Flexibility and Corrosion Resistance of Rubber Flexible Joints
Rubber flexible joints play a critical role in piping systems, offering the necessary flexibility to absorb vibration and movement while withstanding the corrosive effects of various fluids and environmental conditions. The materials used to manufacture rubber flexible joints are selected for their ability to provide reliable performance in demanding applications requiring both flexibility and corrosion resistance.
1. EPDM (Ethylene Propylene Diene Monomer): EPDM rubber flexible joints are prized for their exceptional resistance to weathering, ozone, and UV exposure, making them well-suited for outdoor and exposed applications. EPDM's ability to maintain its properties under prolonged exposure to sunlight and environmental elements contributes to its effectiveness in corrosive environments. The flexibility and corrosion resistance of EPDM rubber flexible joints make them a preferred choice for applications where atmospheric exposure and resistance to water and steam are paramount.
2. Neoprene (CR): Neoprene is a synthetic rubber material known for its remarkable resistance to oils, chemicals, and extreme temperatures, making it an ideal choice for rubber flexible joints in harsh industrial environments. Neoprene's stability and durability enable it to withstand the corrosive effects of a wide range of chemicals, making it suitable for use in piping systems requiring flexibility and resistance to chemical corrosion.
3. Fluoroelastomers (FKM): Fluoroelastomers, such as Viton®, offer exceptional resistance to a broad spectrum of chemicals, fuels, and elevated temperatures. This makes them well-suited for applications requiring both flexibility and resistance to aggressive fluids and corrosive conditions. Rubber flexible joints utilizing FKM compounds are commonly employed in industrial settings where resistance to chemical corrosion and high temperatures is essential.
4. Nitrile Rubber (NBR): Nitrile rubber, or Buna-N, is valued for its excellent oil resistance, making it a preferred material for rubber flexible joints in applications involving petroleum-based fluids, fuels, and hydraulic oils. NBR's resistance to oil and its flexibility make it an ideal choice for piping systems that require protection against both mechanical stresses and potential corrosion from hydrocarbons.
The combination of flexibility and resistance to corrosion is crucial in the selection of rubber flexible joint materials. By effectively addressing the challenges posed by mechanical movement and exposure to corrosive fluids, these materials contribute to the reliability and longevity of piping systems in diverse industrial and commercial environments. Careful consideration of the specific operating conditions and fluid characteristics is essential to ensure that the chosen rubber flexible joint materials meet the requirements for both flexibility and corrosion resistance, consequently contributing to the overall effectiveness of the piping system.
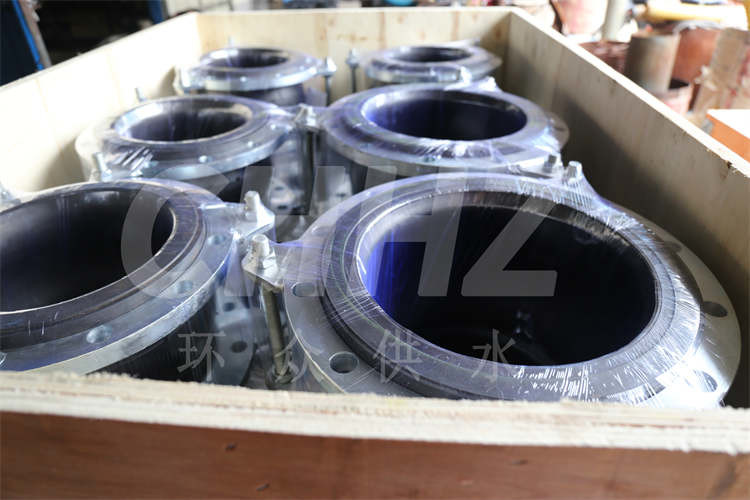