Rubber joints play a crucial role in chemical engineering pipelines by providing flexibility
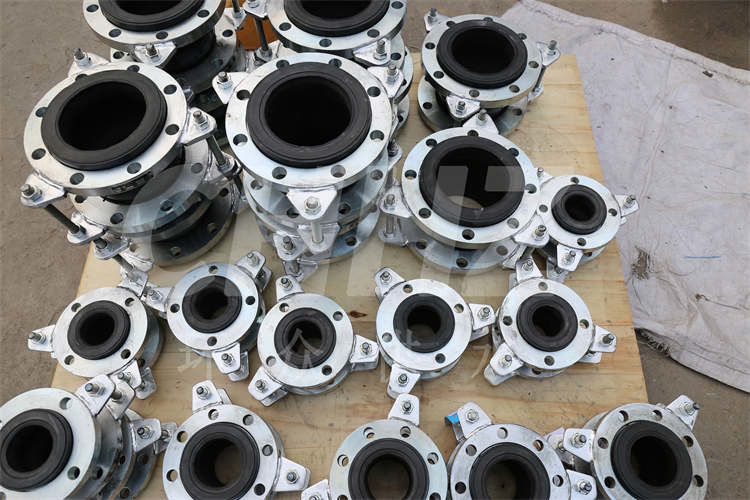
Rubber joints play a crucial role in chemical engineering pipelines by providing flexibility, vibration isolation, and compensating for movement, which are essential for the smooth and safe operation of industrial piping systems. Selecting the right type of rubber joint is crucial to ensure the integrity and performance of chemical engineering pipelines. Several factors should be considered when choosing rubber joints for chemical engineering pipelines, including the operating conditions, type of fluid being transported, environmental factors, and installation requirements.
One of the essential considerations when choosing rubber joints for chemical engineering pipelines is the compatibility of the rubber material with the chemicals being transported. Different rubber materials exhibit varying resistance to chemicals and fluids. For instance, natural rubber, EPDM (ethylene propylene diene monomer), and Viton rubber are known for their excellent chemical resistance, making them suitable for handling a wide range of fluids encountered in chemical engineering applications. Understanding the specific chemical resistance properties of different rubber materials is critical in selecting the most appropriate rubber joint for chemical engineering pipelines.
Another crucial factor to consider is the operating conditions of the chemical engineering pipelines. Factors such as temperature, pressure, and flow rates can significantly impact the performance and longevity of rubber joints. For pipelines operating at high temperatures or under high-pressure conditions, it is essential to choose rubber joints that can withstand these demanding conditions without compromising their structural integrity or functionality. High-temperature-resistant rubber materials such as silicone rubber or fluorocarbon rubber may be suitable for applications involving elevated temperatures, while robust designs that can handle high-pressure environments are necessary for pipelines operating under significant hydraulic loads.
Furthermore, the environmental factors to which the rubber joints will be exposed should be taken into account. Environmental elements such as UV radiation, ozone exposure, and weathering can impact the durability and lifespan of rubber joints. Therefore, selecting rubber joints with excellent weatherability and resistance to environmental degradation is crucial, especially for outdoor or exposed pipeline installations.
Installation requirements and design considerations also play a significant role in selecting suitable rubber joints for chemical engineering pipelines. Factors such as movement compensation, angular deflection capabilities, and installation space constraints should be evaluated to ensure that the selected rubber joints can accommodate the specific installation requirements of the pipeline system.
In conclusion, the selection of rubber joints for chemical engineering pipelines should be based on a comprehensive assessment of factors such as chemical compatibility, operating conditions, environmental exposure, and installation considerations. By considering these critical factors, engineers and specifiers can identify the most suitable rubber joints that will provide reliable performance and longevity in chemical engineering pipeline applications.
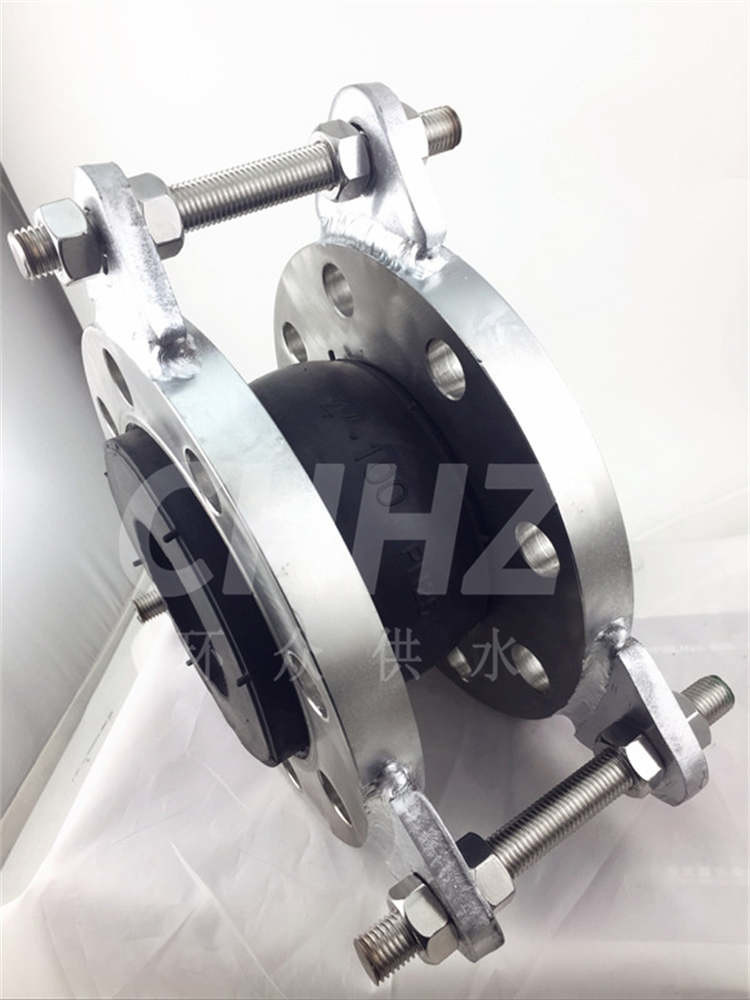