Rubber Joint Valve Components: A Comprehensive Overview
Introduction: Valve components play a vital role in controlling the flow of liquids or gases in various industrial applications. Among these components, rubber joints serve as crucial elements in maintaining the integrity and flexibility of the pipelines. This article aims to provide a comprehensive overview of rubber joint valve components and their significance in industrial systems.
Function and Importance: Rubber joints, also known as expansion joints or flexible connectors, are designed to absorb movements, vibrations, and misalignments within the piping systems. These components function as a flexible link between piping sections, allowing for natural thermal expansion and contraction. The flexibility of rubber joints mitigates stress on the pipeline and reduces the transmission of noise and vibrations, thus protecting the integrity of the system and its surrounding equipment.
Material Composition: Rubber joints are predominantly composed of high-quality elastomers, such as natural rubber, EPDM, neoprene, and synthetic rubbers. These materials possess excellent elasticity, resilience, and chemical resistance, making them suitable for a wide range of applications, including water treatment, HVAC systems, power generation, and chemical processing.
Types of Rubber Joints: There are several types of rubber joints tailored to specific operational requirements. These include single-sphere, double-sphere, threaded union, and flanged rubber joints. Each type offers unique characteristics, such as different levels of movement absorption, pressure ratings, and installation flexibility, allowing for the selection of the most suitable joint based on the specific needs of the application.
Installation and Maintenance: Proper installation and maintenance are critical to the optimal performance and longevity of rubber joint valve components. Thorough inspection of the joints, alignment of the piping, and adherence to manufacturer's guidelines for installation contribute to the effective functioning of the system. Additionally, regular inspection and maintenance schedules help identify potential issues and prevent premature failure of the rubber joints.
Industrial Applications: Rubber joint valve components find widespread application across various industries, including chemical processing plants, water treatment facilities, oil and gas refineries, power generation stations, and HVAC systems. Their versatility, durability, and ability to accommodate movement and vibration make rubber joints an indispensable component in complex piping networks.
Quality Standards and Compliance: Manufacturers adhere to stringent quality standards and regulatory requirements to ensure the reliability and safety of rubber joint valve components. Compliance with industry standards such as ASTM, ANSI, and ISO guarantees that the products meet performance, dimensional, and material specifications, instilling trust and confidence in their application.
Conclusion: In conclusion, rubber joint valve components are integral to the functionality and longevity of industrial piping systems. Their ability to absorb movement, reduce stress, and maintain sealing integrity makes them indispensable in diverse applications. Understanding the function, material composition, types, installation requirements, and industrial significance of rubber joints is vital for optimizing the performance and reliability of complex piping systems.
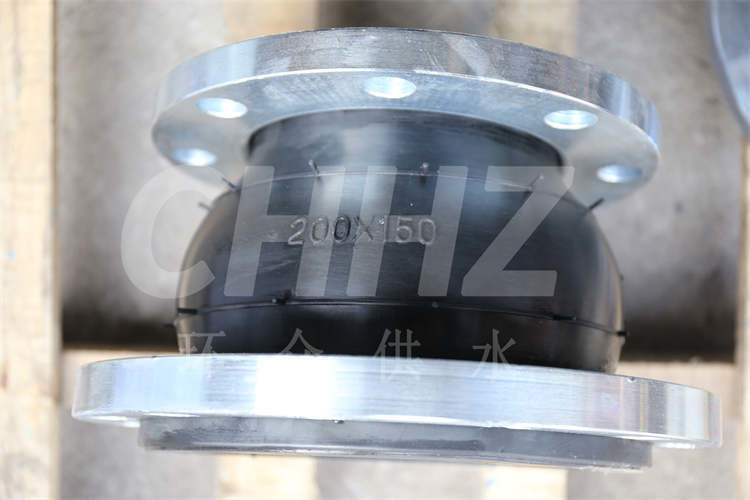