Plastic Couplings on Rubber Hoses: Manufacturing Process
Plastic couplings on rubber hoses play a crucial role in numerous applications across various industries, providing a reliable and efficient means of connecting hoses to other components or equipment. The manufacturing process of these plastic couplings involves several essential steps to ensure the production of high-quality, functional, and durable connections. In this article, we will explore the key aspects of the manufacturing process for plastic couplings on rubber hoses, shedding light on the techniques and considerations involved in their production.
Material Selection:The manufacturing process begins with the careful selection of suitable materials for the plastic couplings. High-quality thermoplastics such as polypropylene, polyethylene, PVC, or nylon are commonly used due to their favorable properties, including durability, chemical resistance, and ease of molding. The material selection process considers the specific application requirements, environmental factors, and compatibility with the rubber hose material to ensure optimal performance and longevity of the coupling.Injection Molding:Injection molding is a widely employed process for the production of plastic couplings. It involves the use of specialized machinery to heat the selected thermoplastic material to its melting point and then inject it into a precision-designed mold cavity. The mold is carefully crafted to form the desired shape and dimensions of the coupling, including features such as barbs, threads, or attachment mechanisms. The injection molding process allows for high-volume production and ensures consistent quality and precision in the manufactured couplings.
Mold Design and Tooling:The design of the mold and tooling is a critical aspect of the manufacturing process. The mold must be engineered to produce couplings with accurate dimensions, smooth surfaces, and structural integrity. Considerations such as the flow of molten plastic, cooling rates, and part ejection are meticulously incorporated into the mold design to achieve optimal production efficiency and part quality. Additionally, the tooling for the mold, including inserts, ejector pins, and gating systems, is carefully configured to ensure reliable and efficient molding operations.
Assembly and Integration:Once the plastic couplings are molded, they undergo assembly and integration processes to facilitate their connection to rubber hoses. This may involve incorporating features such as barbed ends, threaded connectors, or specialized seals to ensure secure and leak-free connections. The manufacturing process also includes quality checks and inspections to verify the dimensional accuracy, functional performance, and integrity of the assembled couplings.
Testing and Quality Assurance:Quality control measures are integral to the manufacturing process of plastic couplings on rubber hoses. Stringent testing protocols are implemented to evaluate aspects such as tensile strength, chemical resistance, and dimensional accuracy of the couplings. This may involve conducting pressure tests, leak tests, and environmental exposure assessments to ascertain the reliability and durability of the manufactured couplings under varying operational conditions.
In conclusion, the manufacturing process of plastic couplings on rubber hoses involves material selection, injection molding, mold design and tooling, assembly and integration, as well as testing and quality assurance measures. By meticulous attention to these steps, manufacturers ensure the production of robust and dependable couplings that meet the diverse needs of industries ranging from agriculture and automotive to construction and manufacturing.
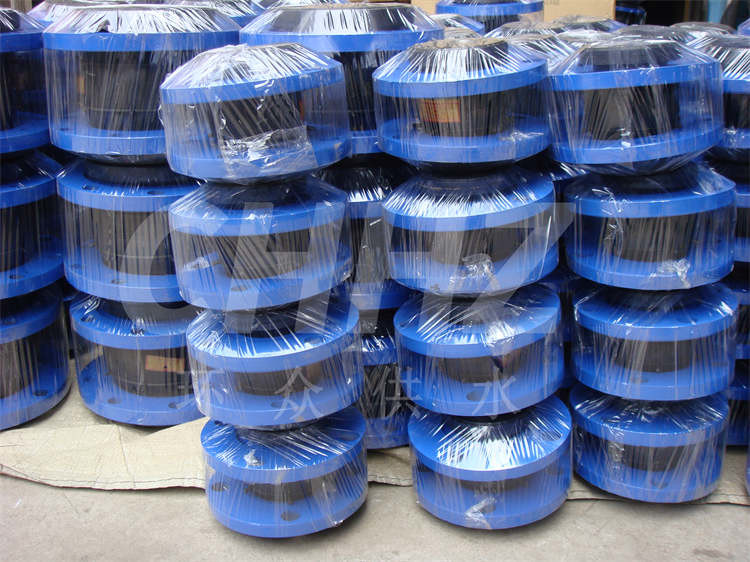