Concentric Rubber Joints: Enhancing Flexibility and Efficiency in Piping Systems
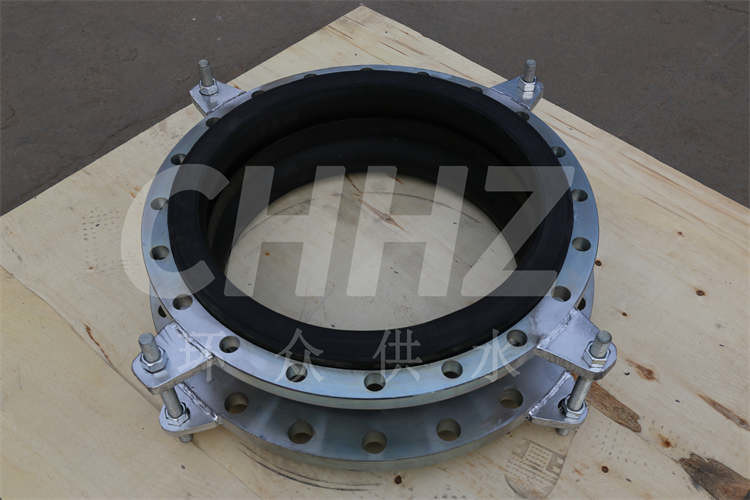
Concentric rubber joints, also referred to as concentric rubber reducers, are essential components in modern piping systems, offering a range of benefits in enhancing flexibility, absorbing vibration, and compensating for misalignment. This article explores the key features, applications, and advantages of concentric rubber joints in various industrial settings.
Key Features:Concentric rubber joints are designed with a conical shape, allowing for the smooth transition of pipe diameter within the joint. This design feature enables the efficient reduction of pipe size, commonly used for connecting piping of different diameters. The concentric configuration ensures that fluid flow remains even and uninterrupted, minimizing pressure imbalances and turbulence within the system. Additionally, these joints are fabricated using high-quality rubber compounds with reinforced layers, offering excellent resistance to corrosion, abrasion, and chemical exposure.
Applications:Concentric rubber joints are widely utilized in a diverse range of industries, including water treatment plants, chemical processing facilities, HVAC systems, and power generation plants. They are particularly valuable in systems where the reduction of pipe diameter is necessary, such as pump connections, transitions between different pipe sizes, and installations in confined spaces. These joints are also commonly integrated into piping systems that require flexibility to accommodate thermal expansion, contraction, and dynamic movement resulting from operational conditions.
Advantages:The implementation of concentric rubber joints brings several advantages to piping systems. Firstly, they can effectively absorb and dampen vibration, minimizing the transmission of mechanical stresses and preventing damage to adjacent piping and equipment. Additionally, the flexibility of the rubber material allows for the accommodation of minor misalignments, reducing the risk of structural fatigue and extending the service life of the overall system. Furthermore, the smooth and continuous geometric transition provided by the concentric design minimizes flow turbulence, pressure losses, and the potential for blockages, thereby optimizing system efficiency and performance.
Furthermore, concentric rubber joints offer cost-effective solutions for system optimization and maintenance. Their installation requires minimal space and can be easily integrated into existing piping configurations, reducing the need for extensive modifications and associated downtime. This makes them particularly valuable for retrofitting applications and system upgrades.
In conclusion, concentric rubber joints play a vital role in promoting the integrity, efficiency, and longevity of piping systems across various industries. Their ability to facilitate smooth transitions, accommodate dynamic movement, reduce vibration, and enhance system performance makes them indispensable components in modern engineering applications. As technology continues to advance, the ongoing development of high-performance rubber compounds and innovative design features further solidifies the position of concentric rubber joints as essential elements in the evolution of modern piping systems.
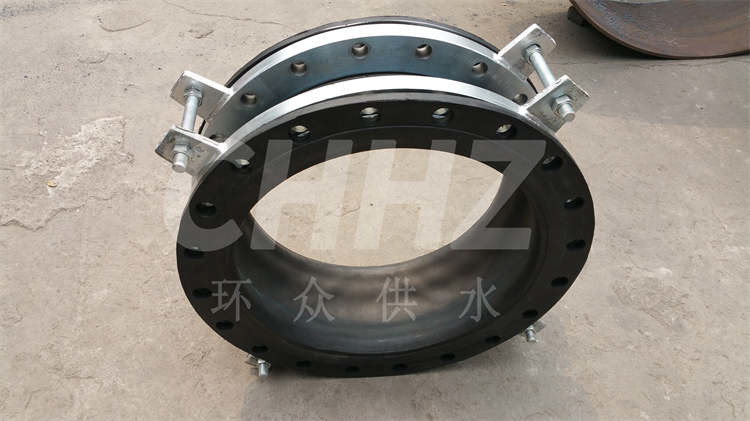