Rubber Joint Execution Standard Specification: Understanding the Standards
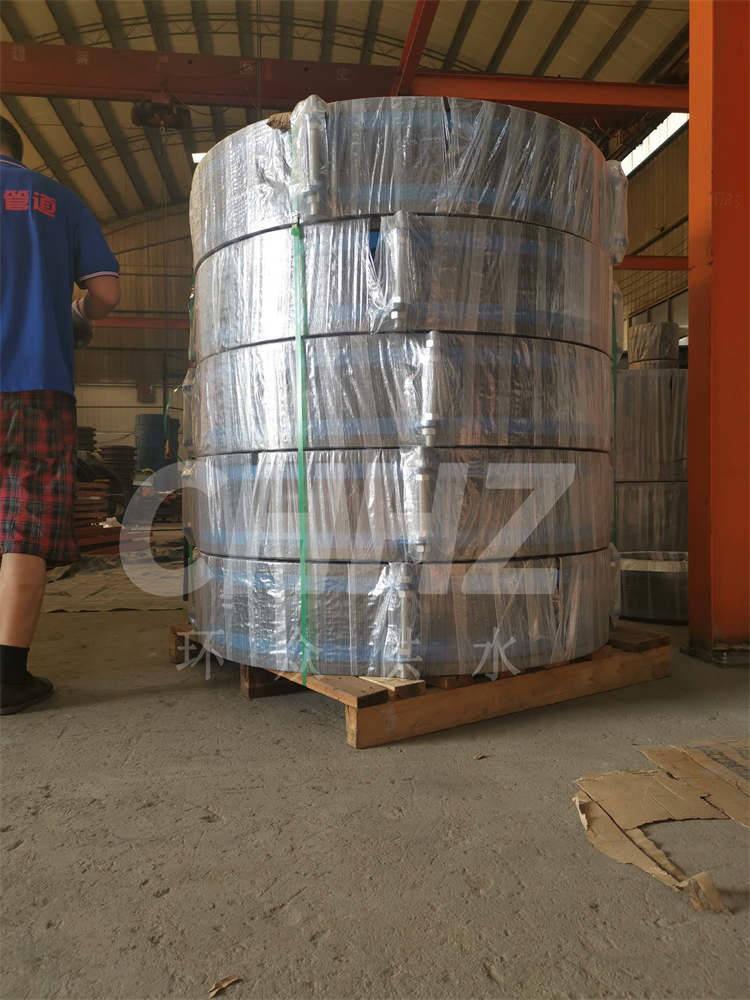
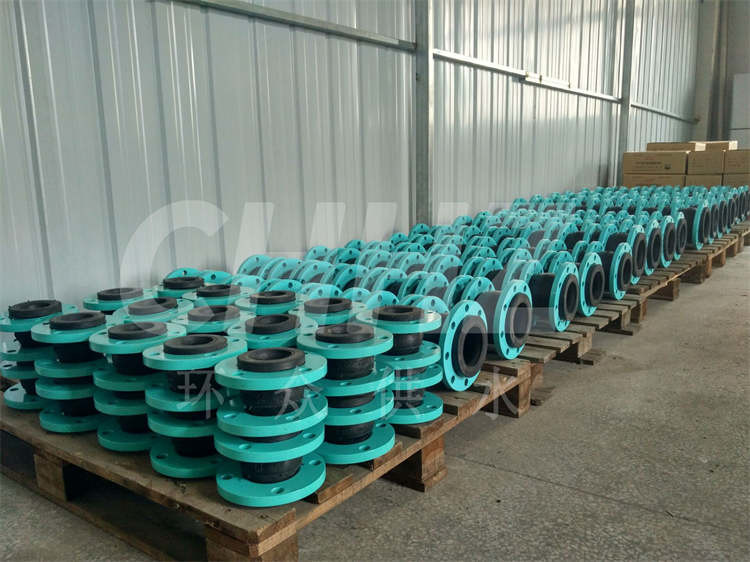
The execution of rubber joints is governed by standardized specifications to ensure their quality, integrity, and performance across various applications. This article provides an insight into the execution standard specifications for rubber joints, outlining the key guidelines, testing procedures, and parameters that govern their production and installation.
