Welding Process for Rubber Joints
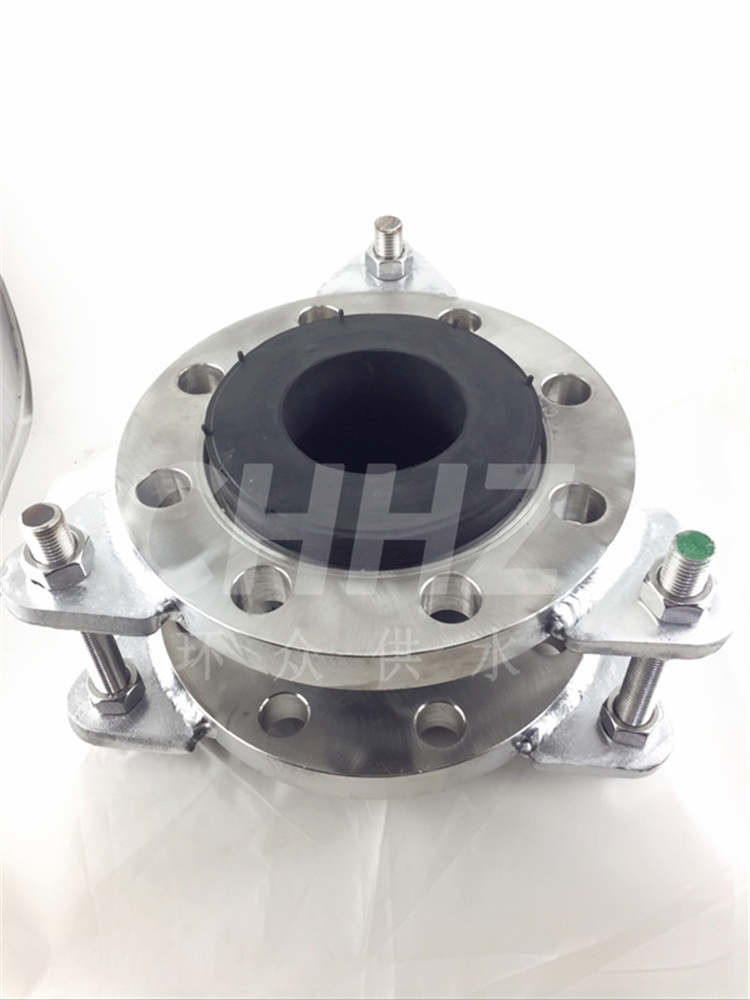
Rubber joints are an essential component in pipeline systems, offering flexibility and vibration absorption. When welding rubber joints to piping, a meticulous process is required to ensure a strong and durable connection. This article outlines the welding process for rubber joints, providing insights into the necessary steps and considerations for achieving optimal results.
1. Inspection and Preparation:Before commencing the welding process, it is crucial to inspect the rubber joint and the piping system. Verify that the rubber joint is free from any defects, such as cuts, abrasions, or contaminants, which could compromise the welding quality. Additionally, ensure the pipe ends are clean, smooth, and free from any protrusions or irregularities that could hinder a proper fit with the rubber joint.
2. Surface Treatment:To facilitate proper adhesion between the rubber joint and the pipe, the surface of the pipe end should be treated appropriately. This may involve degreasing, abrading, or roughening the pipe surface to enhance the bonding capability of the joint adhesive.
3. Application of Adhesive:A specialized adhesive, compatible with both the rubber material of the joint and the surface of the pipe, is applied to create a strong bond. Care must be taken to apply the adhesive evenly and avoid excess buildup, which could lead to an uneven connection or weak spots in the joint.
4. Alignment and Fitting:The rubber joint is carefully aligned with the pipe end to ensure a proper fit. It is crucial to maintain the alignment throughout the fitting process to prevent misalignment or twisting, which could result in a faulty joint.
5. Curing Process:Once the rubber joint is fitted onto the pipe, the curing process begins. This process may involve the application of heat, pressure, or a combination of both to facilitate proper adhesion and curing of the adhesive. The duration and conditions of the curing process will depend on the specific adhesive used and the manufacturer's recommendations.
6. Quality Assurance and Testing:After the curing process is complete, quality assurance measures are taken to ensure the integrity of the joint. This may involve non-destructive testing to check for any defects, leaks, or weaknesses in the joint. Pressure testing, visual inspection, and other quality control measures may be employed to verify the quality of the welded joint.
In conclusion, the welding process for rubber joints demands precision, expertise, and adherence to best practices to achieve a reliable and durable connection. By following the outlined steps and paying close attention to the details, engineers and technicians can ensure that the welded rubber joints meet the stringent quality standards required for safe and efficient operation in pipeline systems.
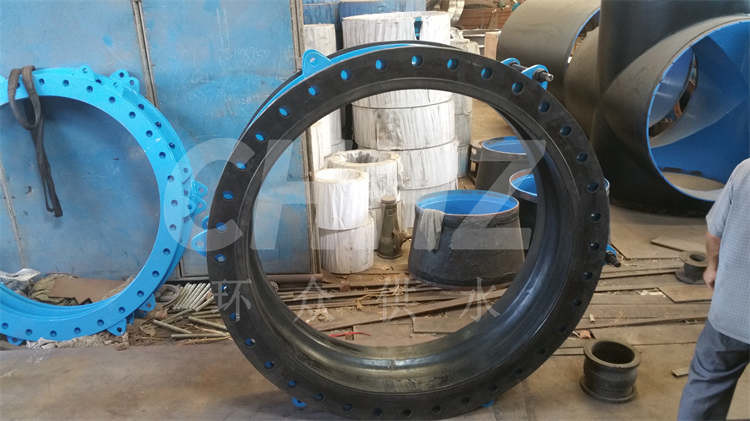