Rubber Joint Installation: Optimizing Piping Systems for Durability and Performance
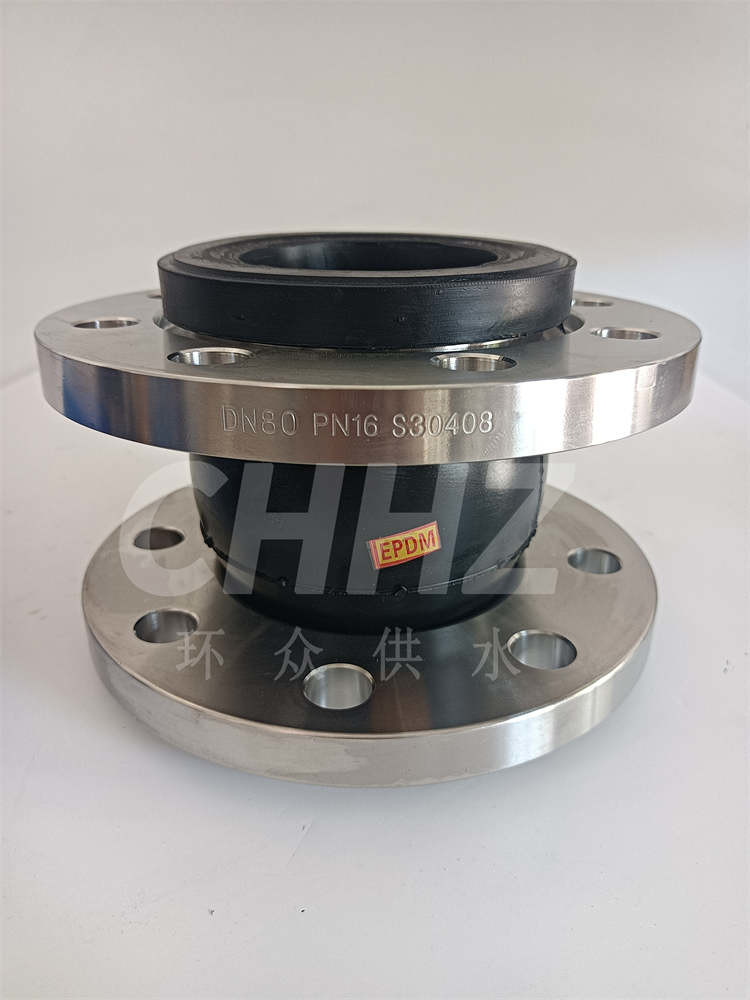
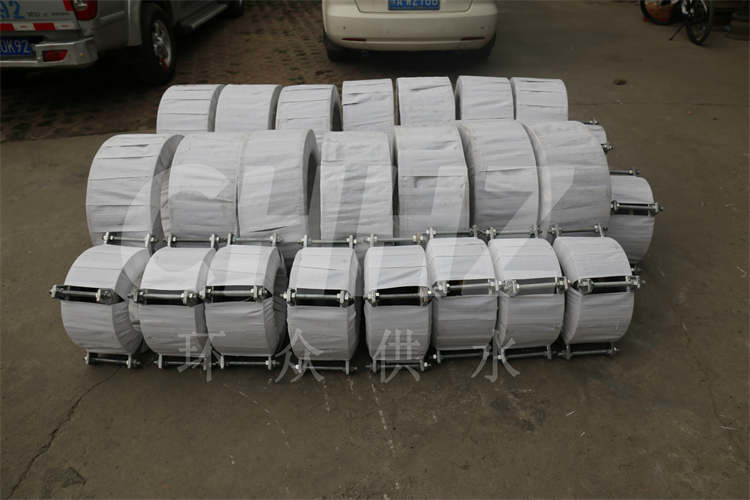
The strategic installation of rubber joints is key to the longevity and efficiency of piping systems across various industrial applications. The placement of rubber joints in pipelines is critical for accommodating movement, absorbing vibrations, and providing flexibility under different operating conditions. This article outlines the significance of proper rubber joint installation, emphasizing its impact on maintaining the integrity and functionality of piping systems and optimizing their performance.
