Flexible Rubber Joints in the Chemical Industry
Flexible rubber joints, also known as rubber expansion joints, are integral components in the chemical industry, providing critical support for piping systems to accommodate movement, vibration, and misalignment. This article delves into the significance of flexible rubber joints in chemical applications and examines their key functions, advantages, and considerations for optimal performance.
In the chemical industry, where fluid processing and transportation are central to operations, flexible rubber joints serve as essential connectors for piping systems. These joints are designed to absorb and isolate movement, vibration, and shock within pipelines, thereby safeguarding equipment and structures from mechanical stress and preventing damage or failure. Additionally, flexible rubber joints allow for limited axial, lateral, and angular movement, offering versatility and adaptability to accommodate dynamic operating conditions and thermal expansion in chemical processing facilities.
One of the primary functions of flexible rubber joints in the chemical industry is to mitigate the transmission of noise and vibration. The inherent resilience and damping properties of rubber materials enable the absorption of acoustic and mechanical disturbances arising from fluid flow, equipment operation, or external factors. By minimizing the propagation of vibration and noise through the piping system, flexible rubber joints contribute to a safer and more comfortable working environment while reducing the risk of structural fatigue and equipment malfunction.
Moreover, flexible rubber joints facilitate the compensation of thermal expansion and contraction in chemical piping systems. As temperature variations occur during the processing and transportation of chemicals, the expansion and contraction of piping can exert significant stress on the system. Rubber expansion joints accommodate these thermal movements, allowing for thermal expansion without imposing undue strain on the piping, fittings, or associated equipment. This capability helps to maintain the integrity and operational reliability of chemical piping systems, especially in processes involving fluctuating temperatures.
Furthermore, flexible rubber joints act as effective shock absorbers to protect equipment and pipelines from dynamic loads and pressure surges in chemical applications. Sudden changes in flow rate, valve operation, or pump start-ups can generate hydraulic shocks that may compromise the structural integrity of piping systems. By absorbing and dissipating the kinetic energy associated with these transient events, rubber expansion joints help to minimize the risk of damage and prolong the service life of critical components in chemical processing plants.
In summary, flexible rubber joints play a vital role in the chemical industry by providing essential flexibility, vibration isolation, and thermal compensation for piping systems. Their ability to mitigate noise and vibration, accommodate thermal expansion, and attenuate hydraulic shock enhances the safety, reliability, and longevity of chemical processing facilities. As a result, the proper selection, installation, and maintenance of flexible rubber joints are paramount for ensuring the optimal performance and integrity of piping systems in chemical applications.
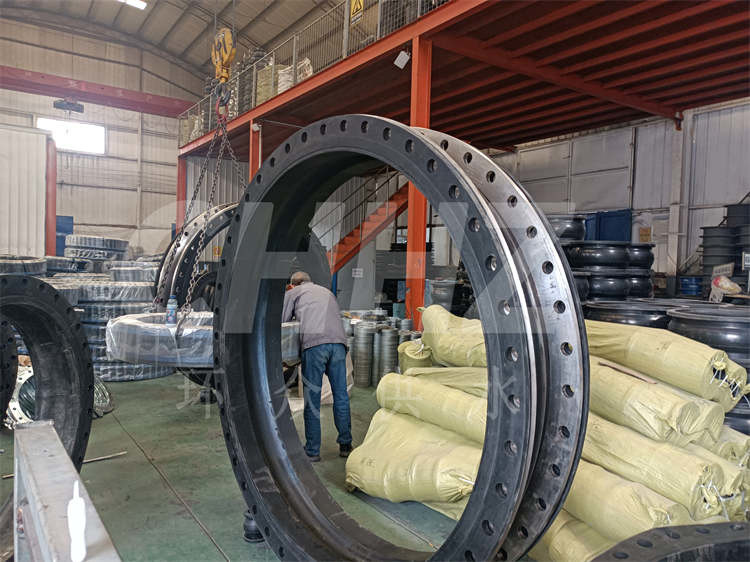