Designing assembly fixtures for automotive rubber hose joints
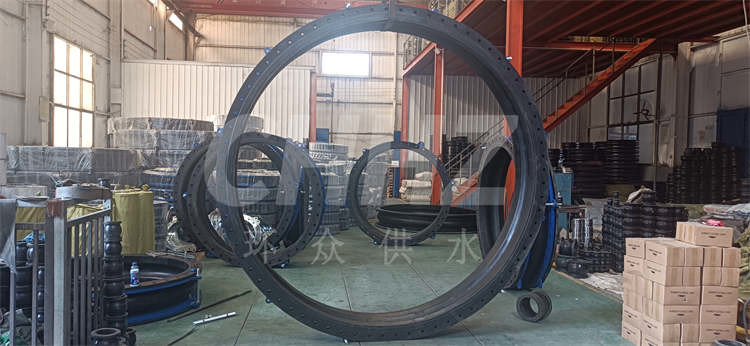
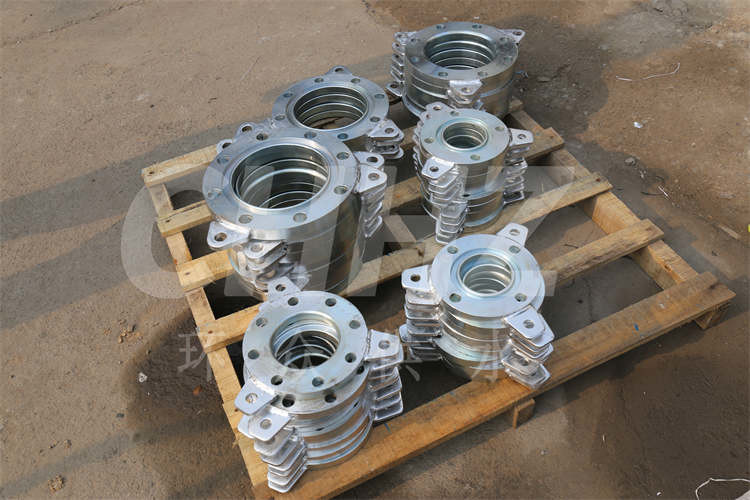
Designing assembly fixtures for automotive rubber hose joints is a critical aspect of the manufacturing process. These fixtures play a key role in ensuring the accurate and efficient assembly of rubber hose joints, which are essential components in automotive fluid transfer systems such as fuel lines, coolant hoses, and hydraulic systems. The following article provides an overview of the key considerations and best practices in the design and use of assembly fixtures for automotive rubber hose joints.
The primary objective of assembly fixtures is to securely and precisely position the components to be assembled, facilitating the efficient and consistent assembly process. When it comes to rubber hose joints, assembly fixtures must accommodate various hose diameters, shapes, and end configurations. Additionally, the fixtures should provide the necessary support and alignment for mating the hose ends with other components, such as connectors, pipes, or fittings.
In the design of assembly fixtures, engineers must consider the specific requirements of the rubber hose joint assembly process. This includes the need for proper clamping and positioning mechanisms that can hold the flexible hose in place without causing damage or deformation. An emphasis on ergonomics and ease of use is also essential to ensure that assembly line workers can effectively utilize the fixtures for repetitive tasks.
The use of modular and adjustable components in assembly fixtures can enhance their versatility and adaptability to different hose configurations. This can be particularly beneficial in automotive manufacturing environments where multiple hose sizes and types are used across different vehicle models. Additionally, incorporating quick-change features and intuitive adjustment mechanisms can contribute to improved productivity and reduced changeover times during assembly line operations.
Furthermore, the materials and surface finishes used in assembly fixtures must be carefully selected to prevent damage to the rubber hose and ensure that the fixtures themselves are durable and long-lasting. Considerations such as non-abrasive contact surfaces, corrosion resistance, and ease of cleaning should be taken into account in the selection of materials for the fixtures.
The integration of sensors or inspection features into assembly fixtures can also serve to enhance quality control during the assembly process. For instance, the incorporation of position sensors or vision systems can verify proper hose alignment and engagement, ensuring that each assembly meets the required specifications.
In conclusion, the design and implementation of assembly fixtures for automotive rubber hose joints are crucial for achieving the desired efficiency, accuracy, and quality in the assembly process. By focusing on considerations such as adaptability, ergonomics, material selection, and quality control features, manufacturers can develop effective fixture solutions that contribute to the overall reliability and performance of automotive fluid transfer systems. Through the thoughtful design and utilization of assembly fixtures, automotive manufacturers can streamline their production processes and produce high-quality rubber hose joint assemblies for use in vehicle applications.
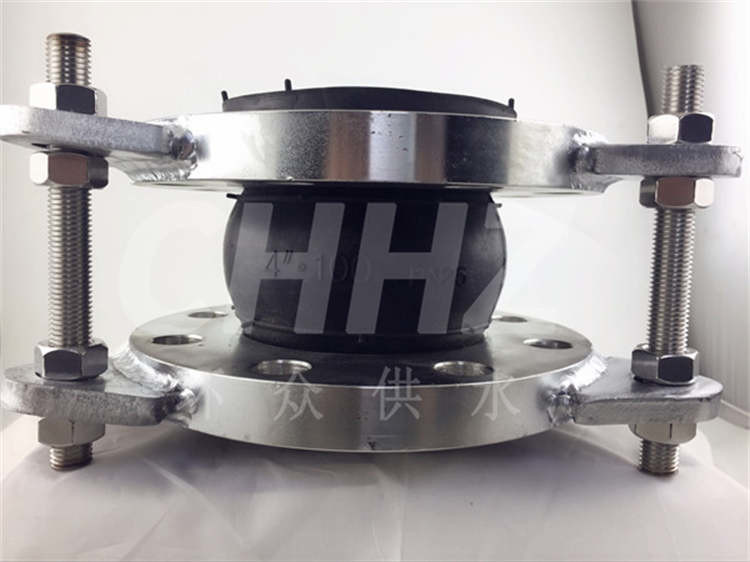