How to Use Rubber Molds for Electrical Wire Joints
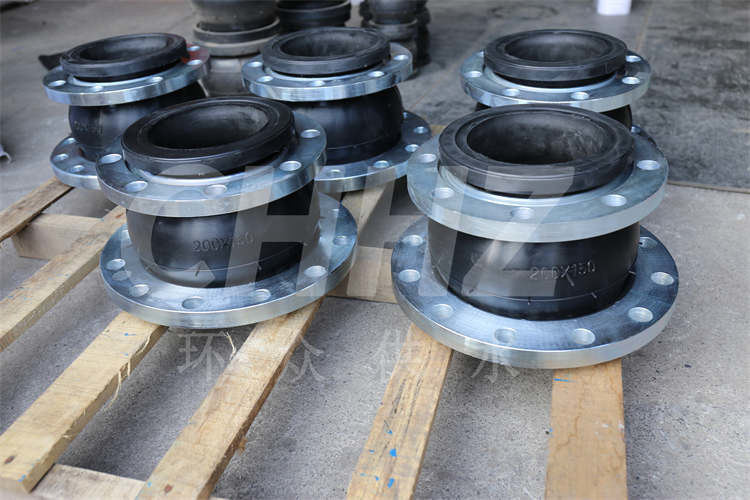
Rubber molds play a crucial role in forming electrical wire joints, ensuring the proper insulation and protection of wire connections. Here are the steps to effectively use rubber molds for electrical wire joints:
Preparation: Before starting the molding process, ensure that the wire connections are clean and free from any debris or contaminants. Additionally, verify that the rubber mold is clean and undamaged to achieve a seamless molding application.
Application of Release Agent: To facilitate the removal of the molded joint, apply a release agent to the interior surface of the rubber mold. This will prevent the rubber from sticking to the mold, enabling easy extraction of the molded wire joint once it has cured.
Encapsulation of Wire Connections: Next, position the wire connections within the rubber mold cavity. Ensure that the connections are properly aligned and securely held in place to create a uniform and well-insulated molding.
Mixing and Pouring of Rubber Compound: Prepare the rubber compound according to the manufacturer's instructions. Thoroughly mix the components to achieve a homogeneous mixture. Once mixed, pour the rubber compound into the mold cavity, completely covering the wire connections to the desired depth. Take care to avoid trapping air bubbles within the mold to ensure a flawless mold.
Curing Process: After pouring the rubber compound, allow it to cure according to the recommended curing time and conditions specified by the rubber manufacturer. This typically involves leaving the rubber mold undisturbed at a specified temperature and humidity level to facilitate the curing process.
Removal of Molded Joint: Once the rubber has fully cured, carefully remove the molded wire joint from the rubber mold. The application of the release agent ensures that the molded joint can be extracted without damaging the mold or the newly formed insulation.
Trimming and Inspection: After demolding, inspect the molded wire joint for any imperfections, such as irregularities in the rubber surface or incomplete encapsulation of the wire connections. Trim any excess rubber material to achieve a clean and uniform finish.
Testing: Before deploying the wire joint, conduct electrical insulation testing to ensure that the molded joint provides the required level of insulation and protection for the wire connections.
In conclusion, the effective use of rubber molds for electrical wire joints involves meticulous preparation, proper encapsulation of wire connections, careful mixing and pouring of rubber compound, precise curing, post-molding inspection, and subsequent testing. When executed with precision, the application of rubber molds ensures the creation of reliable and durable insulation for electrical wire connections, safeguarding them from environmental factors and potential electrical hazards.
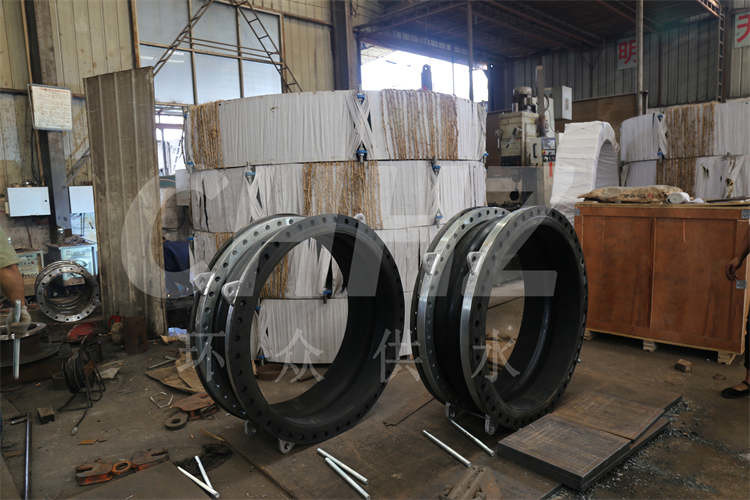