Specifications and Models of Flexible Rubber Joints in Chemical Engineering
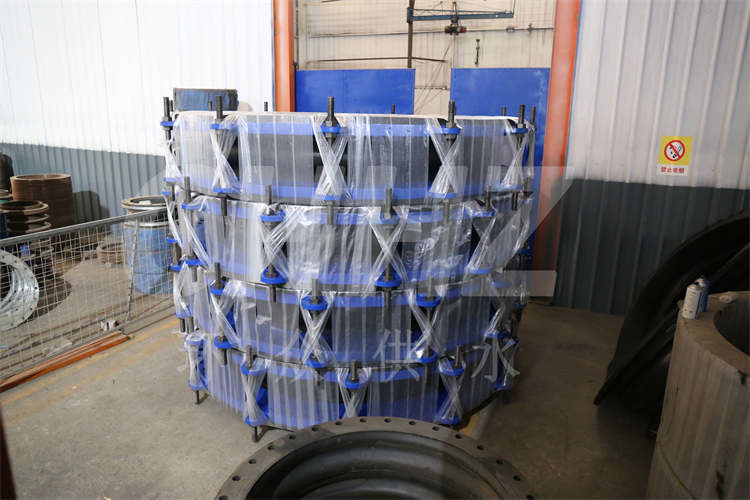
Flexible rubber joints are vital components in the field of chemical engineering, providing crucial flexibility and resilience in piping systems. This article sets out to detail the different specifications and models available for flexible rubber joints, illuminating their importance and varied applications in the chemical industry.
Specifications of Flexible Rubber Joints:
Material Composition: Flexible rubber joints are commonly constructed from high-quality elastomeric materials such as natural rubber, EPDM (Ethylene Propylene Diene Monomer), neoprene, or nitrile rubber. These materials offer resilience, resistance to chemicals, and durability necessary for withstanding demanding chemical engineering environments.
Size Range: Flexible rubber joints are available in a wide range of sizes, typically ranging from 1 inch to 24 inches or even larger, catering to diverse piping system requirements in chemical plants and processing facilities.
Pressure Rating: The pressure rating of flexible rubber joints varies across different models and sizes, commonly ranging from 150 psi to 300 psi. It is essential to select the appropriate pressure rating based on the specific operating conditions within the chemical engineering system.
Temperature Range: These joints are designed to operate within a specific temperature range, ensuring compatibility with the elevated temperatures often encountered in chemical processing. Common temperature ratings range from -20°C to 90°C (-4°F to 194°F), with higher temperature variations available for specialized applications.
Models of Flexible Rubber Joints:
Single Sphere Rubber Joints: This type of rubber joint features a single spherical shape, offering flexibility and allowing for angular movement within the piping system. It is commonly used to absorb vibration, reduce noise, and compensate for minor misalignments in chemical pipelines.
Twin Sphere Rubber Joints: With two spherical shapes connected by a rubber body, twin sphere rubber joints provide enhanced flexibility and absorption of axial, lateral, and angular movements in chemical pipelines. They are suitable for applications where greater movement and misalignment compensation are required.
Threaded Union Rubber Joints: Designed with end connections for easy installation and maintenance, threaded union rubber joints provide a flexible and secure connection in chemical piping systems, allowing for quick disassembly and reassembly for servicing or replacement purposes.
Control Unit Rubber Joints: These specialized rubber joints are equipped with control rods that restrict axial movements, making them ideal for applications where controlled movement is necessary to prevent excessive pipe stress and vibration.
In conclusion, the diverse specifications and models of flexible rubber joints offered in the market cater to a wide array of chemical engineering applications. To ensure optimal performance and longevity, selecting the appropriate size, pressure rating, temperature range, and model of flexible rubber joints is crucial in meeting the specific requirements of chemical piping systems, thereby contributing to the integrity and efficiency of these vital industrial infrastructures.
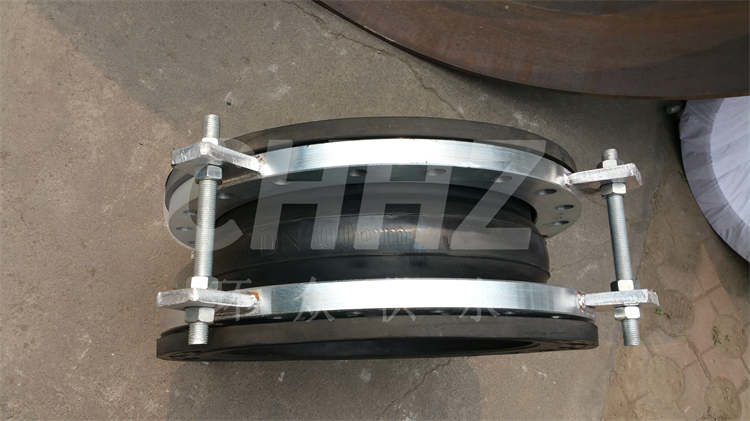