Inspection of Rubber Joints: Ensuring Performance and Safety in Piping Systems
Rubber joints play a critical role in the integrity and functionality of piping systems across various industrial applications. Regular inspection of rubber joints is essential to ensure their performance, longevity, and the overall safety of the system. This article provides an overview of the key aspects involved in the inspection of rubber joints and the importance of this maintenance practice.
Visual Inspection:Visual inspection forms the initial stage of evaluating the condition of rubber joints. During this process, inspectors examine the external surface of the joints for signs of wear, tear, cracks, or deformities. Additionally, the presence of any leaks, corrosion, or damage in the adjacent piping components is assessed. Visual inspection also includes ensuring that the joint is properly anchored and aligned within the system, and that the flanges are intact and free from damage. Any abnormalities observed during this inspection should be promptly documented for further assessment.
Physical Examination:The physical examination of rubber joints involves conducting tests to assess their mechanical properties. This includes evaluating the flexibility, resilience, and overall integrity of the rubber material. Tensile strength, elongation, hardness, and compression resistance are some of the key parameters that are measured to determine the material's condition. Special attention is given to areas where the rubber joint is exposed to high levels of stress, such as the arch and the flange connections. The use of non-destructive testing methods, such as ultrasonic or radiographic inspection, may be employed to detect internal defects that are not visible during visual examination.
Performance Testing:Performance testing involves subjecting the rubber joint to simulated operating conditions to evaluate its functional capabilities. This may include pressurizing the system to the design parameters and observing the joint for any signs of leakage, bulging, or abnormal deformation. The joint's ability to absorb vibration, accommodate thermal expansion, and resist fatigue under dynamic conditions is also assessed. In addition, the performance testing should verify that the joint complies with industry standards, codes, and specific project requirements.
Corrosion and Chemical Resistance:Rubber joints are often exposed to corrosive environments and chemical substances within piping systems. Therefore, the inspection process should include an assessment of the joint's resistance to corrosion, chemical attack, and degradation. This may involve analyzing the material for signs of degradation due to exposure to aggressive media, such as acids, alkalis, or hydrocarbons. Any indication of chemical degradation should prompt further investigation and potential replacement of the affected joints.
Documentation and Maintenance:Documentation of the inspection findings is crucial for establishing a comprehensive maintenance record and identifying trends in joint performance over time. Any deficiencies or areas of concern should be clearly documented, and appropriate corrective actions should be initiated. Regular maintenance, including cleaning, lubrication, and re-tightening of fasteners, is essential to preserve the functionality and service life of rubber joints.
In conclusion, the inspection of rubber joints is a fundamental practice in ensuring the safety, reliability, and performance of piping systems. By conducting thorough visual, physical, and performance assessments, potential issues can be identified early, enabling proactive maintenance and replacement strategies. This proactive approach not only mitigates the risk of unexpected failures but also contributes to the overall operational efficiency and longevity of piping systems.
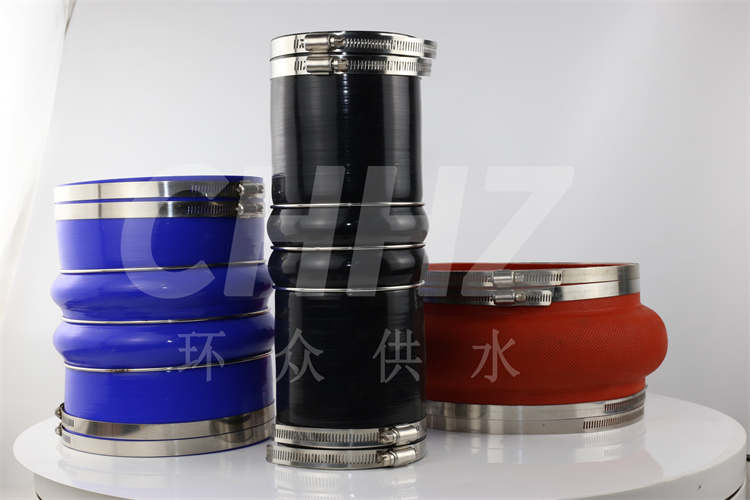