Integration of Rubber Expansion Joints and Gate Valves
In industrial applications, the seamless integration of rubber expansion joints with gate valves is crucial to ensure efficient and reliable performance in fluid conveyance systems. This article outlines the essential steps and considerations for effectively interfacing rubber expansion joints with gate valves, highlighting the key aspects of the integration process to optimize fluid flow, minimize vibrations, and enhance system longevity.
Alignment and Positioning: The first step in the integration of rubber expansion joints with gate valves involves carefully aligning and positioning the components to facilitate a smooth and unobstructed flow path. Proper alignment is critical to avoid undue mechanical stresses on both the expansion joint and the gate valve during operation, promoting optimal performance and longevity. Additionally, the positioning of the components must allow for adequate clearance and flexibility to accommodate thermal movements, vibrations, and dynamic loads within the system.
Flange Connection and Sealing: Once aligned, the rubber expansion joint and gate valve are connected via flange joints to establish a secure and leak-free interface. Precision in aligning the flange bolt holes is essential to ensure a uniform and consistent distribution of loads across the joint, minimizing the potential for stress concentrations and sealing surface irregularities. Proper bolt tightening procedures, utilizing specified torque values and sequence, are employed to achieve adequate compression of gaskets and a reliable, leak-tight seal between the expansion joint and the gate valve.
Flexibility and Movement: Rubber expansion joints are designed to accommodate thermal expansion, vibration, and misalignment, thereby safeguarding the integrity of the overall piping system. When integrated with gate valves, the expansion joint should be installed to allow for unrestricted axial, lateral, and angular movement, enabling it to effectively absorb movements and vibrations induced by the fluid flow or operational dynamics of the system. This flexibility helps to minimize stress on the components and extends the service life of the piping system.
Thermal and Chemical Compatibility: Consideration of thermal and chemical compatibility between the rubber expansion joint and gate valve materials is paramount in ensuring long-term performance and resilience. The expansion joint's elastomeric material should be compatible with the operational temperature range and fluid composition, resisting degradation, swelling, or embrittlement that could compromise its functionality over time. Compatibility assessments should also account for any potential exposure to aggressive chemicals or environmental conditions that may impact the joint's integrity and service life.
Operational Testing and Quality Assurance: Following the integration of the rubber expansion joint with the gate valve, thorough operational testing and quality assurance measures are undertaken to validate the functionality and performance of the assembled interface. This includes conducting pressure tests, leak detection assessments, and visual inspections to verify the integrity of the connection, the effectiveness of sealing, and the absence of defects or irregularities that could compromise operational reliability.
Compliance with Standards and Best Practices: The integration process must adhere to relevant industry standards, manufacturer recommendations, and best practices to ensure that the combined use of rubber expansion joints and gate valves meets the technical, safety, and performance requirements of the application. Adhering to recognized standards, such as those specified by organizations like the American Society of Mechanical Engineers (ASME) and the Fluid Sealing Association (FSA), ensures that the integration process follows established guidelines and practices for optimal system performance.
In conclusion, the effective integration of rubber expansion joints with gate valves demands meticulous attention to alignment, sealing, flexibility, material compatibility, testing, and compliance with standards to create a robust and durable interface in fluid conveyance systems. By following established procedures and best practices, the integration process can optimize fluid flow, mitigate operational stresses, and enhance the reliability and longevity of the interconnected components.
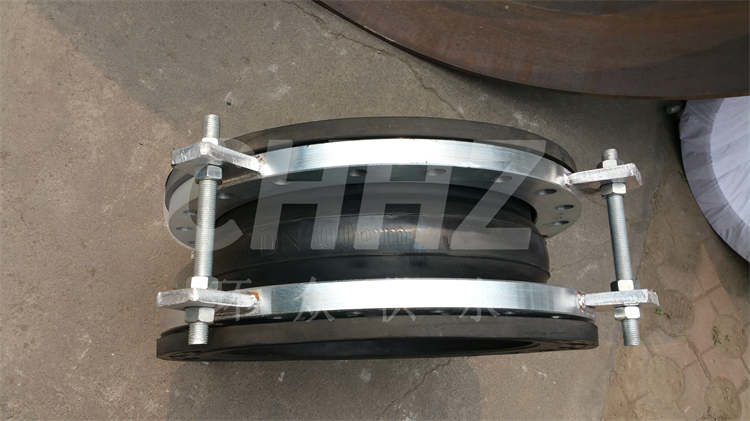