Industrial Rubber Belt Jointing Techniques
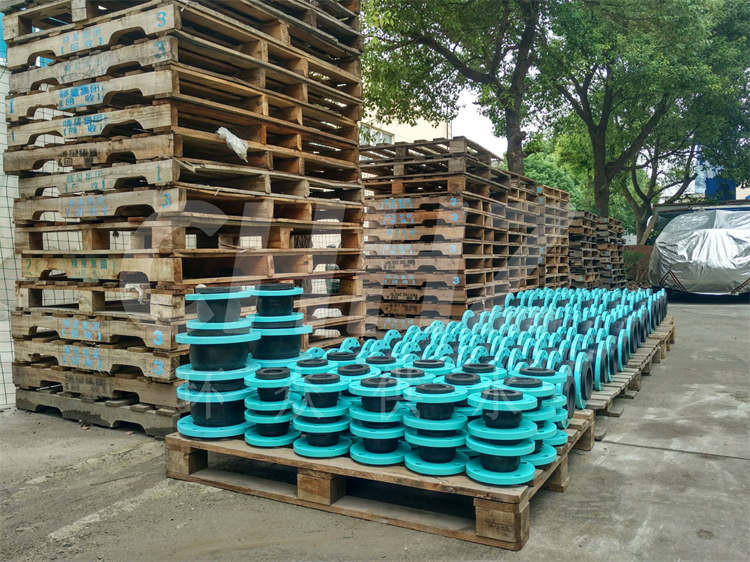
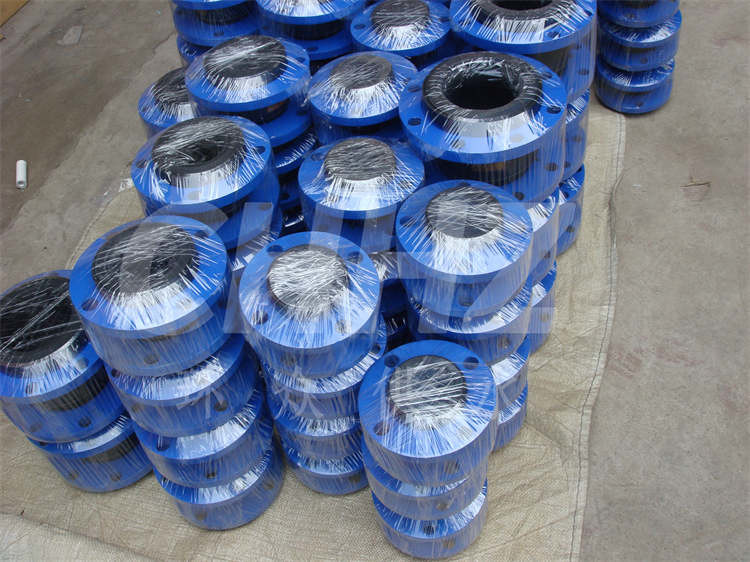
Introduction: In industrial conveyor systems, the proper joining of rubber belts is essential to ensure seamless material handling operations, prevent downtime, and maintain operational safety. This article provides an overview of various techniques used for joining industrial rubber belts, elucidating the processes involved, along with their advantages and applications in diverse industrial settings.
Vulcanization: Vulcanization, a widely used method for joining rubber belts, involves the application of heat and pressure to create a secure and durable bond between belt ends. This process typically utilizes specialized vulcanizing equipment, such as presses and heating platens, to facilitate the fusion of rubber compounds, resulting in a homogeneous joint with excellent tensile strength and resistance to abrasion. Vulcanized joints are ideal for heavy-duty applications in industries such as mining, construction, and bulk material handling due to their robustness and longevity.
Mechanical Fasteners: Mechanical fasteners provide a dynamic and versatile solution for joining rubber belts, allowing for quick assembly and disassembly of the belt sections. These fasteners come in various designs, including hinged, solid plate, and staples, and are installed using specific tools and equipment to securely connect the belt ends. Mechanical fasteners offer significant advantages in terms of ease of installation, maintenance, and the ability to handle frequent belt repairs or replacements, making them suitable for applications requiring flexibility and efficiency in conveyor operations.
Cold Bonding: Cold bonding, also known as cold vulcanization, involves the use of adhesives and bonding agents to create a durable and flexible joint between rubber belt ends. This method is particularly useful for on-site belt repairs or when access to vulcanization equipment is limited. Cold bonding techniques offer the advantage of rapid curing times, enabling expedited repairs and minimizing downtime in conveyor systems. Additionally, they provide good adhesion properties and are capable of accommodating a wide range of operating temperatures and conveying materials.
Overlap Welding: Overlap welding, also referred to as finger splicing, utilizes specialized equipment to create a strong and smooth joint by interlocking the belt ends and bonding them with a combination of heat and pressure. This method ensures a continuous and uniform belt surface, minimizing the risk of material spillage and enhancing the overall efficiency of material transport. Overlap welding is particularly suitable for applications involving the handling of finely powdered or granular materials, as well as in food processing and packaging industries where belt cleanliness and hygiene are critical considerations.
Conclusion: The selection of appropriate rubber belt jointing techniques depends on the specific operational requirements, environmental conditions, and material handling characteristics of industrial conveyor systems. By leveraging the diverse range of joining methods available, conveyor system operators and maintenance professionals can optimize the performance, reliability, and longevity of rubber belts, ensuring seamless material transport and operational efficiency across various industrial sectors.
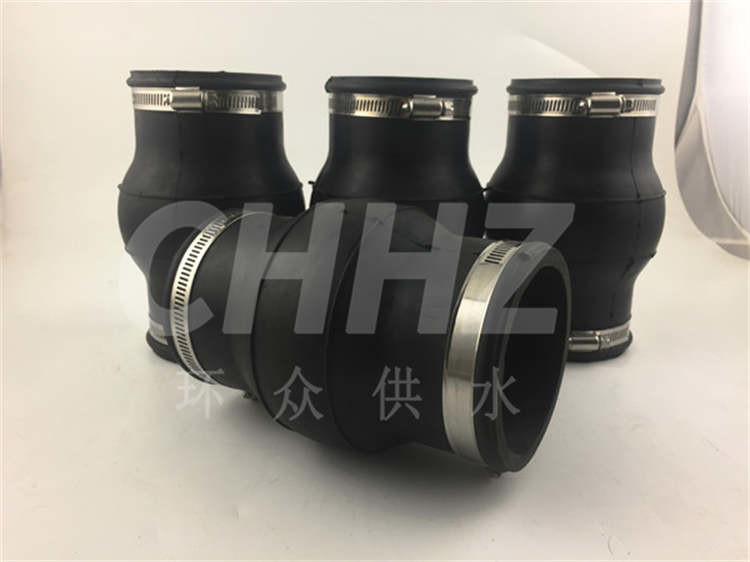