Rubber Hose Connector Manufacturing Process
Rubber hose connectors are vital components in a wide range of industrial applications, facilitating the seamless connection between hoses and equipment for the conveyance of fluids and gases. This article delineates the process involved in the manufacturing of rubber hose connectors, highlighting the critical steps and considerations that contribute to the production of high-quality, durable connectors.
Material Selection: The manufacturing process of rubber hose connectors commences with the careful selection of raw materials. Various grades of rubber, such as EPDM, silicone, and neoprene, are chosen based on the specific application requirements, including resistance to chemicals, heat, and abrasion. These materials are sourced from reputable suppliers and undergo stringent quality checks to ensure compliance with industry standards and regulations.
Compounding and Mixing: Once the raw materials are acquired, they undergo a compounding and mixing process to achieve the desired material properties. The rubber compounds are formulated with precision, incorporating additives and fillers to enhance characteristics such as flexibility, tensile strength, and resistance to environmental factors. Careful attention is paid to the mixing parameters to achieve homogeneity and consistency in the compound.
Extrusion or Molding: The prepared rubber compound is then processed through extrusion or molding techniques to form the basic shape of the hose connector. Extrusion involves forcing the rubber compound through a die to produce connectors with uniform cross-sections, while molding utilizes precision molds to create connectors with specific geometries. Both methods require meticulous control of temperature, pressure, and cooling to achieve accurate dimensions and surface finish.
Vulcanization: Vulcanization is a critical step in the manufacturing process, wherein the molded or extruded connectors undergo curing to attain the desired mechanical properties. This involves subjecting the connectors to heat and pressure within specialized vulcanizing equipment, allowing the rubber to cross-link and achieve its final strength, resilience, and durability. The vulcanization process is tailored to the unique characteristics of the rubber compound and the intended application of the connectors.
Precision Cutting and Finishing: Following vulcanization, the connectors undergo precision cutting to achieve the required lengths and angles. Advanced cutting equipment ensures clean, uniform edges and precise dimensions, contributing to the overall quality and functionality of the connectors. Subsequent finishing processes, such as surface treatments and inspections, are conducted to address any imperfections and ensure conformance to quality standards.
Quality Assurance and Testing: Quality assurance is integral throughout the manufacturing process, with comprehensive testing procedures conducted at various stages. Physical and mechanical tests, such as hardness, elongation, and leak resistance, are performed to verify the performance characteristics of the connectors. Additionally, checks for dimensional accuracy, visual defects, and adherence to regulatory requirements are conducted to guarantee the reliability and safety of the finished products.
Packaging and Shipping: Upon successful completion of the manufacturing and quality control processes, the rubber hose connectors are carefully packaged to prevent damage during transit and storage. Protection against environmental elements, along with clear labeling and instructions, is provided to ensure the integrity of the connectors upon delivery to customers or distribution channels.
In summary, the manufacturing of rubber hose connectors demands meticulous attention to material selection, processing, and quality control. Through adherence to rigorous standards and precision in every production phase, manufacturers can deliver connectors that meet the diverse needs of industries reliant on efficient and reliable fluid handling systems.
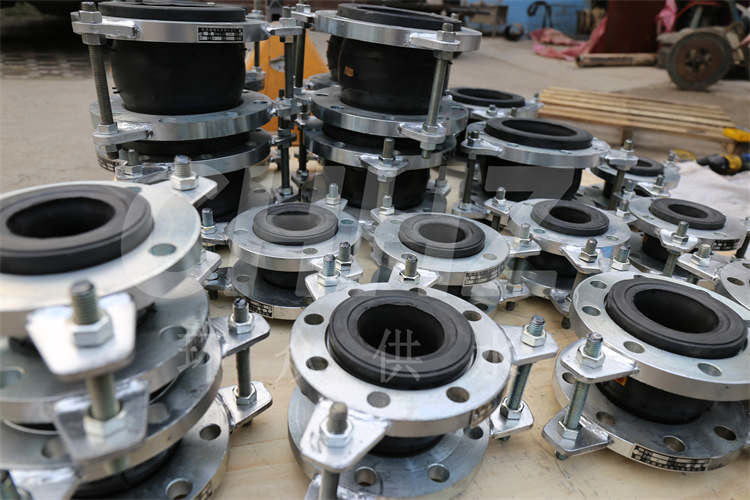