Fabrication of High-Voltage Rubber Cable Splice
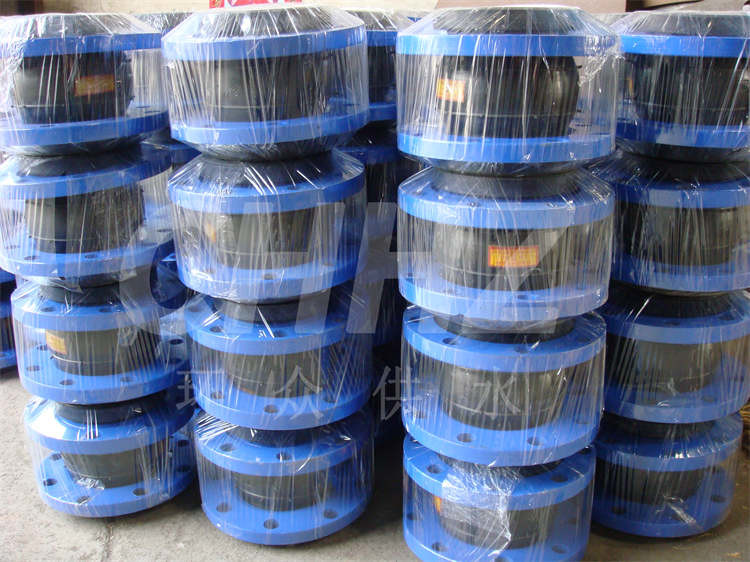
Splicing high-voltage rubber cables is a critical process that necessitates meticulous attention to detail and adherence to industry standards to ensure the safety and reliability of electrical systems. This article provides an overview of the fabrication process for a splice in high-voltage rubber cables, outlining the key steps and considerations involved in achieving a robust and durable joint for transmitting electrical power in demanding applications.
Material Preparation: The first step in fabricating a high-voltage rubber cable splice involves preparing the cable ends for termination. This includes carefully stripping the rubber insulation back to expose the conductor cores and ensuring that the exposed metal cores are clean and free from any contaminants such as dirt, grease, or corrosion. Additionally, the cable insulation must be examined for any signs of damage or degradation that could compromise the electrical integrity of the splice.
Connection and Termination: Once the cable ends are properly prepared, the conductor cores are securely connected and terminated using specialized cable lugs or connectors designed for high-voltage applications. The cable lugs are crimped or mechanically secured onto the conductor cores to establish a robust and low-resistance electrical connection. Careful attention must be paid to the crimping process to ensure that the lug is uniformly and securely attached to the conductor, minimizing the risk of excessive resistance or heat generation at the connection point.
Insulation and Sealing: After the conductor connection is established, insulating and sealing materials are applied to protect the splice from environmental influences, mechanical stress, and moisture ingress. In the case of high-voltage rubber cables, this often involves using specially formulated insulating tapes and heat-shrink tubing that provide electrical insulation and mechanical protection while maintaining flexibility and resistance to harsh operating conditions. The sealing process is crucial to safeguard the cable splice against moisture infiltration and maintain the dielectric strength of the insulation.
Testing and Quality Assurance: Following the completion of the fabrication process, the cable splice undergoes rigorous testing and inspection to verify its electrical integrity and mechanical durability. This includes conducting insulation resistance tests, high-potential (hi-pot) tests, and continuity checks to ensure that the splice meets the specified performance criteria and complies with industry standards for high-voltage cable terminations. Additionally, visual examinations and dimensional measurements are performed to confirm the absence of defects and to validate the adherence to installation requirements.
Compliance with Standards: Fabrication of high-voltage rubber cable splices must be carried out in strict conformity with established industry standards and regulations, such as those outlined by organizations like IEEE (Institute of Electrical and Electronics Engineers) and IEC (International Electrotechnical Commission). Adherence to these standards is essential to guarantee the safety, reliability, and long-term performance of the spliced cable in high-voltage power transmission and distribution systems.
In summary, the fabrication of a high-voltage rubber cable splice demands precision, expertise, and strict adherence to quality control measures to ensure the integrity of electrical connections and insulation. The meticulous attention to material preparation, connection, insulation, testing, and compliance with standards is indispensable in achieving a durable and reliable splice capable of withstanding the demands of high-voltage applications.
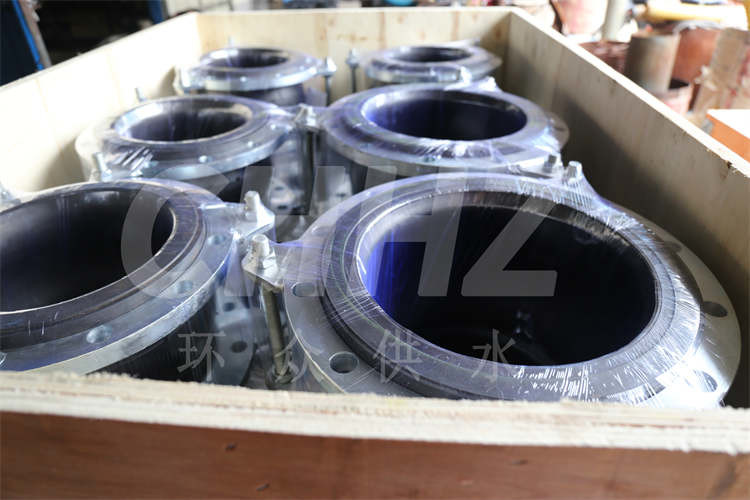