How Rubber Cable Joints Are Made
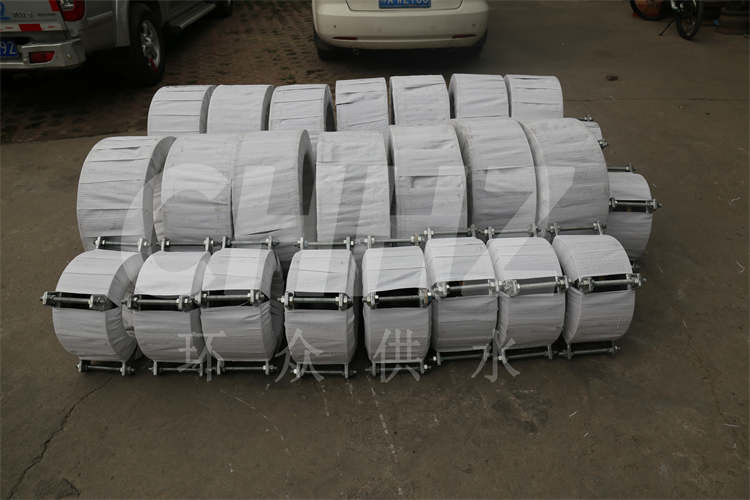
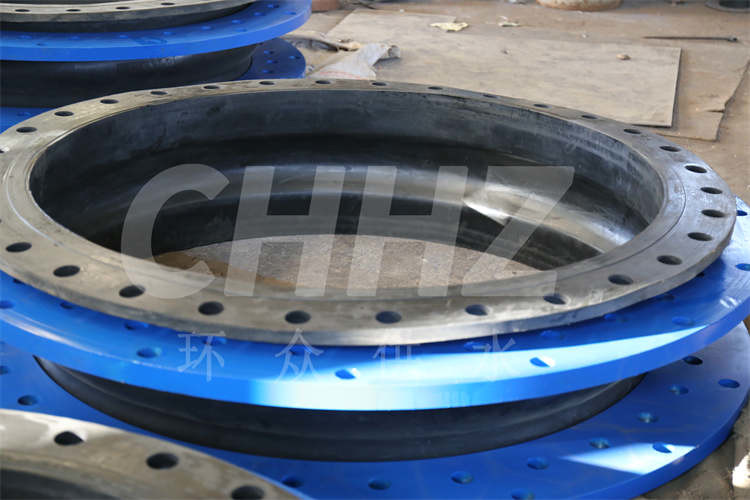
Rubber cable joints are vital components in electrical systems, enabling the connection of cables while ensuring insulation and protection against environmental factors. This article provides an overview of the process involved in manufacturing rubber cable joints and highlights the key steps in their production.
Material Selection: The first step in making rubber cable joints involves the selection of appropriate materials. High-quality rubber compounds with excellent insulating and weather-resistant properties are chosen to ensure the durability and reliability of the cable joints. Additionally, metallic components, such as connectors and fasteners, are carefully selected to meet electrical conductivity and mechanical strength requirements.
Preparation of Rubber Compounds: The selected rubber compounds are prepared by mixing various ingredients, including natural or synthetic rubber polymers, reinforcing agents, fillers, and additives. This mixture is then processed using specialized equipment to achieve the desired consistency and properties, such as flexibility, elasticity, and resistance to electrical stress.
Molding and Extrusion: Once the rubber compound is prepared, it is subjected to molding or extrusion processes to form the specific shapes and structures required for the cable joints. Molding involves the compression or injection of the rubber compound into customized molds that define the shape and dimensions of the joint, while extrusion is used to create continuous lengths of rubber profiles or insulating sleeves that will be used in the assembly of the cable joints.
Vulcanization: After molding or extrusion, the rubber components undergo vulcanization, a crucial process that imparts strength, elasticity, and thermal stability to the material. Vulcanization involves subjecting the rubber parts to heat and pressure in specialized vulcanization chambers, where cross-linking reactions occur, transforming the rubber into a durable and stable material suitable for cable joint applications.
Assembly and Integration: The vulcanized rubber components are then assembled with metallic connectors, insulating sleeves, and other necessary parts to form the complete cable joint assembly. Precision assembly techniques are employed to ensure that the components fit securely and that electrical conductivity and insulation properties are maintained. Additionally, sealing and bonding methods may be used to enhance the environmental protection and mechanical integrity of the cable joint.
Testing and Quality Control: Once the cable joint assembly is completed, rigorous testing and quality control measures are implemented to verify its electrical performance, mechanical strength, and resistance to environmental factors, such as moisture, heat, and mechanical stress. This includes conducting insulation resistance tests, high-voltage withstand tests, and mechanical load tests to ensure compliance with industry standards and specifications.
In conclusion, the manufacturing process of rubber cable joints involves meticulous material selection, preparation, molding, vulcanization, assembly, and testing to ensure that the final products meet the stringent requirements for electrical safety, reliability, and longevity. By adhering to strict quality control measures and utilizing advanced manufacturing techniques, manufacturers can produce high-quality cable joints that effectively fulfill their critical role in electrical systems.
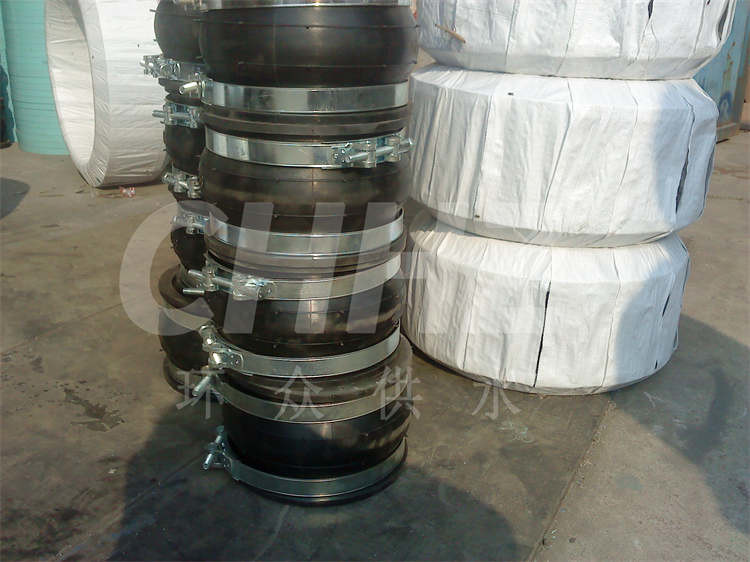