Food-Grade Rubber Connectors for Different Diameters
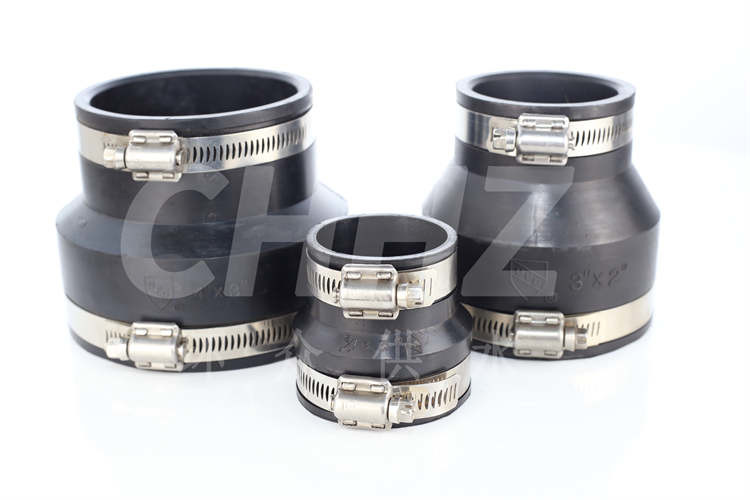
Food-grade rubber connectors play a crucial role in various industries, facilitating the transfer of liquids and products in a hygienic and compliant manner. Specifically, connectors designed for different diameters are essential components in food processing and related applications, providing a flexible and secure means of linking equipment and pipelines. This article sheds light on the significance and production of food-grade rubber connectors for varying diameters.
Importance of Food-Grade Rubber Connectors: In food and beverage processing, pharmaceutical production, and other sanitary applications, maintaining strict hygiene standards is paramount. Food-grade rubber connectors enable the seamless connection of pipes, hoses, and equipment without compromising the purity or integrity of the conveyed substances. These connectors are designed to withstand the demands of sterile processing environments and are constructed from materials approved for contact with edibles and pharmaceutical-grade materials.
Design Considerations for Different Diameters: Connectors for different diameters are engineered with precision to ensure compatibility and functionality across a range of pipe and hose sizes. Factors such as the inner and outer diameters, as well as the flexibility and elasticity of the connector material, are carefully considered to provide a secure and leak-free fit. Moreover, the connectors are designed to accommodate variations in diameter while maintaining sanitary conditions, ensuring ease of installation and maintenance.
Material Selection and Compliance: The production of food-grade rubber connectors for varying diameters begins with the selection of appropriate materials. Silicone rubber, EPDM (ethylene propylene diene monomer), and other FDA-approved elastomers are commonly used due to their excellent resistance to high temperatures, chemicals, and microbial growth. These materials are chosen for their compliance with regulations governing food contact materials, such as FDA (Food and Drug Administration) standards, ensuring that the connectors are safe for use with consumable products.
Manufacturing Process and Customization: The manufacturing process involves precision molding or extrusion of the rubber material to create connectors with the required dimensions and properties. Specialized machinery is utilized to produce connectors tailored to specific diameter combinations, ensuring a snug and reliable fit across diverse piping systems. Moreover, customization options, such as color-coding for size identification and the integration of reinforcing layers for enhanced pressure resistance, are available to meet unique application needs.
Hygienic Design and Cleanability: Food-grade rubber connectors undergo rigorous design and testing to meet stringent hygienic requirements. Smooth, non-porous surfaces are engineered to prevent product entrapment and facilitate thorough cleaning and sterilization procedures. Moreover, the connectors are designed to resist degradation from cleaning agents and sanitization methods, maintaining their integrity and compliance with sanitation standards.
In conclusion, food-grade rubber connectors tailored for varying diameters are indispensable components in industries where hygiene, compliance, and flexibility are essential. By leveraging advanced materials and manufacturing techniques, these connectors provide a critical link in sanitary processing systems, ensuring the safe and efficient transfer of products with diverse diameters while upholding stringent regulatory standards.
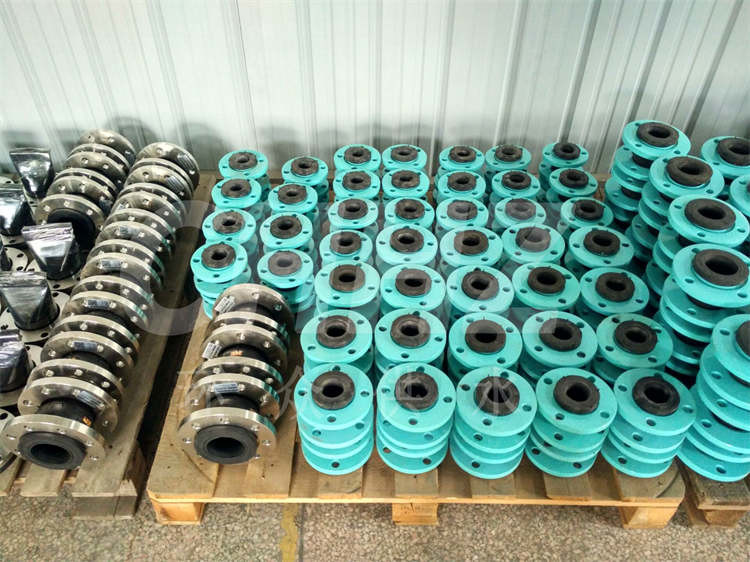