Rubber Cable Connector Production Line
Introduction: The demand for reliable and efficient electrical connections in various industries has led to the development of advanced production lines for rubber cable connectors. These connectors play a critical role in ensuring the seamless transmission of power and signals in diverse applications, including industrial machinery, automotive systems, and electrical infrastructure. This article provides insights into the key processes and technologies involved in the production line for rubber cable connectors, emphasizing the importance of precision, quality control, and innovation in meeting the evolving requirements of electrical connectivity solutions.
Extrusion and Compounding: The production process of rubber cable connectors commences with the extrusion and compounding of high-quality rubber materials, such as ethylene propylene diene monomer (EPDM) or silicone, combined with conductive additives. Advanced extrusion machinery equipped with precision controls ensures the uniformity of the rubber compound, enabling the formation of insulating and jacketing layers with consistent thickness and electrical properties. Careful compounding of rubber materials and conductive fillers contributes to the desired electrical conductivity, flexibility, and resistance to environmental factors, enhancing the performance and longevity of the cable connectors.
Molding and Vulcanization: The next phase of the production line involves the molding and vulcanization of rubber cable connectors. Utilizing precision molds designed to exact specifications, the rubber compounds are shaped into connector components that accommodate various cable sizes and configurations. Vulcanization, a critical process involving the application of heat and pressure, facilitates the cross-linking of rubber molecules, resulting in the desired mechanical strength, resilience, and resistance to thermal and electrical stresses. The integration of advanced molding and vulcanization technologies optimizes the dimensional accuracy and integrity of the cable connectors, ensuring compatibility with stringent performance standards and operational requirements.
Conductor Termination and Assembly: Efficient conductor termination and assembly processes are integral to the production of high-quality rubber cable connectors. Automated equipment and robotics are employed to strip, terminate, and fasten conductors to the designated connector contacts, ensuring consistent and reliable electrical connections. Additionally, assembly stations equipped with precision tools and fixtures enable the integration of connector components, insulating housings, and strain relief elements, securing the cable assemblies and safeguarding against mechanical strain and environmental hazards. The integration of automated assembly systems enhances productivity, repeatability, and quality assurance, contributing to the overall efficiency of the production line.
Quality Control and Testing: Stringent quality control measures and testing protocols are embedded throughout the production line for rubber cable connectors to ascertain compliance with industry standards and customer specifications. In-process monitoring and inspection techniques, such as dimensional checks, electrical continuity testing, and insulation resistance measurements, validate the integrity and functionality of each connector assembly. Furthermore, comprehensive end-of-line testing, including high-voltage withstand tests, mechanical durability assessments, and environmental exposure evaluations, ensures the robustness and reliability of the cable connectors in demanding operational environments.
Conclusion: The production line for rubber cable connectors exemplifies a confluence of precision engineering, material science, and automation technologies in the pursuit of delivering high-performance electrical connectivity solutions. By embracing advanced manufacturing processes, quality assurance methodologies, and continuous improvement initiatives, manufacturers can meet the evolving demands for durable, high-quality cable connectors across industries, ranging from automotive and aerospace to renewable energy and telecommunications.
The commitment to innovation, quality, and customization within the rubber cable connector production line paves the way for addressing the challenges of electrical connectivity in evolving technological landscapes and industrial applications. Collaborating with experienced industry partners and engaging in ongoing research and development endeavors contributes to the advancement of electrical connector technologies and the delivery of tailored solutions that align with specific performance, environmental, and regulatory requirements.
For further information or inquiries regarding the production line for rubber cable connectors, please feel free to contact us to explore how our expertise and capabilities can support your electrical connectivity needs.
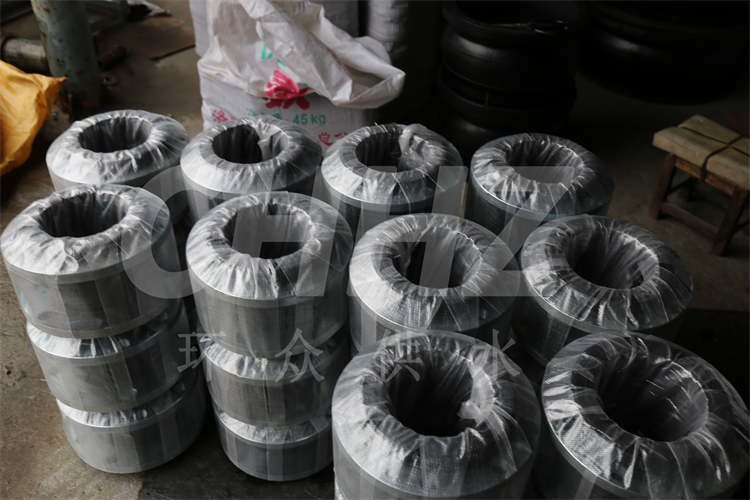