Automatic Rubber Flexible Joint Moulding: Advancements in Production
Introduction: The production of rubber flexible joints has undergone significant improvements with the introduction of fully automated moulding processes. This article will provide a comprehensive overview of the latest advancements in the production of automatic rubber flexible joint moulding.
Advanced Automation: The fundamental shift towards automation has revolutionized the manufacturing of rubber flexible joints. The integration of robotics, computerized control systems, and advanced moulding machinery has enabled the transition from manual to fully automated processes, enhancing precision, efficiency, and consistency in production.
Material Management: Automated systems are adept at managing the intricacies of rubber compound formulations. Robotics and software-based solutions precisely handle the mixing, dispensing, and monitoring of raw materials, ensuring the accurate composition of rubber compounds essential for the production of high-quality flexible joints.
Mould Design and Optimization: Utilizing advanced computer-aided design (CAD) software, mould design for rubber flexible joints has made significant strides. Automated systems facilitate the rapid creation and optimization of mould geometries, allowing for enhanced customization and performance tuning. This includes the integration of reinforcement layers, flange designs, and intricate bellows configurations to meet diverse industrial demands.
Fully Automated Injection Moulding: The core of the automated process lies in the fully automated injection moulding phase. Robotic arms and precision-controlled machinery handle the injection of rubber compounds into custom-designed moulds, ensuring uniform distribution and consistent formation of flexible joints. The seamless integration of injection, curing, and demoulding stages within an automated environment streamlines the production process.
Quality Assurance Systems: Automation has enabled the implementation of robust quality control systems. Advanced sensors, monitoring devices, and automated inspection stations ensure the strict adherence to dimensional tolerances, material properties, and visual quality, mitigating defects in the final products. This leads to a higher standard of reliability and performance in rubber flexible joints.
Efficiency and Productivity: The transition to fully automated moulding has significantly enhanced production efficiency. Continuous operation, reduced cycle times, and minimized manual interventions result in heightened productivity levels, contributing to streamlined supply chains and improved lead times for rubber flexible joints.
Conclusion: The adoption of fully automated moulding processes represents a significant leap in the manufacturing of rubber flexible joints. The amalgamation of advanced automation, material expertise, and precision mould design has culminated in a paradigm shift towards the production of high-quality, standardized, and customized rubber flexible joints catering to a diverse range of industrial applications.
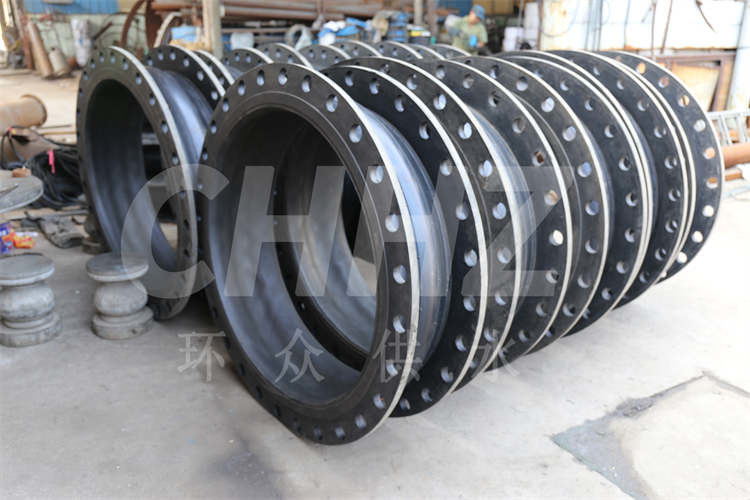