Types of Plastic and Rubber Mold Joints
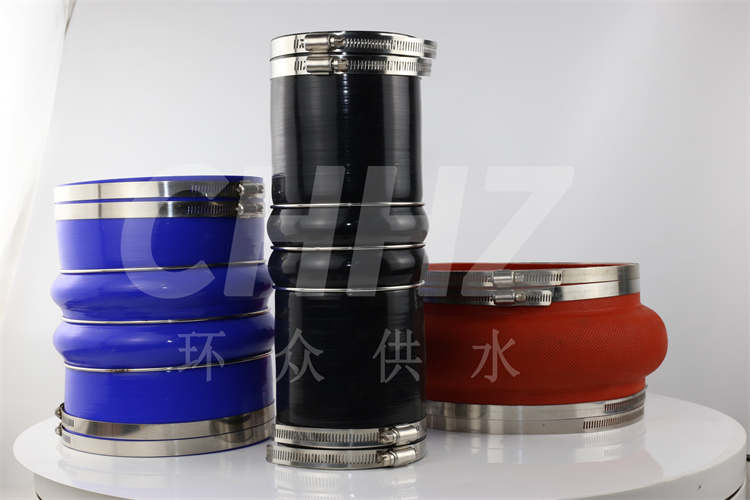
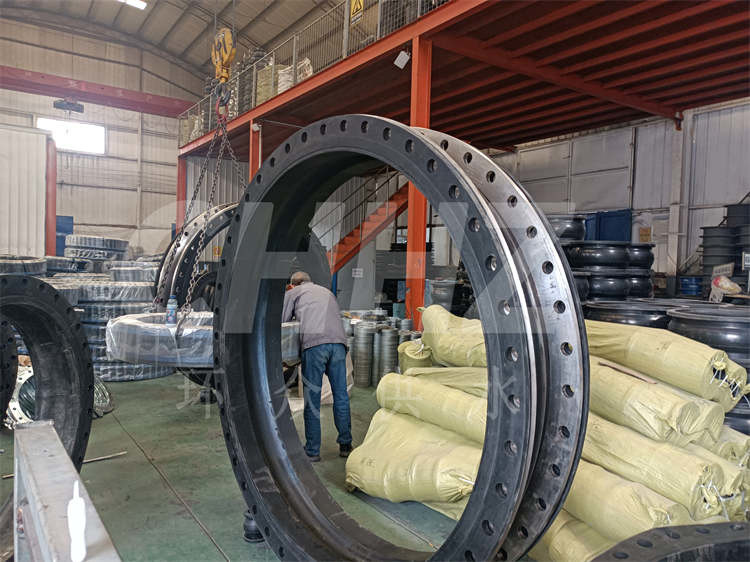
Plastic and rubber molds are widely utilized in various industries for the production of a wide range of components. The jointing of these molds plays a crucial role in ensuring the seamless and efficient manufacturing of high-quality parts. This article outlines the different types of joints used in plastic and rubber molds.
Tongue and Groove Joint: This type of joint consists of a protruding tongue on one mold component that fits into a corresponding groove on the mating component. It provides alignment and prevents lateral movement, ensuring precise mold closure and part consistency.
Clamp and Bolt Joint: Clamp and bolt joints involve the use of clamps and bolts to secure the mold components together. The clamps apply uniform pressure to the joint area, and the bolts ensure a firm and secure connection. This type of joint is suitable for molds that require frequent disassembly.
Quick-Release Coupling Joint: Quick-release coupling joints utilize specialized connectors that allow for rapid assembly and disassembly of mold components. These joints are beneficial for molds that require frequent tool changes or maintenance.
Threaded Joint: Threaded joints involve the use of threaded fasteners such as screws and nuts to secure mold components together. The threaded design provides a strong and reliable connection, making it suitable for molds subjected to high-pressure and high-temperature conditions.
Bayonet Joint: Bayonet joints feature a set of pins on one mold component that align and lock into corresponding slots on the mating component. This design enables quick and secure mold assembly, making it ideal for rapid tooling applications.
Magnetic Joint: Magnetic joints utilize powerful magnets to hold mold components together. This type of joint offers rapid and tool-less assembly, making it suitable for prototype and low-volume production molds.
Snap-Fit Joint: Snap-fit joints feature interlocking features on mold components that snap together, providing a fast and secure assembly without the need for additional fasteners. Snap-fit joints are commonly used in consumer product molds.
Adhesive Bonding: In some cases, mold components are bonded together using specialized adhesives. Adhesive bonding provides a seamless joint and can be used to join dissimilar materials, offering versatility in mold design.
These are just a few examples of the various joint types used in plastic and rubber molds. Manufacturers select the most suitable jointing method based on factors such as mold complexity, production volume, material properties, and operational requirements. A well-designed and properly executed mold joint is essential for achieving consistent part quality and optimizing manufacturing efficiency.
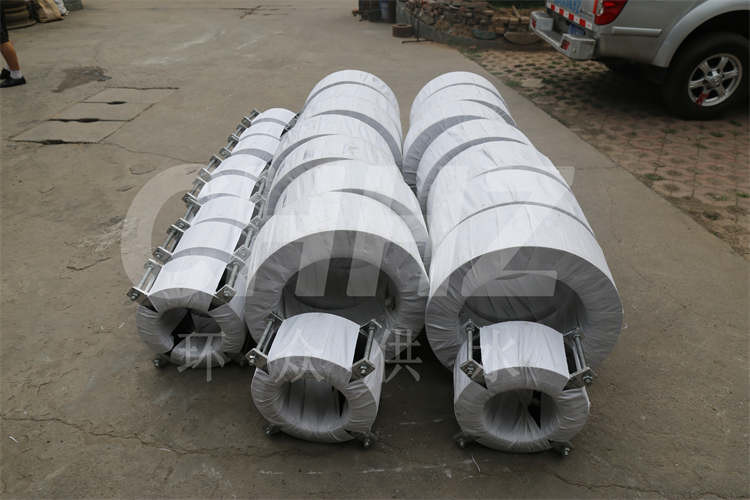