Rubber Joint Assembly and Installation – Ensuring Performance and Reliability
The assembly of rubber joints is a critical process that directly impacts the performance and longevity of piping systems across various industrial applications. Proper assembly and installation are essential to ensure the effectiveness of rubber joints in accommodating movement, absorbing vibrations, and maintaining leak-free connections. This article delves into the key considerations and best practices for the assembly and installation of rubber joints, highlighting the significance of these processes in achieving optimal performance and reliability.
The assembly of rubber joints begins with the selection of high-quality components, including the rubber body, flanges, reinforcing materials, and sealing elements. Manufacturers must adhere to strict quality control and inspection procedures to ensure that each component meets the required specifications and standards. Proper material selection and compatibility are crucial to prevent chemical degradation, premature wear, and potential failure of the rubber joint assembly.
During the assembly process, attention must be given to the alignment and positioning of the rubber joint components. Accurate alignment of the mating flanges and proper insertion of the rubber element are essential to prevent misalignment, undue stress, and uneven loading on the joint during operation. Additionally, the correct torque specifications for tightening bolts and nuts should be followed to achieve the proper compression of the rubber element and ensure a secure, leak-free joint.
Furthermore, the installation of rubber joints involves the careful consideration of environmental and operational factors. Factors such as temperature variations, pressure fluctuations, and mechanical movements must be accounted for to determine the appropriate type of rubber joint and installation method. It's vital to follow manufacturer recommendations and industry guidelines to accommodate thermal expansion, contraction, and angular deflection to prevent premature failure and maintain system integrity.
Proper sealing and gasket placement are also critical aspects of rubber joint assembly. The use of compatible and durable sealing materials, correctly positioned within the joint assembly, is essential to ensure effective fluid containment, prevent leakage, and provide a reliable barrier against external contaminants.
In conclusion, the assembly and installation of rubber joints are crucial stages that directly influence the performance, longevity, and safety of piping systems. Adherence to best practices, proper material selection, meticulous attention to detail, and compliance with industry standards are essential for ensuring the effectiveness and reliability of rubber joint assemblies. By prioritizing these factors, engineers, installers, and maintenance personnel can contribute to the optimal performance and service life of rubber joints in diverse industrial applications.
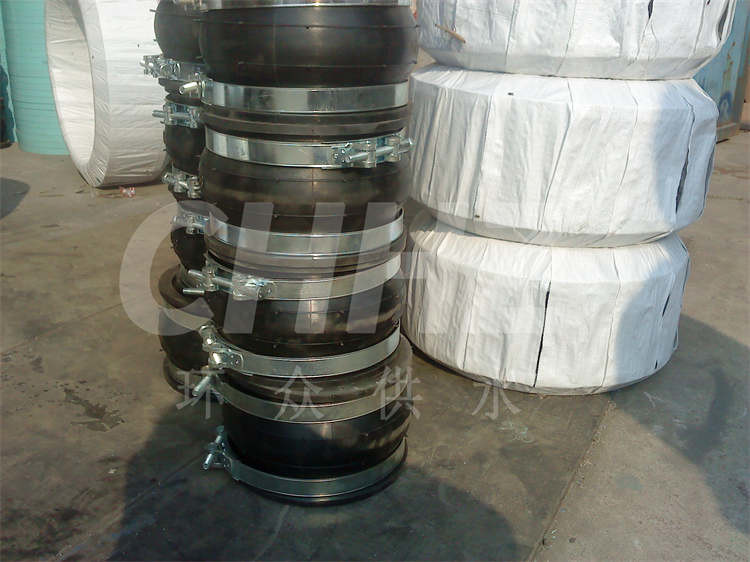