How to Connect Injection-Molded Rubber Hoses: A Guide
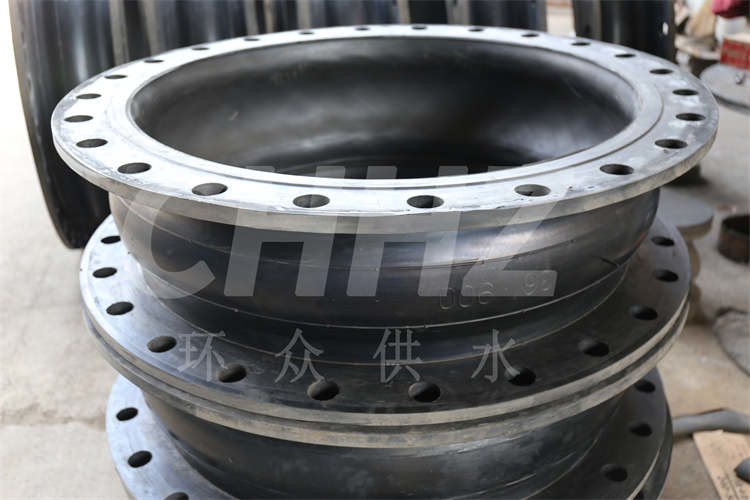
Rubber hoses play a crucial role in various industrial applications, providing a flexible and durable means for fluid transfer. Injection-molded rubber hoses often require specialized methods for connecting joints to ensure leak-proof and reliable performance. This article offers a comprehensive guide on how to effectively connect injection-molded rubber hoses.
Preparation: Before connecting injection-molded rubber hoses, it is essential to ensure that the hose ends are clean, free from contaminants, and properly trimmed to the required length. This promotes a secure and uniform connection, preventing potential leaks and ensuring optimal flow characteristics.
Selection of Fittings: Choose appropriate fittings based on the specific application, operating conditions, and compatibility with the rubber material. Common fitting types include barbed fittings, compression fittings, and threaded fittings. Factors such as pressure rating, chemical resistance, and temperature range should be considered when selecting fittings to ensure compatibility with the intended use.
Barbed Fittings: For connecting injection-molded rubber hoses to barbed fittings, the hose end is stretched and lubricated to facilitate fitting insertion. High-quality hose clamps are then employed to secure the hose to the fitting, ensuring a tight seal and preventing inadvertent detachment during operation.
Compression Fittings: Compression fittings provide a reliable method for connecting injection-molded rubber hoses, particularly in applications requiring a strong, leak-proof joint. The hose end is inserted into the fitting, followed by the compression nut and ferrule. Tightening the compression nut forms a secure seal around the hose, effectively maintaining pressure integrity.
Threaded Fittings: Threaded fittings offer a versatile solution for connecting injection-molded rubber hoses to pipelines and equipment. Properly threading the hose onto the fitting ensures a stable and sealed connection. The use of thread sealants or sealing tape may be necessary to enhance the joint's leak resistance, depending on the specific application requirements.
Special Considerations: In certain applications, such as those involving aggressive chemicals or high-pressure environments, specialized connectors, such as quick-connect couplings or flange fittings, may be required. These fittings provide rapid and secure connections while meeting stringent performance demands, ensuring the safe and efficient operation of the injection-molded rubber hoses.
Inspection and Testing: Following the connection of injection-molded rubber hoses, it is crucial to conduct thorough visual inspections and pressure tests to verify the integrity of the joints. Leakage tests, pressure decay tests, and visual checks for deformation or damage should be performed to ensure reliable and safe operation.
Conclusion: The proper connection of injection-molded rubber hoses is essential for maintaining operational efficiency and safety in industrial systems. By adhering to best practices and selecting suitable fittings, the successful integration of rubber hoses with various connections can be achieved, contributing to the consistent and secure performance of fluid transfer applications.
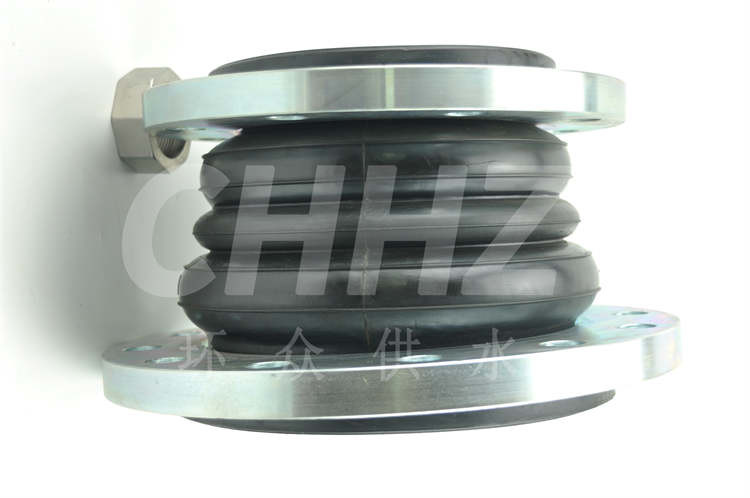