the proper joining of rubber conveyor belts
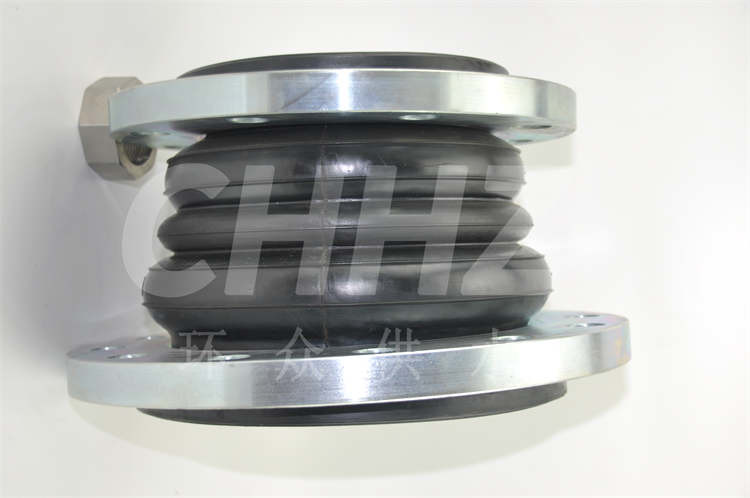
In industrial applications, the proper joining of rubber conveyor belts is crucial for ensuring the safe and efficient transportation of materials. Various methods for joining rubber conveyor belts are employed, each offering distinct advantages and considerations to meet the specific requirements of different conveyor systems.
One common method for joining rubber conveyor belts is through the use of mechanical fasteners. Mechanical fasteners are designed to create a strong, reliable connection between belt ends, allowing for quick and easy installation and maintenance. These fasteners typically consist of metal or plastic components that are secured to the belt ends, providing a sturdy joint that can withstand the rigors of industrial conveying operations. Mechanical fasteners are particularly suitable for applications that require frequent belt maintenance, as they allow for efficient belt splicing and replacement without the need for specialized equipment.
Another widely used method for joining rubber conveyor belts is through the process of vulcanization. Vulcanization involves the use of heat, pressure, and bonding agents to create a permanent and seamless splice between belt ends. This method results in a strong and durable joint that maintains the integrity of the conveyor belt, making it suitable for heavy-duty applications and conveying systems that operate under demanding conditions. Vulcanized splices offer excellent resistance to wear, abrasion, and environmental factors, making them particularly advantageous for conveyor systems in industries such as mining, quarrying, and bulk material handling.
Additionally, cold bonding or cold vulcanization is an alternative method for joining rubber conveyor belts without the need for heat or specialized equipment. Cold bonding adhesives are applied to the belt ends, providing a high-strength bond that allows for quick installation and minimal downtime. Cold bonding splices offer flexibility and ease of application, making them suitable for a wide range of conveyor belt types and operating conditions. However, it is important to consider the environmental and temperature limitations of cold bonding adhesives to ensure their suitability for specific conveyor applications.
Furthermore, newer technologies, such as electronic belt splicing, are emerging as innovative methods for joining rubber conveyor belts. Electronic splicing utilizes advanced equipment to precisely cut and bond belt ends, resulting in high-precision splices that enhance belt performance and longevity. Electronic splicing methods offer superior accuracy and control, making them ideal for conveyor systems that require precise tracking and reduced maintenance.
In conclusion, the selection of a suitable method for joining rubber conveyor belts depends on the specific requirements and operating conditions of the conveyor system. Mechanical fasteners, vulcanization, cold bonding, and electronic splicing each offer unique advantages in terms of strength, convenience, and performance. By carefully considering the application-specific factors, engineers and conveyor system operators can identify the most appropriate joining method to ensure reliable and efficient belt operation in industrial environments.
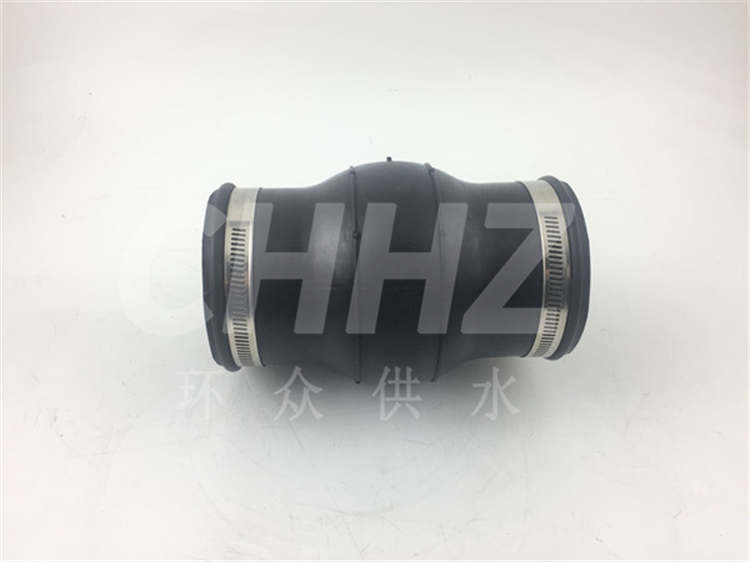