Manufacturing Methods for Rubber Flexible Connectors: A Comprehensive Overview
Rubber flexible connectors play a critical role in numerous industrial, commercial, and domestic applications. These connectors are essential for accommodating misalignment, vibration, and thermal expansion in piping systems. This article provides a comprehensive overview of the various manufacturing methods employed in the production of rubber flexible connectors, highlighting their key characteristics and applications.
Molded Rubber Fabrication: Molded rubber fabrication is a widely employed method for manufacturing rubber flexible connectors. It involves the use of molds and vulcanization processes to produce connectors with precise geometries and material compositions. The process begins with the creation of a mold that mirrors the desired connector shape. Liquid or solid rubber compounds are then introduced into the mold and subjected to heat and pressure, initiating the vulcanization process. This results in the formation of durable, resilient connectors with tailored flexibility and chemical resistance.
Mandrel-Wrapped Construction: In the mandrel-wrapped construction method, a mandrel, or form, is coated with uncured rubber or elastomeric materials. Subsequently, the rubber-coated mandrel is subjected to heat and pressure to achieve vulcanization, forming a seamless and uniform rubber tube. This manufacturing technique is particularly suitable for producing flexible connectors with smooth inner surfaces, high flexibility, and optimized tensile strength.
Fabric Reinforcement: To enhance the structural integrity and pressure-handling capabilities of rubber flexible connectors, fabric reinforcement is often incorporated during the manufacturing process. Layers of fabric, typically composed of polyester, nylon, or aramid fibers, are integrated into the rubber matrix, imparting exceptional tensile strength, tear resistance, and dimensional stability to the connectors. Fabric-reinforced connectors are well-suited for applications involving high mechanical stresses and dynamic movements.
Hand-Built Construction: Hand-built construction methods involve the manual assembly and fabrication of rubber flexible connectors. Skilled craftsmen construct these connectors by handlaying multiple plies of rubber and fabric materials, ensuring precise layer alignment and uniform thickness throughout the connector. This labor-intensive approach allows for the customization of connectors to address specific application requirements, such as size, shape, and material composition.
Applications and Considerations: Rubber flexible connectors manufactured through these methods find extensive utility in a wide range of applications, including HVAC systems, piping assemblies, industrial machinery, and automotive exhaust systems. When selecting a manufacturing method, factors such as operating conditions, fluid compatibility, temperature extremes, and mechanical stress must be carefully considered to ensure the optimal performance and longevity of the connectors.
In conclusion, the manufacturing methods for rubber flexible connectors encompass an array of techniques that enable the production of durable, adaptable, and resilient components for fluid and gas conveyance systems. By integrating advanced materials, precision manufacturing processes, and tailored reinforcement methods, manufacturers can deliver connectors tailored to meet the diverse demands of modern industrial and commercial applications.
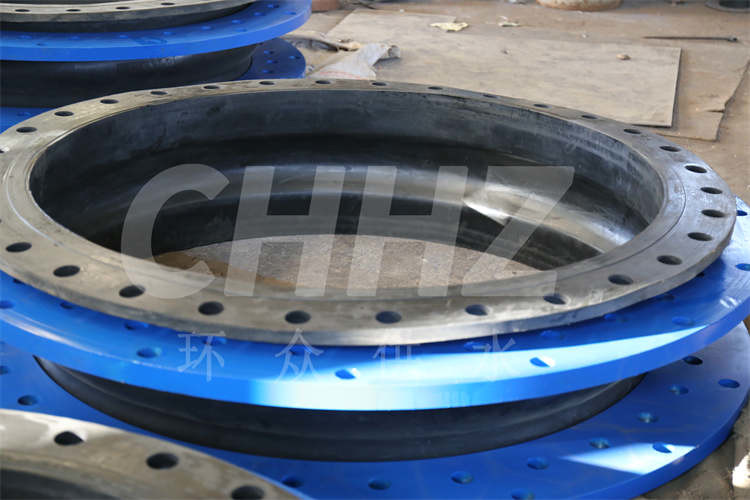