Engineering Pipeline Rubber Flexible Joint Guidelines
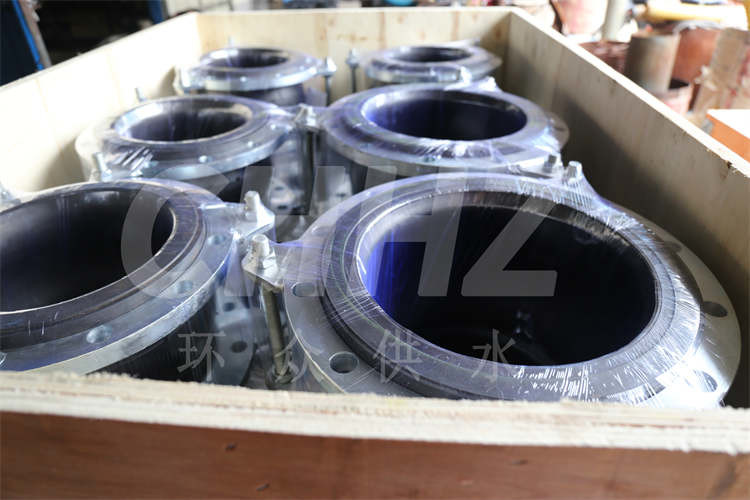
The use of rubber flexible joints in engineering pipeline systems provides an effective solution for absorbing vibration, thermal expansion, and misalignment, thereby extending the lifespan of the pipeline components. This article presents a comprehensive set of guidelines for the installation and use of rubber flexible joints in engineering pipelines, encompassing key considerations and best practices to ensure their successful integration.
Material Selection: Select rubber flexible joints that are specifically designed for the intended application, considering factors such as operating temperature, pressure, media compatibility, and environmental conditions. Materials with superior resistance to abrasion, corrosion, and chemical exposure should be prioritized to mitigate degradation and ensure longevity.
Design Considerations: Evaluate the design parameters of the pipeline system to determine the appropriate size, type, and configuration of rubber flexible joints. Consider factors such as the magnitude of movement, flow dynamics, and system constraints to select the most suitable joint design that aligns with the application's specific requirements.
Installation and Mounting: Ensure that the rubber flexible joints are installed at locations where they can effectively absorb vibration, axial movement, lateral deflection, and angular displacement. Careful attention should be paid to the proper alignment, anchoring, and support of the joints to minimize stress concentrations and facilitate their functional performance within the pipeline system.
Flange Connection: Properly align and secure the rubber flexible joints to adjoining pipes and system components using flange connections. Attention should be given to maintaining uniform bolt torque and implementing effective sealing solutions, such as gaskets, to prevent leakage and maintain the integrity of the pipeline system.
Inspection and Testing: Prior to commissioning, conduct thorough inspections and functional tests to validate the installation and functionality of the rubber flexible joints. Performance tests, including pressure testing, deflection assessments, and visual inspections, should be performed to ensure the joints meet the specified requirements and performance standards.
Maintenance and Service Life: Establish a proactive maintenance program to monitor the condition of rubber flexible joints throughout their service life. Periodic inspections, lubrication, and replacement of components as needed will help maximize the longevity and operational efficiency of the joints within the pipeline system.
Compliance with Standards: Adhere to industry standards, regulations, and codes of practice governing the installation and use of rubber flexible joints in engineering pipelines. Compliance with recognized standards ensures the safety, reliability, and performance of the pipeline system, safeguarding against potential risks and liabilities.
By following these guidelines, engineers and pipeline operators can effectively integrate rubber flexible joints into engineering pipeline systems, ensuring their seamless operation and long-term reliability. Adherence to best practices and considerations outlined in this guide will contribute to the optimal performance, safety, and durability of rubber flexible joints within the context of engineering pipeline applications
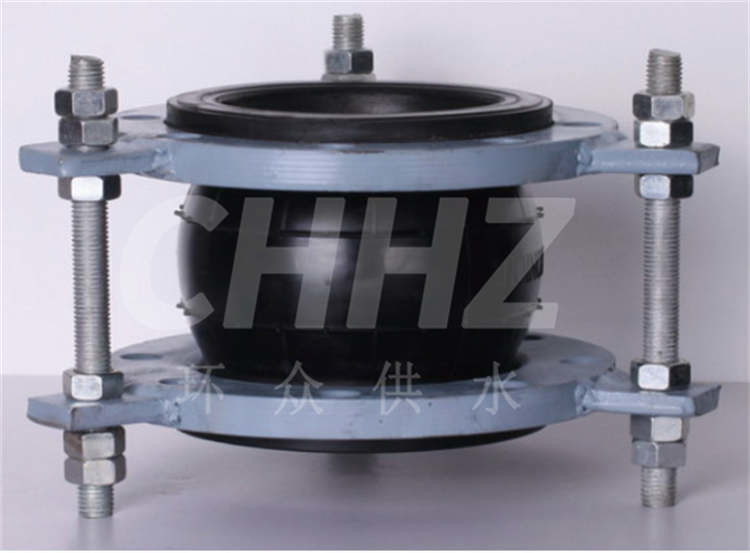