Manufacturing of Rubber Joints: Ensuring Quality and Reliability in Piping Systems
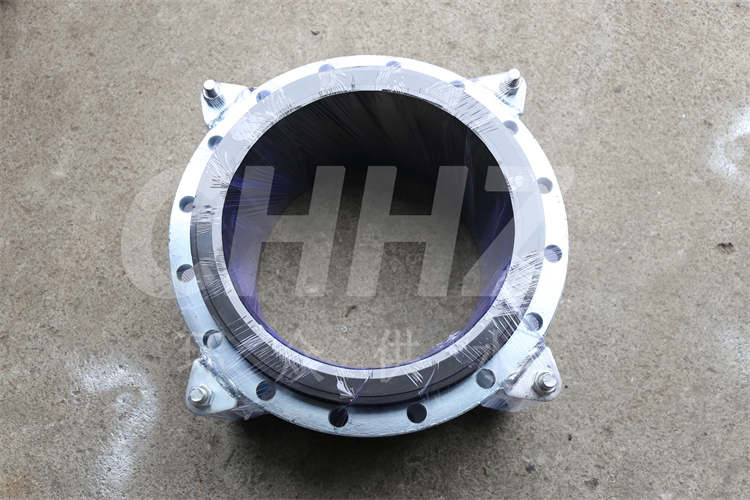
The manufacturing of rubber joints plays a pivotal role in ensuring the integrity and functionality of piping systems across a broad spectrum of industrial and commercial applications. These vital components are designed to accommodate movement, absorb vibrations, and compensate for misalignment in piping systems, thereby promoting durability and reliability. This article provides an overview of the essential aspects involved in the manufacturing of rubber joints, highlighting the key processes and considerations that contribute to their quality and performance.
The manufacturing process of rubber joints begins with the selection of high-quality elastomeric materials, such as natural rubber or synthetic compounds, considering their specific properties and compatibility with intended applications. Advanced elastomer formulations are utilized to ensure resistance to chemicals, heat, pressure, and environmental factors, thereby enhancing the longevity and performance of the rubber joints in various operational conditions.
The fabrication of rubber joints involves precision molding techniques that shape the elastomeric materials into the desired configurations, such as single or multiple arch designs, to provide flexibility and movement absorption. This process necessitates strict adherence to dimensional tolerances and quality standards to achieve consistency and uniformity in the manufactured joints, ensuring optimal performance and reliability when integrated into piping systems.
Incorporating reinforcing materials, such as high-strength fabric or metal components, during the manufacturing process enhances the structural integrity and pressure resistance of rubber joints. The careful selection and integration of these reinforcements contribute to the durability and load-bearing capacity of the joints, enabling them to withstand varying pressures and dynamic forces encountered in piping applications, thus ensuring long-term reliability and safety.
Furthermore, stringent quality control measures are implemented throughout the manufacturing process to validate the structural integrity, material properties, and performance characteristics of rubber joints. Comprehensive testing procedures, including dimensional inspections, pressure testing, and quality assessments, are carried out to verify conformance to industry standards and specifications. This rigorous quality assurance process is essential for delivering rubber joints of superior quality and reliability, meeting the stringent demands of diverse piping system requirements.
In conclusion, the meticulous manufacturing of rubber joints is fundamental to ensuring the quality, reliability, and longevity of piping systems across industrial and commercial sectors. By focusing on material selection, precision molding, reinforcement incorporation, and rigorous quality control, manufacturers can deliver high-performance rubber joints that effectively address the dynamic challenges of fluid conveyance and contribute to the overall efficiency and safety of piping systems. Adopting these best practices in the manufacturing of rubber joints is instrumental in meeting the diverse needs of modern piping applications and upholding the highest standards of quality and performance.
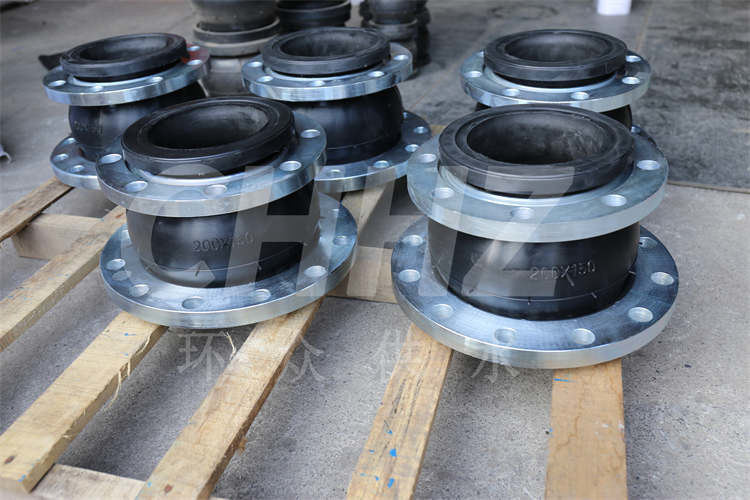