Rubber Joints in Mechanical Piping: Key Features and Applications
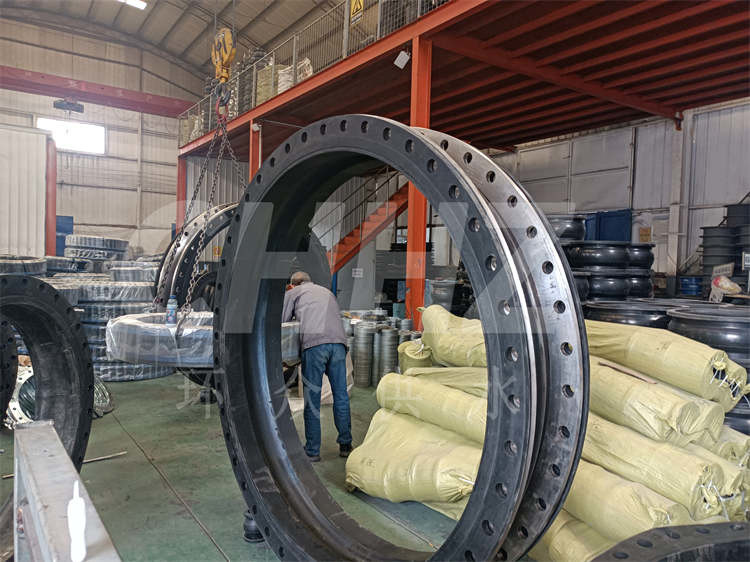
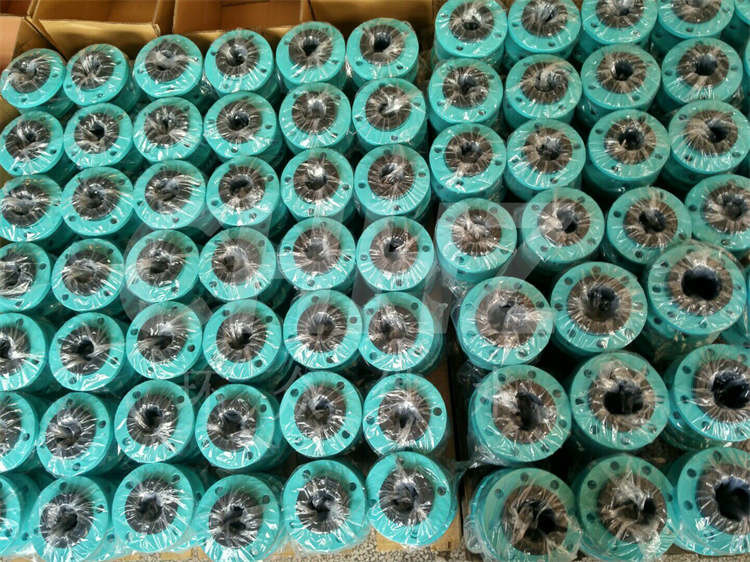
Introduction: Rubber joints, also known as rubber expansion joints or rubber flexible connectors, play a crucial role in mechanical piping systems. This article aims to outline the key features and diverse applications of rubber joints in the realm of mechanical piping engineering.
Features of Rubber Joints:
Flexibility: Rubber joints provide flexibility in mechanical piping systems, allowing for movement caused by thermal expansion, vibration, and misalignment. This feature reduces stress on the piping system and mitigates the risk of damage or failure.
Vibration Isolation: Rubber joints effectively absorb and dampen vibrations, preventing the transmission of potentially disruptive vibrations throughout the piping network. This anti-vibration feature is invaluable in mechanical systems where machinery-generated vibrations are prevalent.
Corrosion Resistance: Many rubber joints are designed with corrosion-resistant properties, making them suitable for use in varied industrial and chemical environments where exposure to corrosive substances is common.
Thermal Compensation: The flexibility of rubber joints allows for the accommodation of thermal expansion and contraction, effectively reducing the impact of thermal stress in the piping system and associated equipment.
Noise Reduction: The inherent elasticity of rubber materials helps in absorbing noise generated by fluid flow and mechanical operations, contributing to a quieter operational environment in mechanical piping systems.
Applications of Rubber Joints in Mechanical Piping:
Industrial Machinery: Rubber joints are widely used in mechanical piping systems that serve industrial machinery, compressors, and hydraulic systems, helping to absorb vibrations and compensating for thermal expansion and contraction.
Heating, Ventilation, and Air Conditioning (HVAC) Systems: Within HVAC installations, rubber joints are employed to dampen vibrations and mitigate the effects of thermal movements and system expansion, ensuring stable and reliable operation.
Pumps and Compressors: In applications involving pumps and compressors, rubber joints play a vital role in minimizing vibrations and accommodating fluid-induced movements, leading to improved system longevity and operational efficiency.
Chemical Processing: Rubber joints find application in chemical processing facilities, where their corrosion-resistant properties and ability to absorb movements contribute to the integrity and reliability of the piping systems.
Water Treatment Plants: Within water treatment facilities, rubber joints are used to absorb hydraulic shocks, compensate for piping movements, and reduce mechanical vibration, thus ensuring the functionality and durability of the piping network.
Conclusion: Rubber joints are integral components in mechanical piping systems, offering essential features such as flexibility, vibration isolation, and resistance to corrosion. Their diverse applications span across industrial machinery, HVAC systems, chemical processing, and water treatment, where they contribute to the reliability and longevity of piping networks. As a result, rubber joints play a foundational role in ensuring the optimal performance and durability of mechanical piping systems across various industrial sectors.
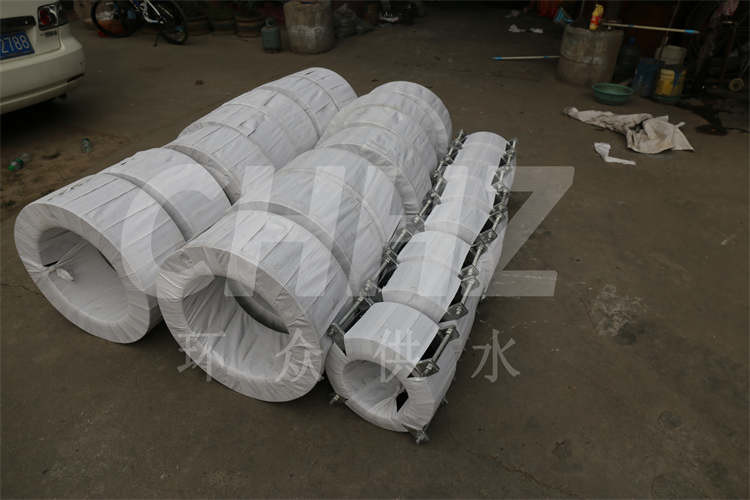