Rubber Flexible Joint Materials
Rubber flexible joints are essential components in piping systems, providing vibration absorption, noise reduction, and compensation for thermal expansion and contraction. The choice of materials for rubber flexible joints is crucial to ensure durability, flexibility, and resistance to various environmental conditions. Several key materials commonly used in the manufacturing of rubber flexible joints include:
1. Natural Rubber (NR): Natural rubber, derived from the latex of rubber trees, offers excellent resilience, abrasion resistance, and flexibility. It is well-suited for applications where exposure to organic solvents and moderate temperatures is anticipated. Additionally, natural rubber exhibits good tensile strength, tear resistance, and compression set properties, making it a popular choice for rubber flexible joints.
2. Styrene-Butadiene Rubber (SBR): SBR is a synthetic rubber compound characterized by its excellent impact strength, abrasion resistance, and resilience. It is often used in rubber flexible joints where resistance to water, heat, and oxidation is required. SBR is known for its versatility and cost-effectiveness, making it a common choice for various piping applications.
3. Neoprene (CR): Neoprene is a synthetic rubber material renowned for its exceptional resistance to oils, chemicals, and extreme temperatures. It is widely utilized in rubber flexible joints exposed to harsh industrial environments, such as petrochemical plants and refineries. Neoprene's inherent stability and durability make it well-suited for demanding applications where resistance to environmental factors is paramount.
4. EPDM (Ethylene Propylene Diene Monomer): EPDM is a synthetic elastomer known for its outstanding resistance to weathering, ozone, and UV exposure. EPDM rubber flexible joints are ideal for outdoor and exposed applications, as they maintain their properties under prolonged exposure to sunlight and environmental elements. EPDM's resistance to heat, water, and steam further enhances its suitability for diverse piping systems.
5. Nitrile Rubber (NBR): Nitrile rubber, also known as Buna-N, is valued for its exceptional oil resistance, making it a preferred material for rubber flexible joints in applications involving petroleum-based fluids, fuels, and hydraulic oils. NBR also exhibits excellent tensile strength and tear resistance, making it suitable for demanding industrial environments.
6. Fluoroelastomers (FKM): Fluoroelastomers, including Viton®, are highly resistant to chemicals, fuels, and elevated temperatures, making them suitable for extreme operating conditions. Rubber flexible joints utilizing FKM compounds are commonly employed in industrial applications where resistance to aggressive fluids and high temperatures is required.
In the selection of materials for rubber flexible joints, factors such as temperature range, chemical exposure, mechanical stresses, and application-specific requirements must be carefully considered to ensure optimal performance and longevity. Each material offers unique properties and advantages, allowing for the customization of rubber flexible joints to meet the demands of diverse piping systems. Proper material selection, accompanied by adherence to quality standards and installation guidelines, contributes to the reliability and effectiveness of rubber flexible joints in industrial and commercial applications.
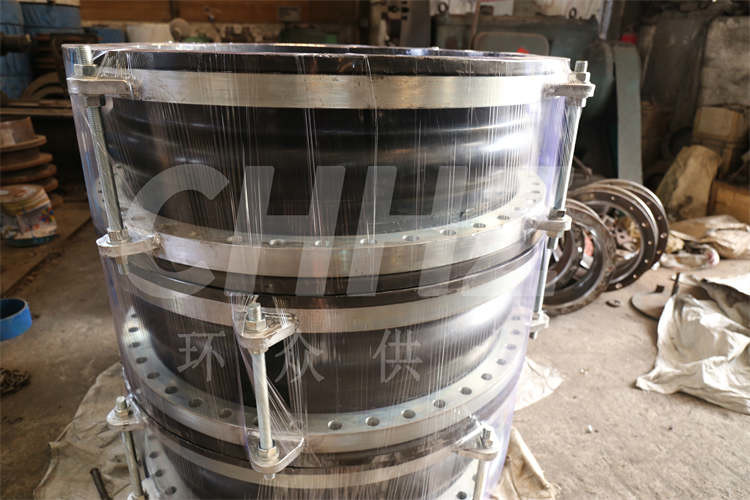