Welding Rubber Joints: A Comprehensive Guide to Proper Techniques
Welding rubber joints, also known as rubber bellows, is a critical skill required in various industrial applications such as piping systems, machinery, and automotive components. Proper welding procedures ensure the structural integrity and performance of rubber joints. This comprehensive guide outlines the essential techniques for welding rubber joints.
Preparation:Before initiating the welding process, it's crucial to prepare both the rubber joint and the mating surfaces for optimal results. The following steps are generally involved in the preparation phase:1. Surface Cleaning: Thoroughly clean the surfaces of the rubber joint and the adjoining components to remove any contaminants, grease, or debris. This can be achieved using appropriate cleaning agents and methods suitable for the specific materials involved.2. Alignment: Ensure that the rubber joint and the mating surfaces are properly aligned to guarantee a seamless welding process and optimal structural integrity.
Welding Techniques:Welding rubber joints requires specialized techniques to effectively bond the materials without compromising the rubber's properties. Here are the primary welding techniques commonly used for rubber joints:1. Heat Sealing: Heat sealing, also known as vulcanization, is a widely used technique for welding rubber joints. This method involves the application of heat and pressure to fuse the rubber surfaces together, creating a durable and flexible bond. Vulcanizing equipment, such as hot presses or autoclaves, is utilized to achieve the necessary temperature and pressure for the welding process.2. Adhesive Bonding: Adhesive bonding involves using suitable adhesives to bond the rubber joint to the mating surfaces. It's essential to select adhesives specifically designed for rubber-to-metal or rubber-to-rubber bonding, ensuring strong adhesion and resistance to environmental factors.3. Mechanical Fastening: In some cases, mechanical fastening techniques, such as clamping or fastener insertion, are utilized to secure the rubber joint to the adjacent components. This approach provides a reliable connection while allowing for disassembly and reassembly if necessary.
Post-Welding Inspection:After the welding process is completed, a thorough inspection is essential to verify the integrity and quality of the welded rubber joint. The following steps are typically incorporated into the inspection phase:1. Visual Examination: Conduct a visual inspection of the welded area to identify any signs of irregularities, such as incomplete bonding, voids, or surface damage.2. Dimensional Verification: Verify the dimensional accuracy of the welded joint to ensure that it conforms to the specified requirements and tolerances.3. Leakage Testing: Perform a leakage test, if applicable, to confirm that the welded joint maintains its integrity under pressure and environmental conditions.
By employing the correct welding techniques and adhering to meticulous preparation and inspection procedures, engineers and technicians can achieve strong, reliable, and durable welded rubber joints. This guide underscores the importance of precision and expertise in welding rubber joints to ensure the safety and performance of industrial applications across various sectors.
In summary, mastering the welding techniques for rubber joints is crucial to maintaining the functionality and longevity of machinery, piping systems, and other components. Adhering to proper welding practices outlined in this guide can contribute to the overall efficiency and safety of industrial operations.
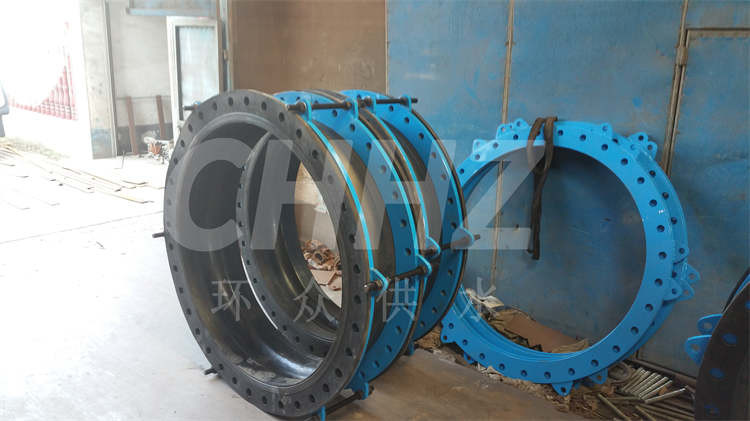