Assembly of Rubber Hose Connectors – Mechanical Aspects
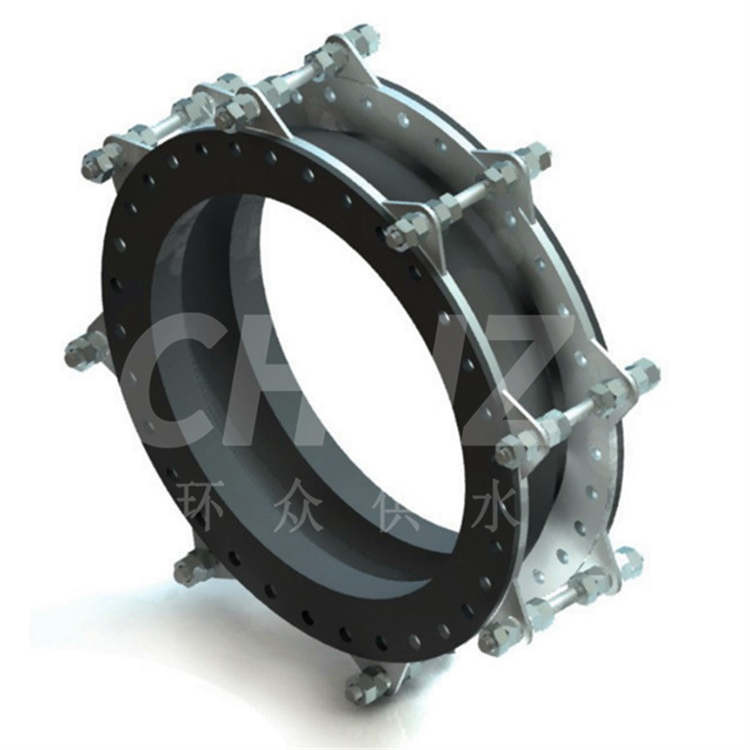
The assembly of rubber hose connectors is a crucial process in various industries, ensuring the secure and efficient coupling of hoses in mechanical systems. This article aims to elaborate on the mechanical aspects involved in the assembly of rubber hose connectors, highlighting the importance of proper installation and the factors influencing their performance.
Connector Types: Rubber hose connectors come in various types, including straight, elbow, tee, and custom-shaped connectors, designed to accommodate specific layout requirements in mechanical systems. Each type demands careful consideration during assembly to ensure proper alignment and fit.
Material Properties: Rubber hose connectors are commonly manufactured from synthetic rubber or elastomeric compounds, offering flexibility, resilience, and resistance to chemical and mechanical stresses. When assembling connectors, it is essential to assess the material properties, including hardness, flexibility, and compatibility with the conveyed substances to ensure optimal performance.
Coupling Mechanisms: The assembly of rubber hose connectors involves integrating coupling mechanisms, such as threaded fittings, camlock couplings, or flanged connections. Proper installation of these coupling mechanisms is critical for maintaining a secure and leak-free joint, preventing loss of fluid or gas and ensuring system integrity.
Installation Techniques: The installation process involves securing the connectors onto the hose ends using appropriate clamping methods, such as band clamps, crimped fittings, or bolted flanges. Careful attention to torque specifications and proper tightening procedures is essential to prevent over-compression or under-compression of the hose materials, which can lead to leakage or premature failure.
Sealing and O-ring Integration: In applications requiring fluid-tight seals, the integration of O-rings and sealing gaskets into the rubber hose connectors is a crucial aspect of assembly. Proper seating and alignment of these seals ensure the prevention of leaks and ingress of contaminants, ensuring the reliability of the mechanical system.
Compatibility and Standards: During assembly, adherence to industry-specific standards and compatibility with system requirements is fundamental. Factors such as pressure ratings, temperature tolerances, and chemical resistance play a pivotal role in the selection and assembly of rubber hose connectors, ensuring their suitability for the intended application.
Quality Assurance: Post-assembly inspection and testing are integral components of the assembly process. Verification of correct alignment, secure attachment, and leak-free performance through pressure or vacuum testing help ensure the reliability and safety of the assembled rubber hose connectors.
In conclusion, the assembly of rubber hose connectors is a critical step in ensuring the functionality and performance of mechanical systems. Attention to the mechanical aspects, including material properties, coupling mechanisms, installation techniques, sealing integration, and adherence to standards, is essential for achieving secure, efficient, and reliable hose connections. By addressing these considerations, industries can uphold the integrity and operational efficiency of their mechanical systems.
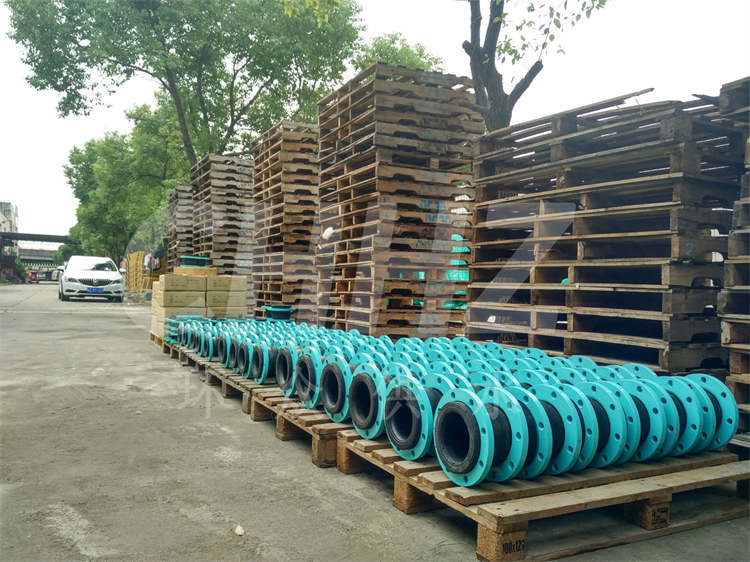