Rubber Flexible Joint Production Workshop: A Comprehensive Overview
The production of rubber flexible joints is a critical process in various industrial applications, where the need for reliable and durable piping systems is paramount. Among the integral components of these systems, rubber flexible joints play a key role in absorbing vibrations, accommodating misalignments, and compensating for thermal expansion, thus ensuring the integrity and longevity of the overall piping infrastructure. In this article, we will provide a comprehensive overview of the production workshop for rubber flexible joints, highlighting the key processes, quality control measures, and technological advancements involved.
Manufacturing Processes
Raw Material Preparation: The production process commences with the meticulous selection and preparation of high-quality raw materials, including rubber compounds, reinforcing materials, and other additives. The mixing and compounding of these materials are conducted with precision to achieve the desired physical and chemical properties in the final rubber joint product.
Molding and Forming: Once the raw materials are prepared, they undergo molding and forming processes to shape the rubber into the desired configurations for the flexible joints. This involves techniques such as compression or injection molding, where the rubber material is subjected to heat and pressure to attain the required geometries and dimensions.
Reinforcement Integration: Many rubber flexible joints require internal reinforcing components, such as fabric or metal inserts, to enhance their structural integrity and performance. The integration of these reinforcements is a critical step, often involving specialized bonding and assembly processes to ensure optimal adhesion and mechanical properties.
Vulcanization and Curing: Vulcanization, a thermal process involving the application of heat and pressure, is employed to cross-link the rubber molecules and impart the necessary strength, elasticity, and chemical resistance to the flexible joints. Proper curing cycles and control of temperature profiles are essential to achieve consistent material properties and dimensional stability.
Quality Control Measures
Material Testing: Throughout the production process, rigorous material testing is performed to validate the physical, mechanical, and chemical properties of the rubber compounds and other raw materials. This ensures compliance with industry standards and specifications, as well as the consistent quality of the final product.
Dimensional Inspection: Precision machining and molding techniques demand meticulous dimensional inspection to verify the accuracy of geometries and tolerances in the finished rubber flexible joints. Advanced metrology and inspection tools are utilized to maintain strict adherence to design specifications.
Performance Evaluation: Functional testing, including pressure, temperature, and vibration trials, is conducted to assess the performance characteristics of the rubber flexible joints under simulated operational conditions. This comprehensive evaluation ensures their suitability for diverse industrial applications.
Technological Advancements
The production of rubber flexible joints has benefited from technological advancements, such as automated manufacturing systems, advanced rubber formulations, and predictive quality control tools. Automated molding and assembly equipment, coupled with real-time monitoring and feedback systems, have enhanced production efficiency, consistency, and flexibility. Furthermore, the development of innovative rubber formulations, including elastomeric compounds with superior wear resistance, chemical compatibility, and fatigue resilience, has expanded the performance envelope of rubber flexible joints in demanding applications. Predictive quality control tools, such as non-destructive testing methods and data analytics, enable proactive defect detection and process optimization, further elevating the reliability and quality of the manufactured joints.
In conclusion, the production workshop for rubber flexible joints encompasses a diverse array of processes, quality control measures, and technological advancements aimed at delivering high-performance, durable products for industrial piping systems. By maintaining stringent material standards, precision manufacturing techniques, and embracing technological innovation, manufacturers can ensure the consistent quality, reliability, and resilience of rubber flexible joints in various sectors, including petrochemical, water treatment, HVAC, and power generation.
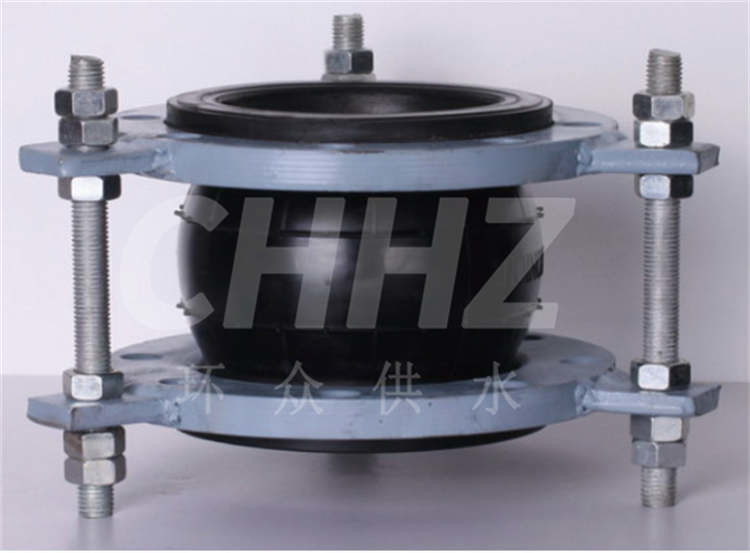