The Issue of Deficient Adhesive Application in Rubber Joint Manufacturing
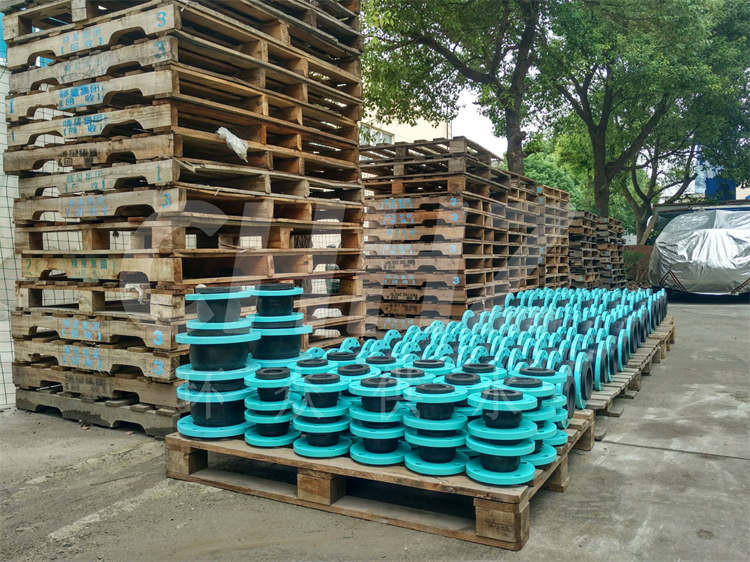
During the manufacturing process of rubber joints, a common problem that arises is the deficient application of adhesive on the flange surface. This issue can have detrimental effects on the overall performance and integrity of the rubber joint, leading to potential leakages, reduced durability, and compromised safety. In this article, we will delve into the implications of deficient adhesive application in rubber joint manufacturing and explore measures to address and prevent this issue.
Implications of Deficient Adhesive Application:
Ineffective Sealing: The primary function of the adhesive in rubber joint manufacturing is to ensure a secure and watertight seal between the flange and the rubber material. Inadequate adhesive coverage can result in incomplete sealing, leading to potential leak paths and compromising the efficacy of the joint in containing fluids or gases.
Reduced Structural Integrity: Proper adhesive bonding is crucial for reinforcing the connection between the rubber and the flange, enhancing the overall structural integrity of the joint. Insufficient adhesive application can weaken the bond strength, making the joint susceptible to separation or delamination under operational stresses.
Compromised Durability: A robust adhesive bond is essential for the longevity and durability of rubber joints, especially in applications involving cyclic loading, vibration, or fluctuating temperatures. Deficient adhesive coverage can accelerate material degradation and decrease the service life of the joint, necessitating premature replacements and maintenance.
Preventive Measures and Solutions:
Adhesive Quality Control: Implementing stringent quality control measures during the adhesive application process is crucial to ensure uniform coverage on the flange surface. Regular inspections, viscosity tests, and adhesive application trials can help identify and rectify any deficiencies in the bonding process.
Standardized Application Techniques: Establishing standardized procedures and application techniques for adhesive coating can help maintain consistency and uniformity across all rubber joint manufacturing processes. This includes proper surface preparation, application methods, and curing parameters to optimize adhesive performance.
Training and Skill Development: Providing comprehensive training to manufacturing personnel on the intricacies of adhesive application is essential for achieving consistent and reliable bonding results. Equipping operators with the knowledge and skills necessary to apply adhesive effectively can significantly mitigate the risk of deficient coverage.
Automated Application Systems: Automation of adhesive application processes using precision equipment and dispensing systems can enhance accuracy, repeatability, and coverage uniformity. Automated systems can ensure that the adhesive is applied in the desired quantity and distribution, minimizing the potential for deficient coverage.
In conclusion, addressing the issue of deficient adhesive application in rubber joint manufacturing is paramount for upholding the quality, reliability, and performance of the final product. By implementing robust quality control measures, standardized application techniques, training initiatives, and automated systems, manufacturers can mitigate the risk of adhesive deficiencies and ensure the consistent integrity of rubber joints in various industrial and commercial applications.
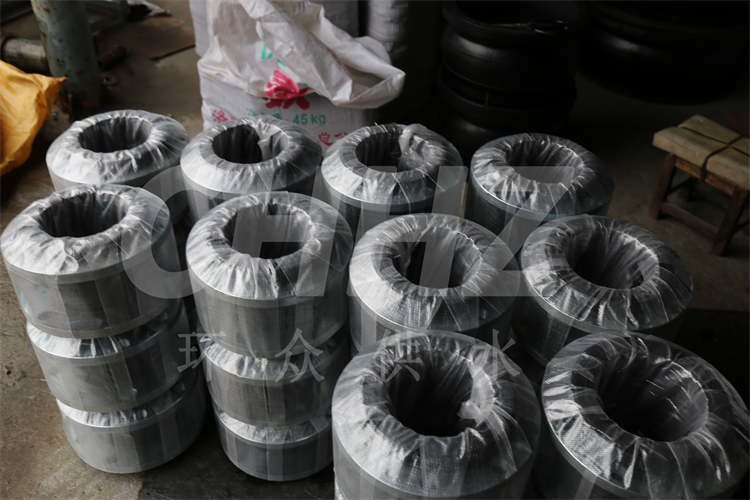