Rubber Expansion Joints in Engineering Piping Systems
Introduction: Rubber expansion joints play a critical role in engineering piping systems by providing flexibility, vibration isolation, and thermal expansion compensation. This article provides an overview of the fundamental aspects and applications of rubber expansion joints in engineering pipelines, addressing their design, functionality, and installation considerations.
Functionality: Rubber expansion joints are designed to absorb movements and vibrations caused by thermal expansion, mechanical stresses, or dynamic loads within piping systems. They accommodate axial, lateral, and angular movements, thus minimizing stress on connected equipment and piping. Additionally, they serve as effective shock absorbers, reducing noise and vibration transmission in industrial and commercial applications.
Design and Construction: The design of rubber expansion joints consists of a rubber element, typically made from synthetic elastomers or natural rubber, and often reinforced with fabric or metal reinforcements. The rubber's flexibility, resilience, and ability to withstand various operating conditions are crucial factors considered during the design phase. Metal components such as flanges or retaining rings are integrated to provide structural support and ensure a secure connection to the piping system.
Operating Conditions and Material Selection: The selection of rubber expansion joints is based on the specific operating conditions, including temperature, pressure, and chemical exposure. Engineering standards and guidelines outline the material specifications, chemical resistance, and permissible temperature ranges to ensure compatibility with the conveyed media and environmental conditions. Factors such as abrasion resistance, UV stability, and fire resistance are also considered based on the application requirements.
Installation and Maintenance: Proper installation of rubber expansion joints is essential to maximize their effectiveness and service life. This includes correct alignment, torque specifications for flange connections, and adequate support to prevent overextension or misalignment during operation. Regular inspection and maintenance are recommended to monitor the condition of the rubber element, as well as the integrity of the connections, ensuring continued performance and reliability.
Application Areas: Rubber expansion joints are utilized in a wide range of engineering applications, including HVAC systems, industrial ducting, power plants, chemical processing facilities, and water treatment plants. Their versatility and adaptability make them suitable for mitigating vibration and movement in various piping systems, contributing to the overall safety and efficiency of the infrastructure.
Conclusion: Rubber expansion joints serve as indispensable components in engineering piping systems, offering flexibility, vibration isolation, and stress relief. Understanding their functionality, design considerations, material selection, installation, and maintenance requirements is crucial in ensuring their optimal performance and longevity within diverse engineering applications. By incorporating these aspects into engineering designs and maintenance protocols, the efficient and reliable operation of piping systems can be sustained.
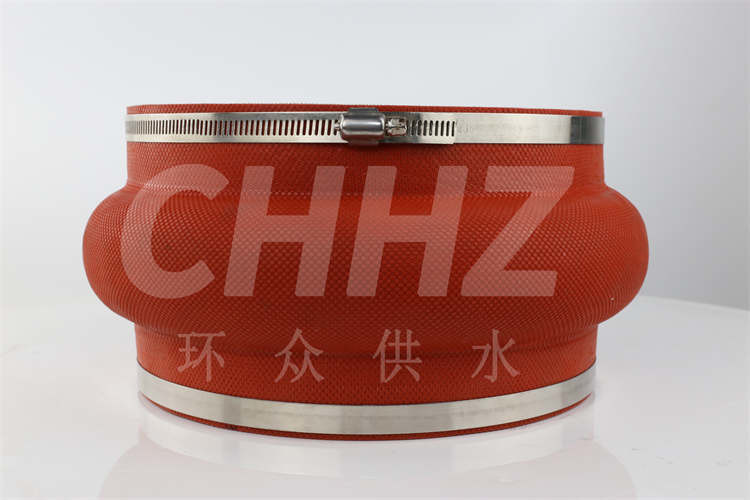