Rubber Reducing Joints: Ensuring Efficient Piping Systems
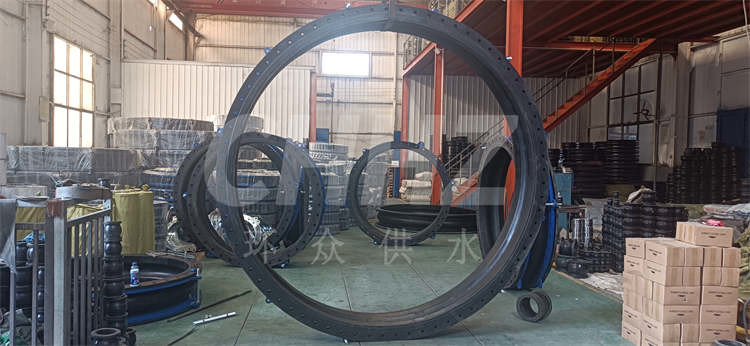
Rubber reducing joints are essential components in piping systems, designed to facilitate the seamless transition between pipes of different diameters while offering flexibility and resilience to various environmental and operational challenges. These joints' ability to accommodate the differential pressure and movement within the piping system makes them indispensable in a wide range of industrial, commercial, and residential applications.
1. Material Selection:Rubber reducing joints are commonly manufactured from high-quality elastomeric materials such as EPDM, neoprene, or nitrile rubber. These materials are chosen for their exceptional flexibility, durability, and resistance to corrosion, making them ideal for withstanding the demands of diverse operating conditions. EPDM rubber provides excellent resistance to weathering, ozone, and ultraviolet exposure, while neoprene exhibits remarkable chemical resistance and stability. Nitrile rubber, known for its outstanding oil resistance, is often used in applications involving petroleum-based fluids.
2. Flexibility and Absorption of Vibrations:The design and material composition of rubber reducing joints enable them to absorb vibrations, reduce noise, and compensate for thermal expansion and contraction, thereby ensuring the integrity of the entire piping system. Their flexibility allows for smooth and efficient flow transition between pipes of varying diameters, minimizing pressure drops and turbulence within the system.
3. Corrosion Resistance: Rubber reducing joints demonstrate resilience against the corrosive effects of chemicals, oils, and environmental factors, contributing to the longevity and reliability of piping systems. The selected elastomeric materials' inherent resistance to corrosion ensures that the joints maintain their structural integrity, even in challenging industrial environments.
4. Installation and Maintenance:The installation of rubber reducing joints is relatively straightforward, and their flexibility allows for easy alignment and connection with pipes of different sizes. Periodic inspection and maintenance are essential to ensure optimal performance and longevity. Visual checks for wear, tear, or degradation of the rubber material, along with regular cleaning and lubrication of the joints, contribute to their prolonged service life.
5. Application Versatility: Rubber reducing joints find applications in various industries, including water treatment plants, chemical processing facilities, HVAC systems, and plumbing installations. Their ability to accommodate different pipe sizes and effectively mitigate the impact of fluid flow and system vibrations makes them indispensable in achieving efficient and reliable piping systems.
In conclusion, rubber reducing joints play a vital role in maintaining the functionality and integrity of piping systems by seamlessly transitioning between pipes of varying diameters. Their inherent flexibility, resistance to corrosion, and ability to absorb vibrations make them essential components for ensuring the efficient operation of diverse industrial and commercial applications. The effective selection, installation, and maintenance of rubber reducing joints are paramount in safeguarding the performance and longevity of piping systems, thereby contributing to operational efficiency and overall system reliability.
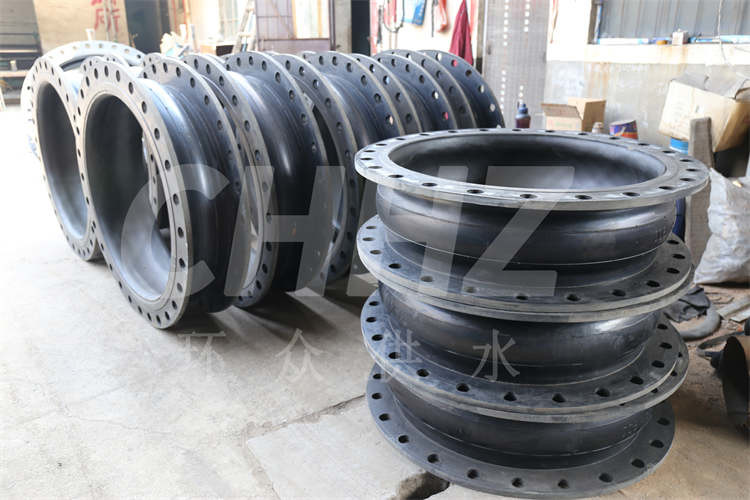