When it comes to the installation of rubber joints, attention to detail and adherence to industry best practices are essential. Before installation, thorough inspection of the rubber joint components is necessary to ensure their quality and integrity. This step includes verifying the compatibility of materials with conveyed substances, checking for any defects or damage, and confirming that the design and specifications align with the specific requirements of the piping system.
Precise alignment and positioning of rubber joints within the piping system are crucial for maintaining the desired functionality and performance. Correct placement minimizes stress on the joints and the adjoining pipework, thus preventing premature wear and potential leakage. Additionally, ensuring proper support for the rubber joints within the system is fundamental in preventing excessive movement and enhancing their longevity.
Flange connections are a critical aspect of rubber joint installation. Tightening bolts to the specified torque values is paramount for achieving a secure, leak-free seal. Proper bolt tightening procedures help to evenly distribute the load across the flange faces, preventing gasket deformation and ensuring uniform pressure distribution, which are essential for reliable sealing and long-term performance of the joint.
Beyond the installation process, regular inspection and maintenance of rubber joints are imperative for preserving their effectiveness and maximizing their service life. Periodic checks for signs of wear, damage, or deterioration, as well as monitoring of seals and connections, help identify potential issues early and prevent costly failures or safety hazards. Addressing any identified concerns promptly through proactive maintenance measures is essential for sustaining the integrity and functionality of the piping system.
In conclusion, the installation of rubber joints significantly influences the durability, performance, and safety of piping systems across industrial applications. Attention to detail, from the initial inspection of components to precise positioning and secure flange connections, is essential for optimizing the functionality and longevity of rubber joints within the system. Adhering to proper installation practices and implementing proactive maintenance measures are instrumental in preserving the reliability and performance of piping systems in diverse industrial settings.
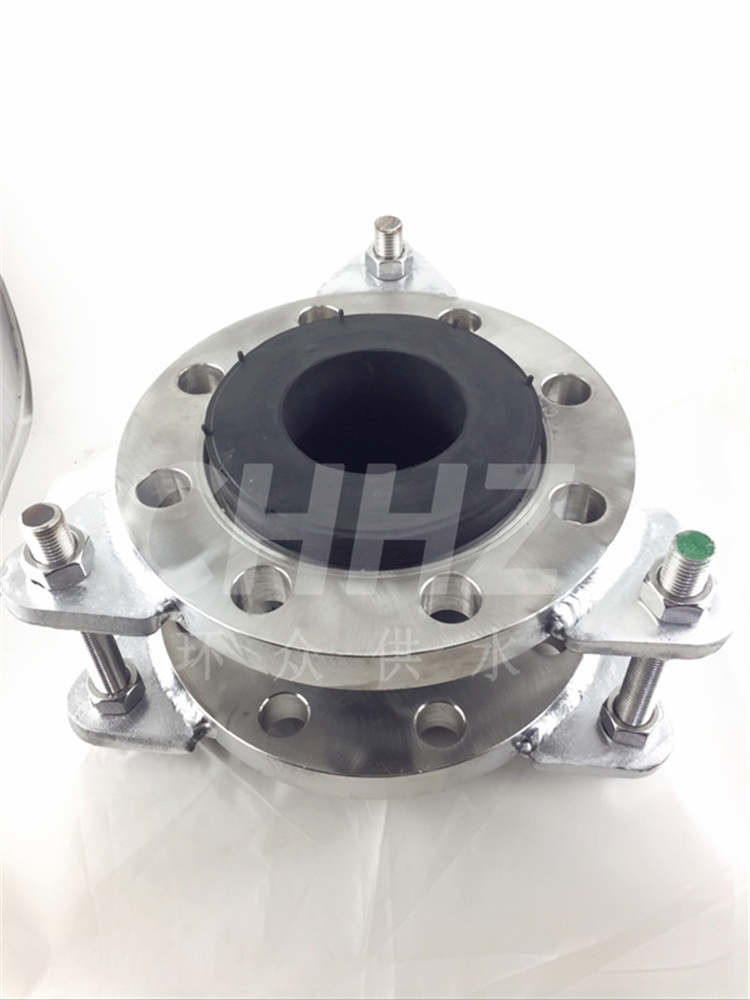