Rubber Joints in Chemical Engineering — Ensuring Safety and Efficiency in Piping Systems
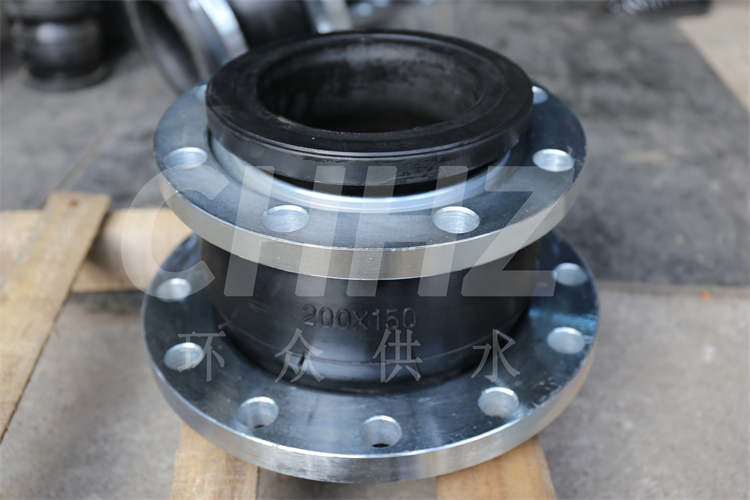
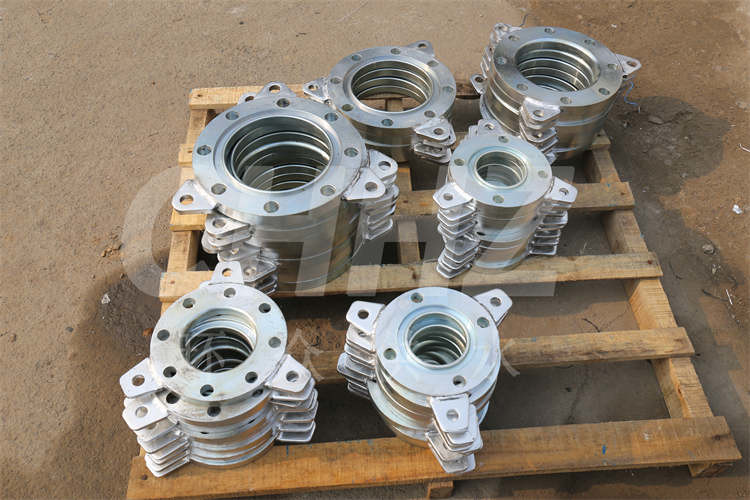
In the field of chemical engineering, the use of rubber joints plays a crucial role in the design and operation of piping systems. These components are essential for accommodating movement, absorbing vibrations, and providing flexibility, thereby ensuring the integrity and functionality of pipework in chemical processing plants. This article delves into the importance of rubber joints in chemical engineering, focusing on their applications, key considerations, and the significance of proper installation and maintenance practices.
Rubber joints are employed in chemical engineering applications to address the challenges associated with conveying corrosive fluids, diverse temperature ranges, and dynamic operating conditions. Their ability to dampen vibrations and mitigate the effects of thermal expansion and contraction makes them indispensable in maintaining the structural integrity of pipelines and equipment. Moreover, rubber joints effectively reduce noise transmission and protect sensitive components from damage caused by mechanical stress.
The selection of rubber joints in chemical engineering applications must consider the compatibility of materials with the conveyed substances. Chemical resistance, temperature tolerance, and pressure ratings are critical factors that determine the suitability of rubber joints for specific process requirements. Additionally, the design and construction of rubber joints should adhere to industry standards and incorporate features that enable easy installation, inspection, and maintenance.
Proper installation is paramount to the performance and service life of rubber joints in chemical engineering applications. Careful attention to alignment, flange connections, and bolt tightening procedures is necessary to prevent premature wear, leakage, and potential safety hazards. Furthermore, periodic inspection and maintenance of rubber joints are essential to identify signs of deterioration, ensure proper sealing, and address any issues that may compromise the integrity of the piping system.
The use of rubber joints contributes to the safety and efficiency of chemical engineering operations by minimizing the risk of leaks, mitigating the transmission of vibrations, and extending the service life of piping systems. Their ability to accommodate movement and maintain tight seals in the presence of aggressive chemicals and fluctuating pressures is instrumental in preventing environmental contamination and ensuring the reliability of industrial processes.
In conclusion, the application of rubber joints in chemical engineering plays a pivotal role in safeguarding the reliability, safety, and performance of piping systems. By selecting appropriate rubber joints, adhering to installation best practices, and implementing proactive maintenance measures, chemical engineers can effectively address the challenges of conveying corrosive fluids and dynamic process conditions. The reliable performance of rubber joints is instrumental in maintaining the integrity of piping systems, enhancing operational efficiency, and promoting the safety of chemical engineering facilities.
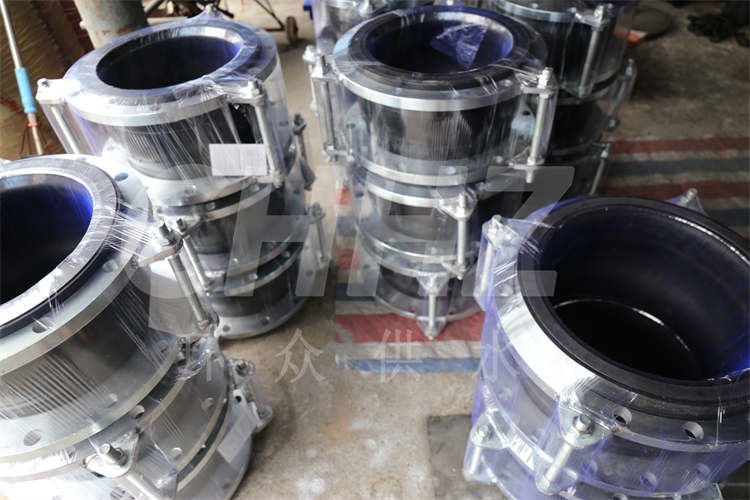