Flexible Rubber Expansion Joint Material
Flexible rubber expansion joints are critical components in various piping and ducting systems, providing vital functions such as absorbing thermal expansion, reducing vibration, and compensating for misalignment. The choice of material for these expansion joints plays a significant role in determining their performance, durability, and compatibility with specific applications. This article aims to delve into the different materials used for flexible rubber expansion joints and their respective characteristics, highlighting the importance of material selection in ensuring optimal joint functionality.
Natural Rubber (NR): Natural rubber, derived from the latex of rubber trees, offers excellent flexibility, resilience, and tear resistance, making it a popular choice for flexible expansion joints. Its elasticity allows for effective movement absorption and vibration isolation, while its durability ensures prolonged service life. However, natural rubber may not be suitable for applications involving exposure to oils, solvents, or high temperatures, as it can degrade under such conditions.
Neoprene (CR): Neoprene, a synthetic rubber, is valued for its resistance to weathering, ozone, and a wide range of chemicals, making it suitable for outdoor and industrial applications. It exhibits good physical properties over a broad temperature range, ensuring stability and performance in various environmental conditions. Neoprene expansion joints are often used in applications where resistance to oil and fuels is necessary, such as in fuel delivery systems and petroleum processing.
EPDM (Ethylene Propylene Diene Monomer): EPDM rubber offers exceptional resistance to weathering, heat, ozone, and aging, making it a versatile material for flexible expansion joints. Its suitability for outdoor use and exposure to extreme temperatures, water, and steam makes it a preferred choice for HVAC, water supply, and automotive applications. EPDM expansion joints provide reliable sealing and flexibility in demanding environments, contributing to their widespread use in diverse industries.
Fluoroelastomers (FKM): Fluoroelastomers, such as Viton®, are known for their superior chemical resistance, particularly to fuels, oils, and harsh chemicals, making them ideal for challenging applications in the chemical processing, aerospace, and automotive industries. The high temperature resistance and thermal stability of FKM rubber expansion joints ensure long-term performance in aggressive environments where conventional elastomers may falter.
Selecting the Right Material: The selection of flexible rubber expansion joint material should be guided by an understanding of the application's operating conditions, including temperature, exposure to chemicals, pressure variations, and environmental factors. Factors such as compatibility with the conveyed media, resistance to corrosion, and longevity should be carefully evaluated when choosing the material for expansion joints to ensure optimal performance and service life.
In conclusion, the material used in flexible rubber expansion joints significantly influences their functionality, durability, and suitability for specific applications. By considering the unique properties and performance characteristics of natural rubber, neoprene, EPDM, and fluoroelastomers, engineers and system designers can make informed decisions when selecting the appropriate material for expansion joints, thereby ensuring the reliability and effectiveness of piping and ducting systems.
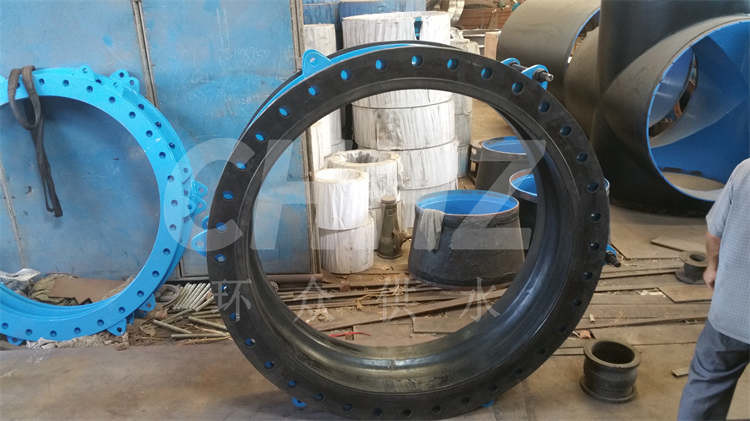