Rotary Joints in the Rubber Industry
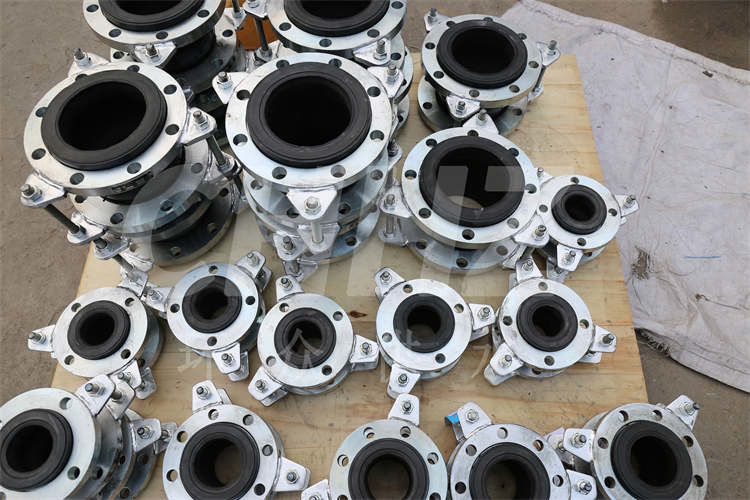
Rotary joints are fundamental components in the rubber industry, serving a vital role in the efficient and continuous operation of various manufacturing processes. These rotary joints, also known as rotary unions, facilitate the transfer of fluid, steam, or air between fixed piping and rotating equipment, enabling seamless connectivity, heat transfer, and fluid distribution. This article examines the significance of rotary joints in the rubber industry and explores their essential functions and applications.
In the rubber industry, rotary joints are employed in a diverse range of machinery and equipment used for the processing, molding, and curing of rubber products. These rotary joints are designed to accommodate the rotational movement of rollers, molds, and other components while ensuring the uninterrupted supply of steam, water, hydraulic fluid, or air to critical process points. Their ability to transfer media from stationary to rotating parts enables the efficient heating, cooling, or lubrication of equipment, contributing to the overall productivity and quality of rubber manufacturing operations.
One of the primary functions of rotary joints in the rubber industry is thermal management. Rubber processing involves heating and cooling stages, such as vulcanization and molding, which require precise temperature control to achieve the desired material properties and product characteristics. Rotary joints facilitate the transfer of hot water, steam, or thermal oil to the rotating elements of curing presses, calenders, and extruders, allowing for uniform and controlled heating or cooling of rubber compounds. This thermal regulation is critical for achieving consistent product quality and optimizing production efficiency.
Another crucial function of rotary joints is the transmission of hydraulic or pneumatic power to rotating machinery in the rubber industry. Hydraulic rotary joints enable the delivery of pressurized hydraulic fluid to actuate clamping devices, rubber extruders, or other equipment with rotating components, ensuring precise and responsive operation. Similarly, rotary joints for pneumatic applications enable the transfer of compressed air for pneumatic cylinders, control systems, and tooling used in rubber processing, thereby enabling essential automation and control functionalities.
Furthermore, rotary joints play a pivotal role in the lubrication of bearings and shafts in rotating equipment within the rubber industry. By providing a continuous supply of lubricating oil or grease to the rotating components of mixers, mills, and other machinery, these rotary joints contribute to the reduction of friction, wear, and maintenance requirements, thereby enhancing the reliability and longevity of critical equipment.
In conclusion, rotary joints are indispensable in the rubber industry, where they enable the seamless transfer of fluids, thermal energy, and power to rotating machinery and equipment. Their functions in thermal management, power transmission, and lubrication are essential for sustaining efficient and reliable rubber manufacturing processes. Whether in vulcanization, molding, or material handling, rotary joints play a pivotal role in supporting the productivity, quality, and performance of the rubber industry.
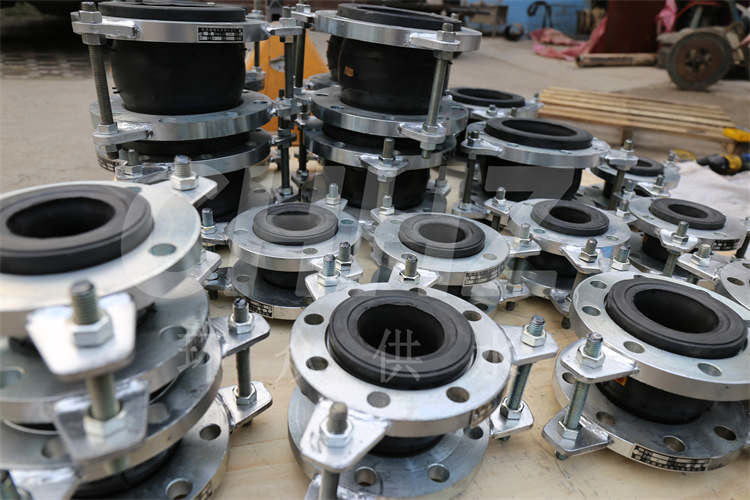