Customized Manufacturing of Flanged Rubber Expansion Joints
Introduction: Flanged rubber expansion joints play a crucial role in fluid handling systems by providing flexibility, vibration isolation, and shock absorption. In various industrial applications, the customization of these expansion joints to meet specific operational requirements is essential. This article outlines the process of custom manufacturing flanged rubber expansion joints, including design considerations, materials, and fabrication techniques, to achieve optimal performance and longevity in diverse fluid handling systems.
Design Considerations: Custom manufacturing of flanged rubber expansion joints begins with a comprehensive analysis of the application requirements, including operating pressures, temperatures, fluid media, movement capabilities, and environmental conditions. Tailoring the design to accommodate these factors ensures that the expansion joints effectively mitigate vibrations, compensate for thermal expansion or contraction, and resist corrosive elements present in the fluid handling environment.
Materials Selection: The selection of high-quality elastomeric compounds, such as natural rubber, EPDM, neoprene, or silicone, is crucial in custom manufacturing flanged rubber expansion joints. These materials offer varying degrees of resistance to heat, chemicals, abrasion, and weathering, enabling the expansion joints to withstand demanding operating conditions. Furthermore, the choice of reinforcing materials, such as textile or metal inserts, enhances the structural integrity and pressure-handling capabilities of the expansion joint, contributing to its long-term reliability.
Fabrication Techniques: Custom fabrication of flanged rubber expansion joints involves precision cutting, molding, and vulcanization processes to achieve the desired shape, size, and performance attributes. Advanced manufacturing techniques, including computer-aided design (CAD) and computer numerical control (CNC) machining, ensure dimensional accuracy and consistency in flange alignment, bolt hole patterns, and overall geometry, facilitating seamless integration into existing piping systems. Additionally, specialized molding methods, such as compression or injection molding, are employed to form intricate shapes and reinforcement configurations, ensuring the integrity of the expansion joint under a wide range of operating conditions.
Quality Assurance: Stringent quality control measures are integral to the custom manufacturing of flanged rubber expansion joints. Comprehensive inspection protocols, including dimensional checks, material testing, and leak-proof integrity assessments, guarantee that each expansion joint complies with industry standards and customer specifications. Non-destructive testing methods, such as pressure and performance testing, validate the expansion joint's ability to withstand fluid pressures, temperature differentials, and dynamic movements, ensuring its reliability and longevity in demanding fluid handling applications.
Conclusion: Custom manufacturing of flanged rubber expansion joints enables the creation of tailored solutions that precisely suit the unique requirements of fluid handling systems across industries such as petrochemical, water treatment, power generation, and HVAC. By integrating design expertise, advanced materials, and precise fabrication techniques, manufacturers can deliver expansion joints that excel in providing fluid system flexibility, absorbing vibrations, and extending the service life of critical piping infrastructure.
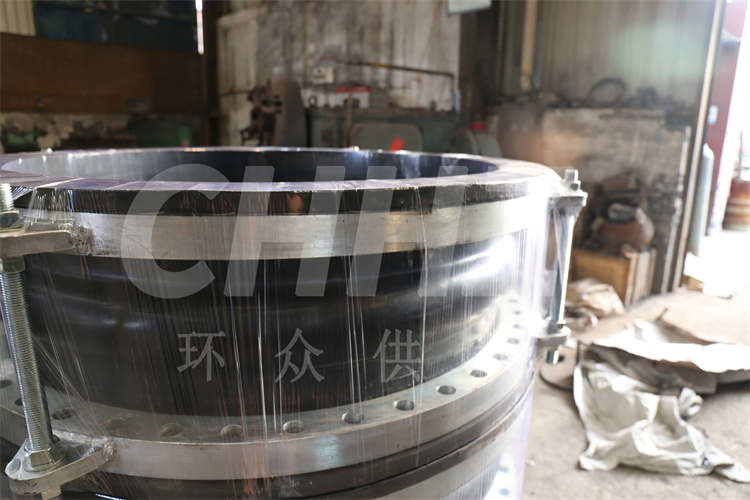