Rubber joints are subject to standard specifications that define their characteristics, materials, manufacturing processes, and performance requirements. These specifications are developed and regulated by industry organizations, such as the ASTM International, ISO (International Organization for Standardization), and national standards bodies, to ensure consistency, quality, and reliability in the design, production, and utilization of rubber joints.
The execution standards for rubber joints encompass a range of parameters, starting with the material selection and composition of the rubber components. The standards specify the types of rubber materials suitable for various applications, such as natural rubber, nitrile rubber (NBR), ethylene propylene diene monomer (EPDM) rubber, and fluorocarbon rubber (FKM). Additionally, the standards mandate specific material properties, such as hardness, tensile strength, elongation, and resistance to environmental factors, to ensure the durability and performance of the rubber joints.
The manufacturing processes and construction of rubber joints are also defined within the execution standards. These specifications include guidelines for the molding or fabrication methods, reinforcement techniques, and the incorporation of additives or fillers to modify the material properties as required for specific applications. Furthermore, the standards outline the dimensional tolerances, surface finishes, and quality control measures to uphold the integrity and consistency of rubber joint production.
Testing and performance criteria are integral components of rubber joint execution standards, encompassing mechanical, chemical, and environmental tests aimed at evaluating the performance and durability of the joints. Mechanical tests such as pressure and deflection testing assess the structural integrity and load-bearing capabilities of the rubber joints. Chemical resistance tests evaluate the compatibility of the rubber materials with various fluids, including oils, fuels, chemicals, and solvents. Environmental tests, including temperature cycling, ozone resistance, and aging tests, simulate real-world conditions to ascertain the long-term performance and reliability of the rubber joints.
The installation and maintenance requirements for rubber joints are also covered within the execution standards. Guidelines for proper storage, handling, and installation procedures, as well as best practices for inspection, maintenance, and replacement intervals, are provided to ensure the optimal performance and service life of the rubber joints in their intended applications.
In conclusion, the execution standard specifications for rubber joints serve as essential guidelines for the design, production, and installation of these critical components. By adhering to standardized specifications, manufacturers, suppliers, and end-users can ensure the quality, reliability, and performance of rubber joints across diverse industrial applications. As technology and industry requirements evolve, the continuous refinement and development of execution standard specifications will further enhance the quality and effectiveness of rubber joints, contributing to their continued significance in modern engineering and industrial practices.
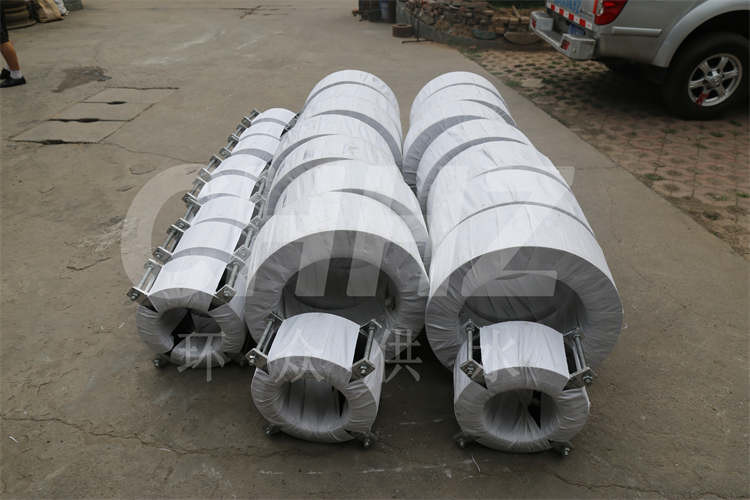