Concentric and Eccentric Rubber Joints: Understanding Their Applications
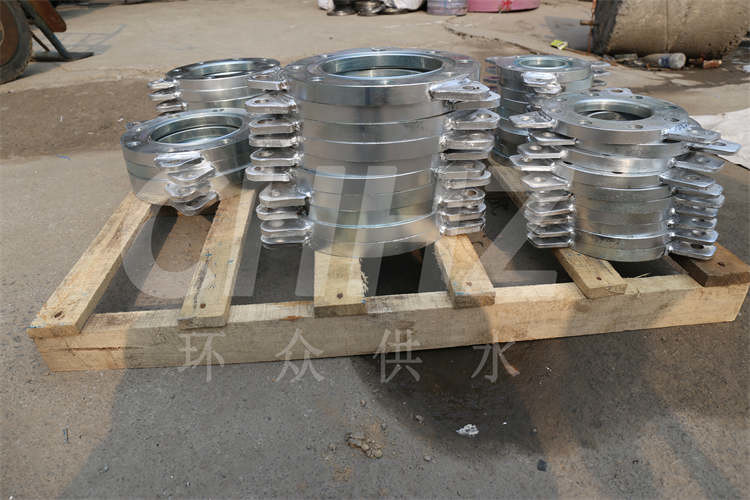
Rubber joints are essential components in piping systems, designed to absorb vibration, compensate for movement, and reduce noise. Two common variations of rubber joints are concentric and eccentric joints, each serving specific purposes in diverse industrial and commercial applications. This article aims to elucidate the characteristics and applications of concentric and eccentric rubber joints, shedding light on their distinct advantages and functions.
Concentric Rubber Joints: Concentric rubber joints, also known as straight rubber joints, feature symmetrical geometries with uniform thickness and identical inner and outer diameters. These joints are employed in piping systems where axial displacement, angular misalignment, and lateral movement need to be accommodated while maintaining a consistent flow path. Concentric rubber joints are ideal for applications where axial movement or vibration control is a primary concern, such as in HVAC systems, pump installations, and general water distribution pipelines.
Eccentric Rubber Joints: Eccentric rubber joints, on the other hand, exhibit an asymmetrical design with offset inner and outer diameters. This eccentric configuration allows for the compensation of non-uniform movement, including lateral and angular displacement in piping systems. Eccentric rubber joints find particular utility in applications where structural constraints or spatial limitations necessitate the redirection of flow or the accommodation of non-parallel pipe connections. Their ability to manage both axial and angular movements makes them suitable for use in tight or confined spaces, as well as in systems with non-standard piping configurations, such as industrial machinery, power generation facilities, and marine installations.
Key Considerations: When selecting between concentric and eccentric rubber joints, several factors should be taken into account to ensure optimal performance and longevity. These factors include the expected range of motion, operating pressures, temperature fluctuations, as well as the chemical compatibility of the joint materials with the conveyed fluids. Additionally, the design and layout of the piping system, along with space constraints and installation requirements, play a crucial role in determining the most suitable joint configuration for a given application.
Conclusion: In summary, concentric and eccentric rubber joints represent distinct solutions for managing movement, vibration, and misalignment in piping systems. By understanding the unique characteristics and applications of these joints, engineers and system designers can effectively select the appropriate joint configuration to address the specific demands of their projects. Whether it is maintaining a smooth, uninterrupted flow path or accommodating complex piping layouts, concentric and eccentric rubber joints play a vital role in ensuring the reliability and longevity of diverse piping systems across various industries.
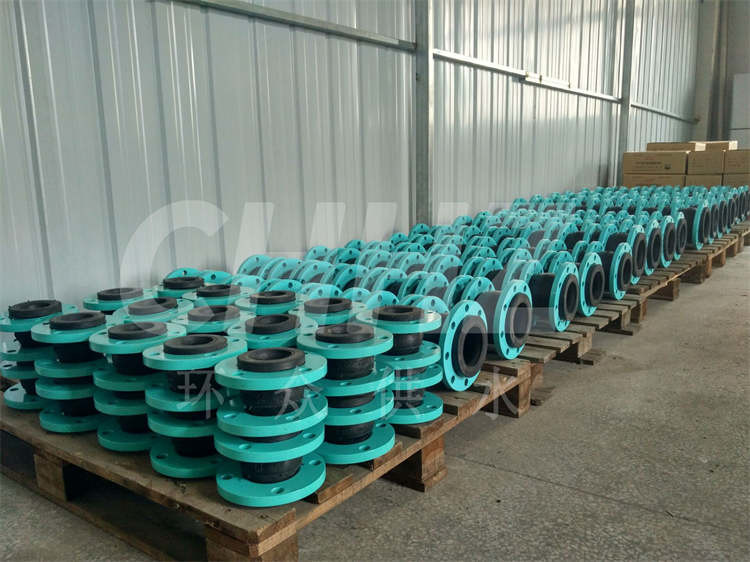