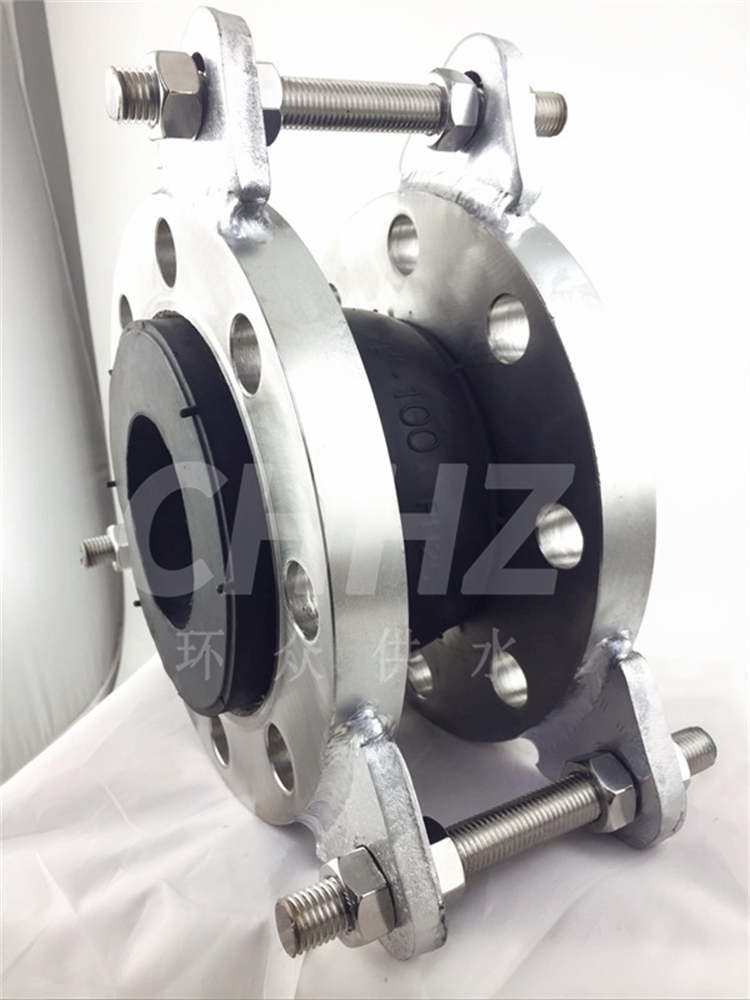
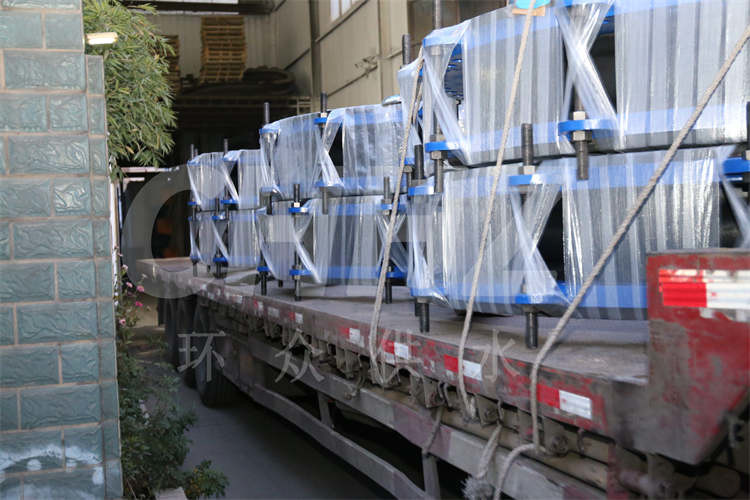
Introduction:The choice between metal hoses and rubber flexible joints is a critical decision in various industrial and construction applications. Both these components offer distinct advantages and have specific areas where they excel. This article aims to provide a comparative analysis of metal hoses and rubber flexible joints to help in understanding their relative strengths and optimal applications.
Metal Hoses:Metal hoses are constructed from resilient metal alloys such as stainless steel, providing exceptional strength and high-temperature resistance. They are widely favored in applications requiring robustness and durability, particularly in conveying high-temperature fluids, gases, and corrosive substances. Metal hoses offer superior pressure resistance and are suitable for applications where high mechanical strength is paramount. In industrial settings, metal hoses are often used in high-pressure hydraulic systems, chemical processing plants, and petrochemical installations.
Rubber Flexible Joints:On the other hand, rubber flexible joints are characterized by their flexibility, vibration absorption, and ability to accommodate movement. These components are constructed from high-grade synthetic elastomers and are particularly effective in minimizing vibrations, noise, and shock transmission in piping systems. Rubber flexible joints excel in applications that involve movement due to factors such as thermal expansion, contraction, or seismic activity. They find wide usage in HVAC systems, piping networks, and architectural applications where the isolation of vibrations and movement is crucial for the integrity and functionality of the system.
Comparative Analysis:When comparing metal hoses and rubber flexible joints, the choice largely depends on the specific requirements of the application. Metal hoses are preferred for high-pressure and high-temperature applications where mechanical strength and corrosion resistance are critical. Their robust construction makes them suitable for conveying aggressive chemicals, steam, and abrasive materials, as well as for use in harsh environmental conditions.
On the other hand, rubber flexible joints are valuable in scenarios where movement absorption, vibration isolation, and noise reduction are paramount. Their flexibility allows for the accommodation of thermal expansion, contraction, and misalignment, making them ideal for use in HVAC systems, seismic isolation, and building cladding applications. Rubber flexible joints are also widely employed in industrial settings where the reduction of noise and vibration improves the working environment and protects sensitive equipment.
In conclusion, the choice between metal hoses and rubber flexible joints depends on the specific requirements of the application, including factors such as pressure, temperature, movement, and environmental conditions. Each component offers unique advantages, and understanding their characteristics is essential for selecting the most suitable solution. While metal hoses excel in high-pressure and high-temperature applications, rubber flexible joints are preferred for their flexibility, movement absorption, and vibration isolation properties. By carefully evaluating the specific needs of the application, engineers and designers can make informed decisions to ensure optimal performance and longevity of the system.
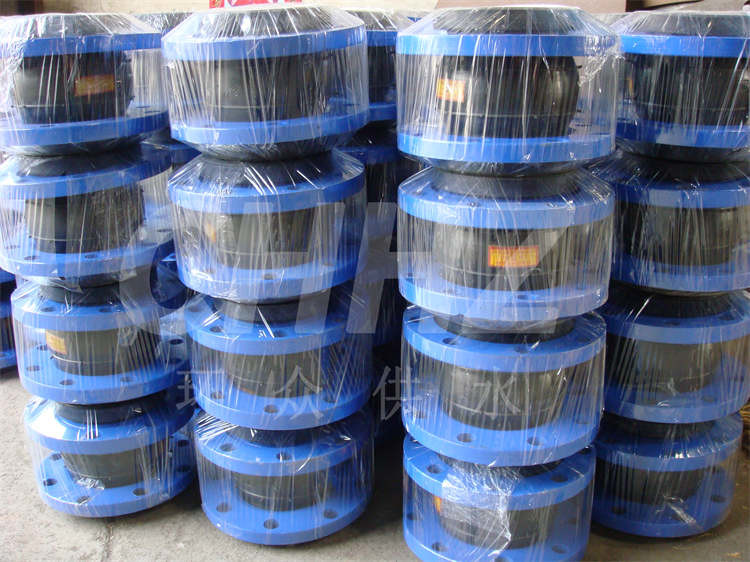