The Use of Butyl Rubber Joints in Engineering Applications
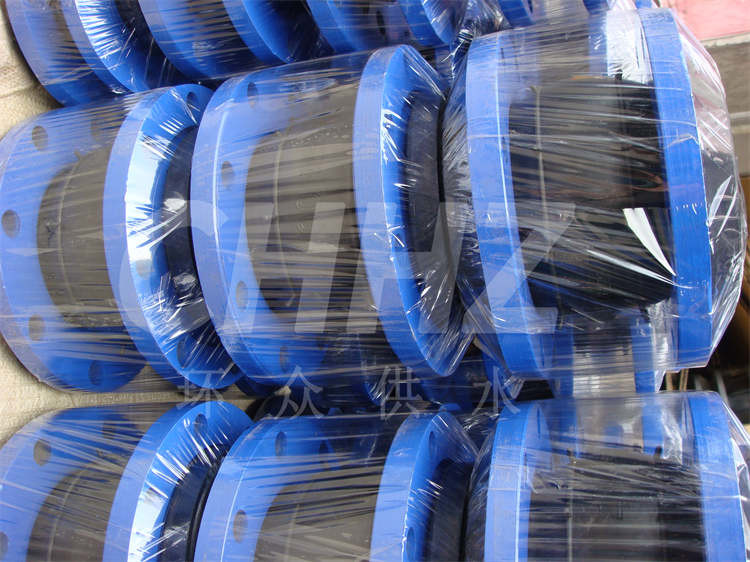
Butyl rubber joints, also known as butyl rubber expansion joints, are widely utilized in various engineering applications to accommodate movement, absorb vibration, and provide flexibility in piping systems, bridges, and other structures. This article sheds light on the distinctive properties, applications, and benefits of butyl rubber joints in the field of engineering.
Butyl rubber, a copolymer of isobutylene and a small amount of isoprene, exhibits exceptional impermeability to gases, excellent resistance to weathering, and high flexibility, making it an ideal material for expansion joints. The unique molecular structure of butyl rubber imparts it with low gas and moisture permeability, which is crucial for applications where sealing and protection against environmental factors are paramount.
One of the key applications of butyl rubber joints is in piping systems, where they are employed to absorb thermal expansion, system vibration, and movement caused by ground settlement. These joints play a critical role in maintaining the integrity of pipelines, preventing leaks, and ensuring the efficient operation of industrial, municipal, and commercial fluid transport systems. Moreover, butyl rubber joints find extensive use in building construction, particularly in bridges, parking garages, and infrastructure projects, where they facilitate the movement of structures due to thermal expansion, seismic activity, or other dynamic forces.
The benefits of butyl rubber joints are further underscored by their excellent resistance to ozone, UV radiation, and chemical exposure, making them suitable for outdoor and industrial environments. This resistance contributes to their longevity and reliability in challenging conditions, reducing maintenance requirements and operational downtime in various applications.
Another notable advantage of butyl rubber joints is their ease of installation and customization to specific project requirements. Their flexibility and adaptability allow for efficient integration into diverse engineering systems, minimizing the need for complex and costly modifications during installation.
In summary, butyl rubber joints play a pivotal role in ensuring the integrity, functionality, and longevity of engineering systems and structures. Their unique blend of properties, including impermeability, flexibility, and resistance to environmental factors, makes them indispensable components in the construction and maintenance of pipelines, bridges, and other infrastructure. As industries continue to evolve, the versatile and dependable nature of butyl rubber joints positions them as essential elements in engineering and construction, providing solutions to challenges associated with movement, vibration, and environmental exposure.
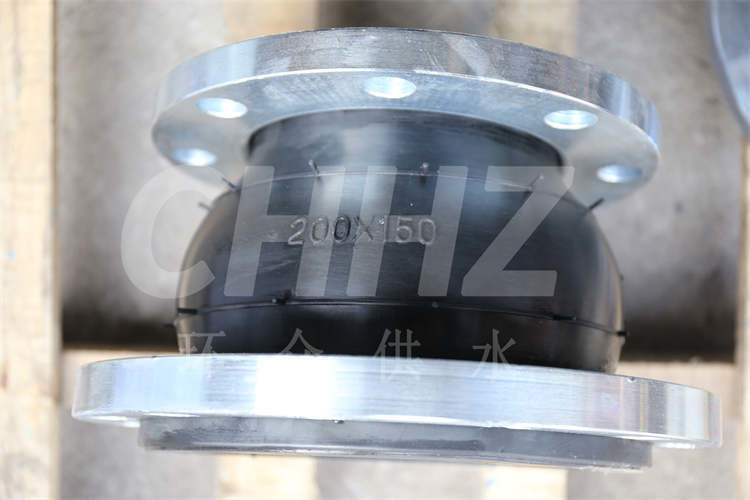